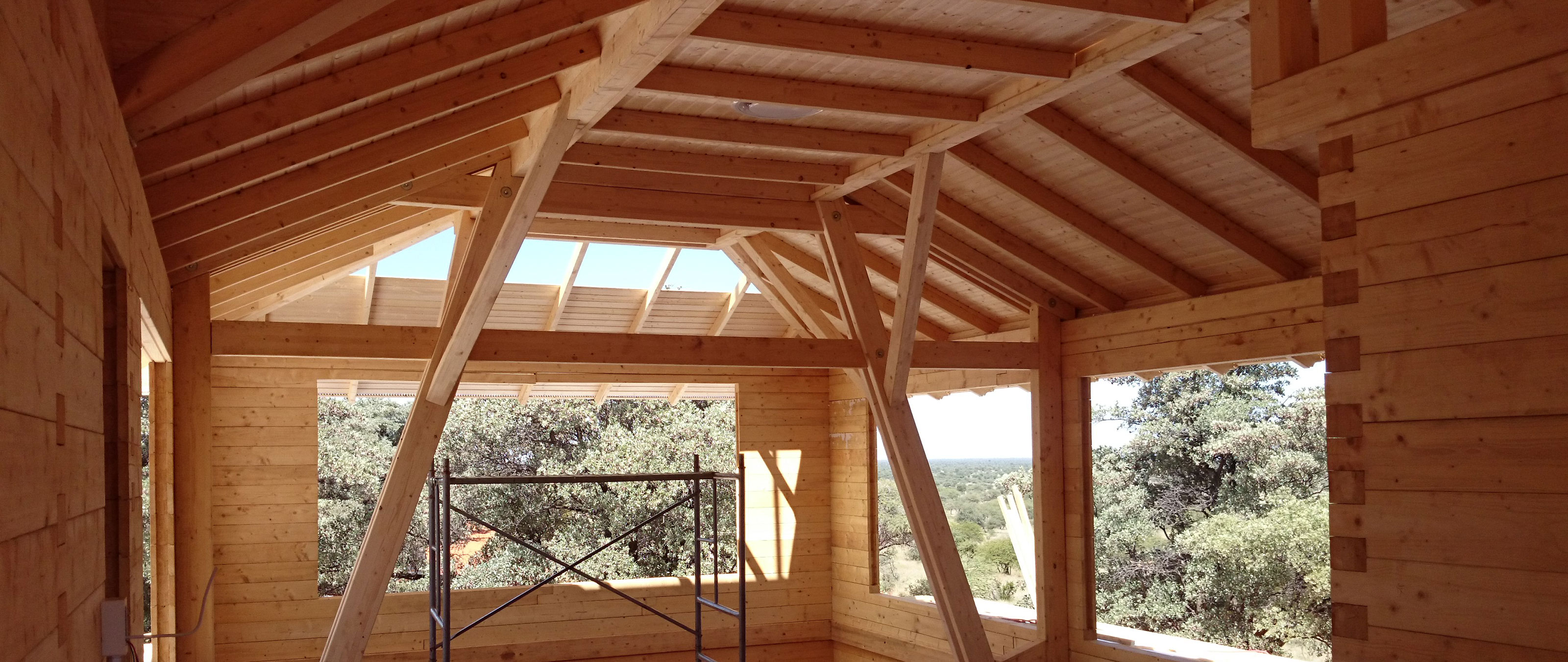
An article from the WEINMANN customer magazine Performance, Version 15/ 2016. Here you can read the customer magazine Performance online.
The interview was conducted from company WEINMANN Holzbausystemtechnik GmbH.
Performance:
Mr. Hess, in 2007 you founded the Holzbau Carpentry Hess company in Namibia. What gave you the idea to found a carpentry business in Namibia and how is the business doing?
Christian Hess:
I have always been very interested in different cultures and countries and I have always traveled a lot. I felt very comfortable in Namibia and so I decided to emigrate there. When I founded the carpentry business in Namibia in 2007, there were just two of us. My apartment also served as the workshop and this is where we did all of the work. At that time, we mainly laid laminate floors. Carpentry as a job and the use of timber as a construction material were largely unknown. Gradually, we were able to build up a customer base and transformed timber construction in to a more familiar concept.
The company's first large order came as a result of a fire in an old sports hall that also served as the court building. A German construction company approached us to ask if we could produce the braces. We actually ended up producing the entire roof framework. The hall was in the center of the city, which meant that people found out about the project very quickly and we received some more orders as a result. Up until this point, we were using only South African timber for production but for the second project we imported solid construction timber from Germany. At that time we were importing two containers per year. In 2014, this had risen to 23 containers — approx. 1000 m³ of timber. However, it was proving very difficult to import larger beams so we decided to purchase only the raw materials and to glue the timber ourselves. I took a course at Stuttgart University to acquire the relevant knowledge. Since 201, we have been working with a 30-year-old compact finger jointer to produce glued timber via a fully automated process. This makes us the only business in Africa that produces, cuts and installs glued timber up to a length of 30 m.
Performance:
What persuaded you to invest in a WEINMANN carpentry machine?
Christian Hess:
I have always been a firm believer in traditional workmanship and never wanted a carpentry machine. In 2013, we were processing 100 m³ by hand every month, and a large part of that work was complex roof frameworks with a lot of mitering. As land prices in Namibia are extremely low, buildings tend to be very spacious, meaning that diagonal and angled processing is very common. Due to this high workload and after talking to my foreman and employees, I decided to invest in a carpentry machine.
During my research for a suitable machine, the size of the machine was a very important consideration for keeping the transportation process easy and cost-efficient. The hall was also already finished and I didn't want to have to do any modifications for machine foundations, for example. As the power supply lines in Namibia are problematic, it was also important to me that the machine was energy efficient. As you would expect, the precision of the processing format was also a deciding factor, particularly because most of our roof frameworks are visible and we want to deliver high-quality products to our customers.
After various bits of research and discussions with fellow carpenters, I decided on theWEINMANN carpentry machine WBS 140, which had just been launched on the market. The machine is compact, small and precise, meaning that it fully satisfied our requirements. Once the WBS had been delivered, it only had to be set up and after just three days, we were able to press the first button and start the machine. We were impressed.
Performance:
What products do you manufacture with the WEINMANN carpentry machine? What are the special features of your products?
Christian Hess:
Regardless of whether we need dovetail joints, miter cuts or any other format, the machine copes with it all and completes all of the processing precisely and cleanly. This high quality level is exactly what we need with the high number of open roof frameworks that we produce.
At the start of 201, we erected a two-story block house and produced all of the beams using the WEINMANN carpentry machine. We also test a wide variety of processing formats — regardless of whether it's braces, tables or any other form of joint, we use the WBS for everything. Given that time is not such an important factor to us compared to the situation in Germany, we can use the WBS to test a range of different processing formats. In contrast, the material is much more important and therefore it's important that we keep waste to a minimum. Thanks to the automated setup, we can do a lot more and we have been able to increase our sales by 30%. The machine has already paid for itself in just its third year. The machine is very important to me now, and I would not be able to do without it.
Performance:
How does the WEINMANN service work at such a great distance?
Christian Hess:
The WEINMANN service is one hundred percent reliable. Regardless of whether it's a Saturday or after the end of the working day, someone is always available. Contact is fast and a great help. The Internet connection is also very good for African standards, and so we have never had any problems with software updates, for example. To keep the machine working without any problems, an employee from WEINMANN visits once a year to perform maintenance. This arrangement is also reliable and it works very well.
Performance:
How do you see the situation developing in the future?
Christian Hess:
At the moment we have 17 employees, including me and a foreman from Germany, as well as two other Namibian-German skilled workers. One of these employees has already completed carpentry training in Germany and is a journeyman. As it is very difficult to get a work or residency visa for Namibia, I try to give my local personnel good training in Germany.
And we have some very interesting projects coming up in the next couple of years: Over the course of the next two to three years, we have a project planned that involves constructing 20 block houses in the desert. And in spring 2016, we will be manufacturing a roof that consists of 20 gable roof trusses for an industrial hall. The trusses are 27 m long and 2. m high in the center — they will probably be the largest trusses in Africa. We will also manufacture a lodge, consisting of three timber construction houses. The external side of the walls will be a timber casing, protected with a corrugated polycarbonate panel, rather than a rendered facade. This protection layer is very important due to the extreme exposure to sunlight. I first saw this type of construction in long-term trials at Stuttgart University and now I am using it. Contact and my connection with Germany have always been very important to me. I therefore maintain relationships with various companies in the industry as well as engineering companies, and I regularly visit leading trade fairs. As you can see, there is no time to be bored — there are always new and interesting projects in the pipeline. So the future promises to be exciting, too.
Performance:
Thank you for taking the time to speak to us, Mr. Hess.
Source/ Image rights:
Holzbau Carpentry Hess, NamibiaPerformance:
Mr. Hess, in 2007 you founded the Holzbau Carpentry Hess company in Namibia. What gave you the idea to found a carpentry business in Namibia and how is the business doing?
Christian Hess:
I have always been very interested in different cultures and countries and I have always traveled a lot. I felt very comfortable in Namibia and so I decided to emigrate there. When I founded the carpentry business in Namibia in 2007, there were just two of us. My apartment also served as the workshop and this is where we did all of the work. At that time, we mainly laid laminate floors. Carpentry as a job and the use of timber as a construction material were largely unknown. Gradually, we were able to build up a customer base and transformed timber construction in to a more familiar concept.
The company's first large order came as a result of a fire in an old sports hall that also served as the court building. A German construction company approached us to ask if we could produce the braces. We actually ended up producing the entire roof framework. The hall was in the center of the city, which meant that people found out about the project very quickly and we received some more orders as a result. Up until this point, we were using only South African timber for production but for the second project we imported solid construction timber from Germany. At that time we were importing two containers per year. In 2014, this had risen to 23 containers — approx. 1000 m³ of timber. However, it was proving very difficult to import larger beams so we decided to purchase only the raw materials and to glue the timber ourselves. I took a course at Stuttgart University to acquire the relevant knowledge. Since 201, we have been working with a 30-year-old compact finger jointer to produce glued timber via a fully automated process. This makes us the only business in Africa that produces, cuts and installs glued timber up to a length of 30 m.
Performance:
What persuaded you to invest in a WEINMANN carpentry machine?
Christian Hess:
I have always been a firm believer in traditional workmanship and never wanted a carpentry machine. In 2013, we were processing 100 m³ by hand every month, and a large part of that work was complex roof frameworks with a lot of mitering. As land prices in Namibia are extremely low, buildings tend to be very spacious, meaning that diagonal and angled processing is very common. Due to this high workload and after talking to my foreman and employees, I decided to invest in a carpentry machine.
During my research for a suitable machine, the size of the machine was a very important consideration for keeping the transportation process easy and cost-efficient. The hall was also already finished and I didn't want to have to do any modifications for machine foundations, for example. As the power supply lines in Namibia are problematic, it was also important to me that the machine was energy efficient. As you would expect, the precision of the processing format was also a deciding factor, particularly because most of our roof frameworks are visible and we want to deliver high-quality products to our customers.
After various bits of research and discussions with fellow carpenters, I decided on theWEINMANN carpentry machine WBS 140, which had just been launched on the market. The machine is compact, small and precise, meaning that it fully satisfied our requirements. Once the WBS had been delivered, it only had to be set up and after just three days, we were able to press the first button and start the machine. We were impressed.
Performance:
What products do you manufacture with the WEINMANN carpentry machine? What are the special features of your products?
Christian Hess:
Regardless of whether we need dovetail joints, miter cuts or any other format, the machine copes with it all and completes all of the processing precisely and cleanly. This high quality level is exactly what we need with the high number of open roof frameworks that we produce.
At the start of 201, we erected a two-story block house and produced all of the beams using the WEINMANN carpentry machine. We also test a wide variety of processing formats — regardless of whether it's braces, tables or any other form of joint, we use the WBS for everything. Given that time is not such an important factor to us compared to the situation in Germany, we can use the WBS to test a range of different processing formats. In contrast, the material is much more important and therefore it's important that we keep waste to a minimum. Thanks to the automated setup, we can do a lot more and we have been able to increase our sales by 30%. The machine has already paid for itself in just its third year. The machine is very important to me now, and I would not be able to do without it.
Performance:
How does the WEINMANN service work at such a great distance?
Christian Hess:
The WEINMANN service is one hundred percent reliable. Regardless of whether it's a Saturday or after the end of the working day, someone is always available. Contact is fast and a great help. The Internet connection is also very good for African standards, and so we have never had any problems with software updates, for example. To keep the machine working without any problems, an employee from WEINMANN visits once a year to perform maintenance. This arrangement is also reliable and it works very well.
Performance:
How do you see the situation developing in the future?
Christian Hess:
At the moment we have 17 employees, including me and a foreman from Germany, as well as two other Namibian-German skilled workers. One of these employees has already completed carpentry training in Germany and is a journeyman. As it is very difficult to get a work or residency visa for Namibia, I try to give my local personnel good training in Germany.
And we have some very interesting projects coming up in the next couple of years: Over the course of the next two to three years, we have a project planned that involves constructing 20 block houses in the desert. And in spring 2016, we will be manufacturing a roof that consists of 20 gable roof trusses for an industrial hall. The trusses are 27 m long and 2. m high in the center — they will probably be the largest trusses in Africa. We will also manufacture a lodge, consisting of three timber construction houses. The external side of the walls will be a timber casing, protected with a corrugated polycarbonate panel, rather than a rendered facade. This protection layer is very important due to the extreme exposure to sunlight. I first saw this type of construction in long-term trials at Stuttgart University and now I am using it. Contact and my connection with Germany have always been very important to me. I therefore maintain relationships with various companies in the industry as well as engineering companies, and I regularly visit leading trade fairs. As you can see, there is no time to be bored — there are always new and interesting projects in the pipeline. So the future promises to be exciting, too.
Performance:
Thank you for taking the time to speak to us, Mr. Hess.