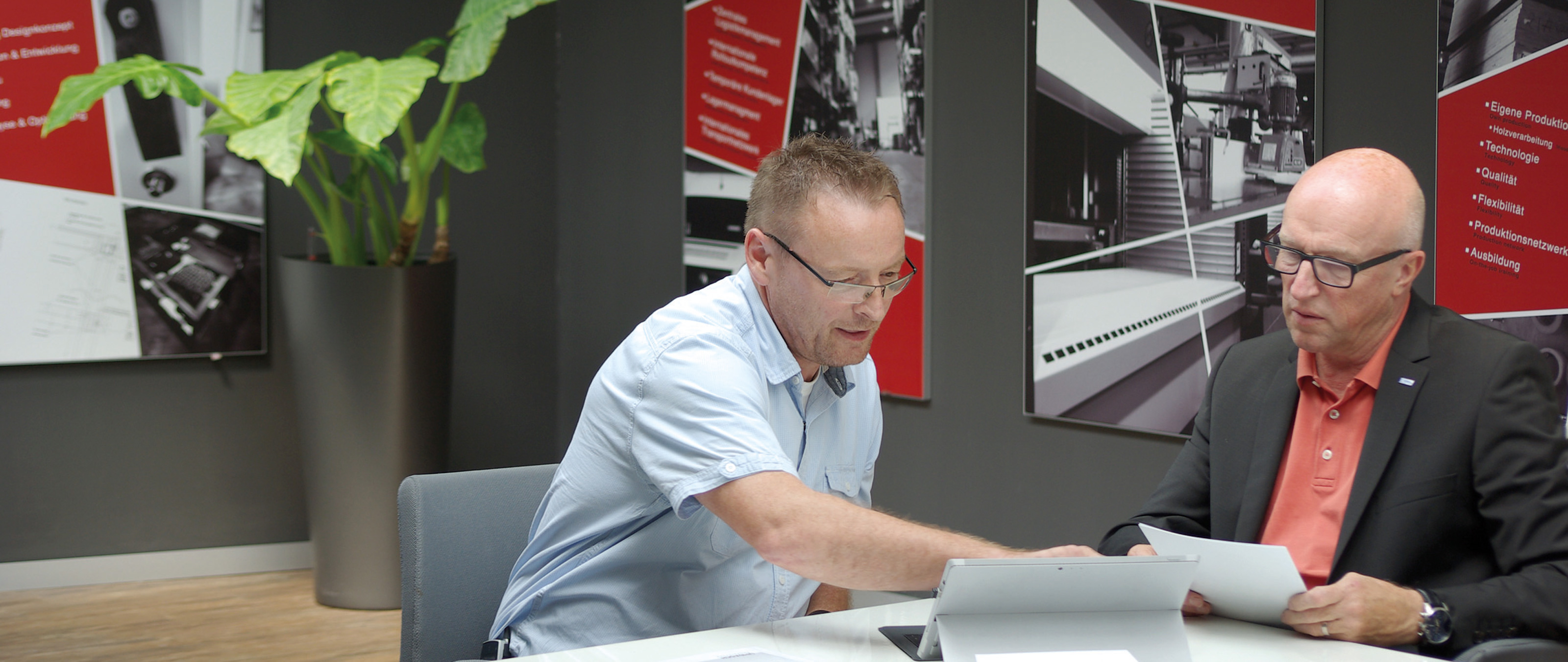
Ein Artikel des Fachmagazins HOB, Ausgabe 09/2015. Hier lesen Sie das HOB-Magazin Online.
Paradigmenwechsel in der Fertigung
Mit einer neuen Lager-Säge-Kombination hat Umdasch Shopfitting in Neidenstein den grundlegenden Umbau der Fertigung eingeläutet. Künftig in eine verkettete Produktion eingebaut, spielt die Anlage schon heute entscheidende Vorteile aus.
Umdasch Shopfitting, ein führender Hersteller ganzheitlicher, anspruchsvoller Ladenbau-Lösungen, unterzieht derzeit sein Produktionskonzept am Standort Neidenstein einem grundlegenden Paradigmenwechsel. Während man heute noch auf unterschiedlichen Niveaus unverkettet fertigt, soll künftig per Assembly Line produziert werden. Die Strategie dazu heißt Vision 2020. Bei Losgrößen von 1 bis 250 Stück
setzt Umdasch prinzipiell eine auftragsbezogene und eine Fertigung auf Lager um, auf die man sich auch künftig technologisch einstellen wird. Dabei sollen die Aufträge mit größeren Stückzahlen auf einer Hauptlinie bearbeitet werden, während man die Aufträge mit der Stückzahl eins oder drei auf Bypass-Linien legt und je nach Auslastung einschleust. „Wir werden in Zukunft also zwei Linien fahren: eine Highspeed- und eine etwas langsamere Linie, wobei die Abarbeitung nach Menge sowie Termin priorisiert wird“, sagt Uwe Rimmler, Bereichsleiter Produktion, Logistik und SUI bei Umdasch Shopfitting. „Der Hintergrund ist: Unsere Kunden wünschen immer mehr den schnellen Termin, wodurch die Durchlauf zeiten von der Auftragserteilung bis zur Auslieferung und Montage immer kürzer werden.“
Den ersten Schritt in Richtung Neustrukturierung hat Umdasch mit einer Lager-Säge-Kombination von Holzma und Homag Automation getan, die Ende letzten Jahres in Betrieb ging. Dabei handelt es sich um eine Anlage aus Flächenlager TLF 411 und Winkelanlage HKL 300 profiLine. In einem weiteren Schritt wird derzeit gerade die Halle saniert, während im nächsten Jahr die Sanierung der kompletten Heiz- und Energieanlage folgt. Daran werden sich diverse Investitionen im Maschinenbereich anschließen.
Viele Argumente für den Umstieg
Schon bis 2014 hatte Umdasch mit einer Lager- Säge-Kombination von Bargstedt, heute Homag Automation, und Holzma gearbeitet, die aus einem Flächenlager und der Plattenaufteilsäge HPV 11 bestand. „Mit dieser Anlage, die damals in der Mitte der Halle stand, produzierten wir in zwei Hallenrichtungen. Dabei war ein Werkstück durchschnittlich 921 m unterwegs. Mit der neuen Anlage, die nun am Beginn der Halle aufgestellt wurde, sind es 322 m. Das war schon mal der erste Effizienzschritt, den wir mit der Lager-Säge-Kombination erreicht haben“, so Rimmler. Dass die Säge am Anfang der Halle auch mittig aufgestellt wurde, ist wieder in die Zukunft gedacht: Denn an die drei Anschlussrichtungen für Folgeprozesse der Winkelanlage sollen in den nächsten Jahren verschiedene Technologien angebunden werden. Nesting und Digitalprint werden wohl dazugehören. Zugleich gab es eine Reihe weiterer Punkte, die für die Investition in ein neues Lager-Säge-Konzept sprachen. Das fing mit den Wartungs- und Instandhaltungskosten an, die nach 15 Jahren Zweischichtbetrieb bei der alten Anlage deutlich gestiegen waren. Und ging mit den Toleranzen schnell weiter, die beim Zuschnitt immer größer wurden. „Außerdem hatte die Analyse unserer Teile ergeben, dass nur ein bis zwei Prozent davon länger als 2,80 m sind. Also stellten wir auf Halbmaßplatten um“, berichtet Rimmler. „Bis dahin waren die Großformate mit ineffizienten Wegen vom Lager zur Säge von bis zu 50 m verbunden. Aber auch der Platzbedarf des Lagers selbst war enorm.“ Weil man bis dahin viel Zeit mit dem Umsetzen der Platten und den langen Wegen verloren hatte, wollte man zudem eine effiziente Lager-Software und eine automatische Etikettierung, durch die das Lager weiß, wo jede Platte sitzt. Ganz vorn auf der Agenda des Bereichsleiters stand jedoch die Effizienzsteigerung. Er wollte schneller werden.
Aber auch ergonomischer. „Wenn wir zuschneiden, erhalten wir teilweise 5 m lange und 60 cm breite Streifen. Durch die Säge mit einer Schnittlinie mussten diese Streifen früher manuell gedreht, angelegt und wieder geschnitten werden.“ Nicht zuletzt sollte der entstehende Abfall effizienter entsorgt werden.
Anforderungen erfüllt
„Bedingt durch diese Anforderungen, die von der Effizienzsteigerung über die Reduzierung beeinflussbarer Zeiten durch das Bedienpersonal und eine planungssichere Software mit regelmäßigen Updates bis hin zur effizienten Abfallentsorgung reichten, waren wir sehr schnell bei dem Konzept Winkelanlage mit allen Features, die eine solche Säge heute bieten kann“, sagt Martin Kress, Produktmanager von Holzma. Kombiniert wurde die Holzma HKL 300 profiLine mit einem Flächenlager TLF 411, die beide im letzten Jahr ihre Arbeit aufnahmen. Seither wurden Erfahrungen gesammelt, wie die Anlage den unterschiedlichen Anforderungen gerecht wird.
Weil die Materialanalysen von Umdasch zu einer Reduzierung großformatiger Platten geführt hatten, zielte das Unternehmen auf ein möglichst kleines, effizientes Lager. Ohnehin brauchte die schnellere Winkelanlage kein Lager der vormaligen Größe. Das neue Flächenlager ist heute halb so groß wie das alte. Während man früher ein Innen- und ein Außenlager nutzte, ist nach dem Einbuchen inzwischen alles in einem System. „Über die leistungsfähige Software und die einzelnen Lagerplätze haben wir einen deutlich schnelleren Zugriff auf das Material und besitzen stets den Überblick, was in den einzelnen Stapeln liegt“, sagt Rimmler. „Beim Einlagern denkt das System weit voraus und legt die große Zahl unserer Platten optimiert ab.“ In der Konstellation Lager steuert Säge weiß das Lager, wann die Winkelanlage eine bestimmte Platte braucht. Freie Zeiten nutzt es zum Umstapeln, sodass eine benötigte Platte zum richtigen Zeitpunkt zur Verfügung steht. Dabei lernt das Lager die Häufigkeit, mit der ein bestimmtes Material bewegt wurde und setzt entsprechende Stapel selbstständig näher zur Säge. Anders als beim alten Lager wird dafür eine Saugtraverse genutzt, die ST 71, die je nach Platte diagonal verfahren und sich drehen kann. „So nehmen wir heute jede Platte bis 4 mm Stärke auf und können die vorhandene Fläche im Lager viel besser nutzen: Weil jede Platte vermessen wird, lassen sich die Platten einfach enger setzen“, berichtet Rimmler.
Mehr als 40 Prozent schneller
„Nach der Installation der Anlage haben wir einen Monat lang die Zuschnittdaten aufgenommen und ausgewertet“, erzählt Kress. „Dabei hat sich herausgestellt, dass die neue Anlage bei gleichen Zuschnittdaten 42 Prozent schneller als die alte ist.“ Anfänglich erwartete man bei Umdasch einen Effizienzsprung von 20 Prozent. „Heute wissen wir: Sobald wir größere Lose zuschneiden, sind wir schneller als 42 Prozent“, so Rimmler. „Bei Objekten mit fünf oder sechs verschiedenen Materialien kommen wir auf 20 Prozent. Da wir augenblicklich über 50 Prozent unserer Produkte ins Lager und damit höhere Stückzahlen produzieren, liegen wir immer über 30 Prozent. Das wirkt sich so aus, dass bei üblichem 3-Schicht-Betrieb im Haus nur zweischichtig zugeschnitten werden muss. Dadurch sinkt der Druck auf die Vorfertigung und die Mitarbeiter und wir haben die gefordert hohe Qualität.“
Momentan ist es bei Umdasch noch so, dass auch Pakete bis drei Platten zugeschnitten werden. „Unsere Analysen haben ergeben, dass sich der Paketschnitt in Richtung 1,2 bis 1,5 Platten entwickelt. Dieser Trend in Richtung Einzelplatte gilt auch für klassische Laden-, Möbel- und Messebauer“, sagt Kress. „Künftig werden auch wir wohl keine Pakete mehr zuschneiden, weil wir Möbel im Durchlauf komplett fertig produzieren wollen“, bestätigt Rimmler. „Unter Umständen nehmen wir dabei den etwas langsameren Durchlauf an der Säge in Kauf, um jedoch über den gesamten Fertigungsablauf schneller zu werden. Die großen Lager für unsere Produkte sind dann wahrscheinlich nicht mehr erforderlich, weil wir auch die auf Lager gefertigten Produkte kurzfristig herstellen können.“
Informationen effizient weitergeben
Etikettiert werden die geschnittenen Platten derzeit einmal von einem automatischen Drucker am Druckbalken und im geringen Prozentsatz von einem manuellen Spender, sobald im Paket verarbeitet wird. Bei einem Dreierpaket etwa wird das erste Etikett automatisch oben aufgebracht, während die beiden unteren Platten über den Handspender gekennzeichnet werden. „Mit den Etiketten laufen umfangreichere Informationen als früher mit. Praktisch könnten damit auch Bearbeitungsprozesse initiiert werden“, sagt Rimmler. „Allerdings wollen wir künftig auch hier einen Schritt weitergehen: Wir wollen mit RFID arbeiten.“ Dann soll nicht nur das Teil gescannt werden, um dann Programme zu laden und die Bearbeitung zu initiieren; RFID könnte für Umdasch auch das lagerbestandführende System werden. Dann wüsste man stets von jedem Teil, wo es sich gerade befindet. Und in der Fertigung könnte von Maschine zu Maschine der Abschluss der Bearbeitung ans System gemeldet werden. Per Etikett transportiert man im Augenblick Informationen wie Auftragsnummer, Fertigungsendtermin oder Verladetermin. Die Bearbeitungsalgorithmen sollen in Zukunft per CAD/CAM-Anbindung direkt übergeben werden. Nicht zuletzt deshalb gibt es die Strategie, künftig über alle Systeme eine Leit-Software zu setzen. Cobus ist hier das Stichwort. „Auch hier sind wir in den ersten Gesprächen für ein übergreifendes System, mit dem wir die verschiedensten Fertigungstechnologien ansteuern können“, sagt der Bereichsleiter. Inzwischen ist die Holzma Lager-Säge-Kombination für Umdasch der erste Platzhalter der geplanten Fertigungsvision 2020. Der wichtigste Punkt, der damit schon heute erfüllt wurde, ist die deutliche Leistungssteigerung. An zweiter Stelle kommt die verbesserte Ergonomie, die mit einer erhöhten Zufriedenheit der Mitarbeiter einhergeht. „Nur wenn ich zufriedene Mitarbeiter habe, bekomme ich die PS auf die Straße“, weiß Rimmler. „Schon bei der ersten Schulung haben unsere Mitarbeiter gemerkt, dass wir einen Quantensprung bei der Bedienoberfläche machen.“ Außerdem ist die Geräuschkulisse heute merklich geringer. Wenn man in die Halle geht, hört man das Lager gar nicht und die Säge nur bei bestimmten Materialien. Deutlich ergonomischer ist für die Mitarbeiter auch die Restebeseitigung, die automatisch vonstattengeht. Reststücke fasst heute niemand mehr an. Und auch lange, schwere Abschnitte müssen nicht mehr gehandelt werden. „Die vorgegebenen Toleranzen beim Zuschnitt halten wir heute mit deutlich weniger Aufwand sicher ein“, berichtet Rimmler weiter. „Nicht zuletzt ist das aufgeräumte Lager für uns ein Aushängeschild. Schließlich präsentieren wir Kunden regelmäßig unsere Fertigung, um gläsern zu sein und Vertrauen zu schaffen.“
Es geht weiter
Im Augenblick ist Rimmler gerade dabei, Daten für ein Durchlaufbohraggregat einzuholen. „Unsere Analysen sagen uns, dass auf dem jetzigen BAZ nur vier Prozent Formteile gefertigt werden, über 90 Prozent sind rechteckige Teile“, so der Bereichsleiter. „Diese Erkenntnisse werden in den Kauf des Bohraggregates einfließen, wo die Homag Group für uns wieder ein interessanter Ansprechpartner ist.“
Foto: HOB Fachmagazin / Michael Hobohm
„Unsere Kunden wünschen immer mehr den schnellen Termin, wodurch die Durchlaufzeiten von der Auftragserteilung bis zur Auslieferung und Montage immer kürzer werden.“Uwe Rimmler, Bereichsleiter Produktion, Logistik und SUI bei Umdasch Shopfitting