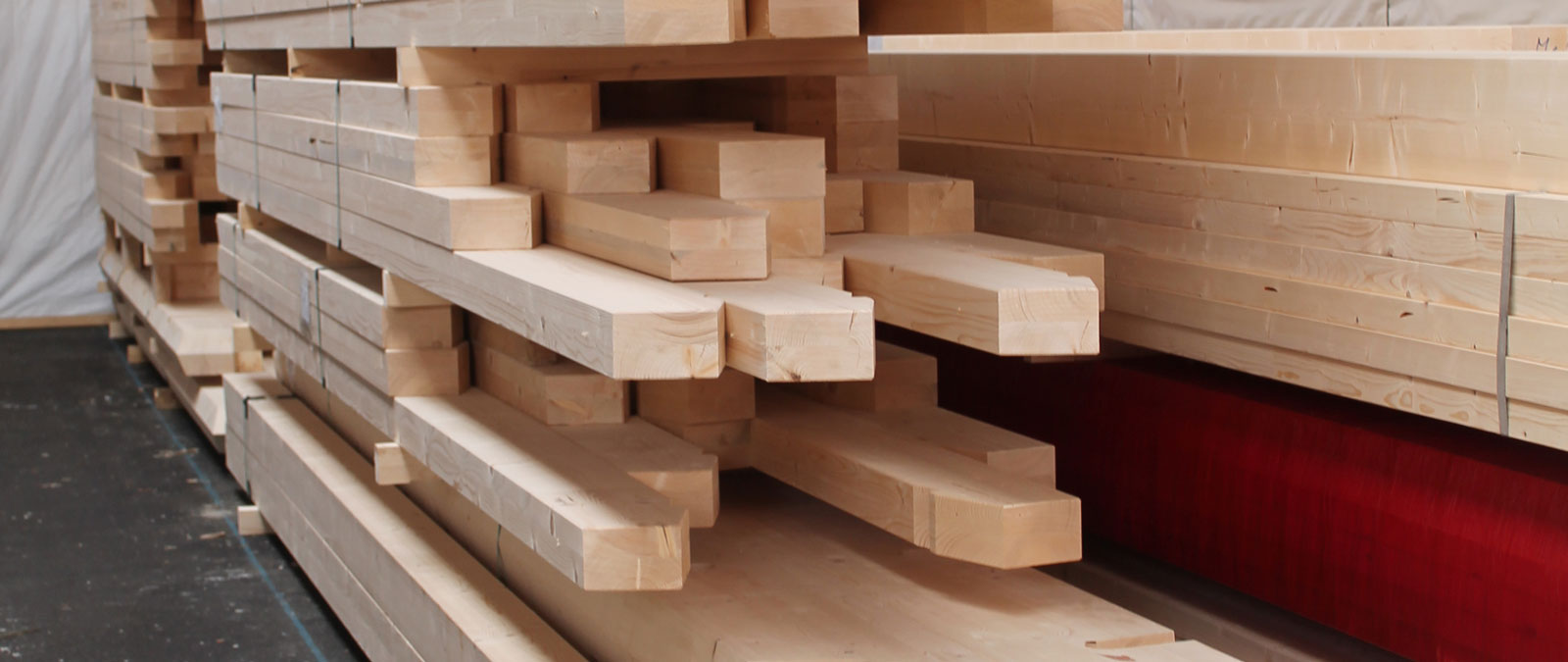
Eine gut ausgelastete Abbundanlage bindet im Jahr zwischen 1700 und 2200 Kubikmeter Holz ab. Die Leistung kann je nach Maschine, Abbundart und Projekt unterschiedlich sein und liegt bei ein bis zwei Kubikmetern pro Stunde. Bei geringerem Produktionsvolumen gilt es bei der Entscheidung zahlreiche Aspekte zu berücksichtigen.
«Eine CNC-Anlage ist durchaus auch ein Prestigeobjekt.»
Vor rund zehn Jahren gab es schweizweit eine Investitionswelle in den Abbund. Kaufte die erste Zimmerei im Dorf eine Abbundmaschine, konnten direkt Wetten abgeschlossen werden, bis wann das nächste Holzbauunternehmen nachziehen würde. Eine CNC-Anlage ist durchaus auch ein Prestigeobjekt – allerdings gibt das kaum jemand offen zu. Es bestehen viele Gründe dafür, warum eine Zimmerei ihre eigene Abbundanlage braucht – dabei hat sich die Argumentation in den letzten Jahren wenig geändert. Die beiden Hauptaspekte für die Anschaffung sind einerseits die Flexibilität und andererseits die Wertschöpfung, die damit im eigenen Unternehmen gehalten werden kann. Doch die Auswirkungen, die eine solche Investition auf das Unternehmen hat, werden oft zu wenig beachtet.
Flexibilität erreichen
Für die meisten Holzbauunternehmen ist die Flexibilität in der Produktion das Wichtigste. «Ich muss kurzfristig auf die Bedürfnisse der Kunden und auf wechselnde Terminplanungen reagieren können» lautet ein Argument. Doch wie oft gab es im letzten Jahr tatsächlich den Fall im Unternehmen, dass in kürzester Zeit eine grössere Menge an Teilen benötigt wurde? Und würde sich der Bedarf bestätigen, wenn im Abbund eine Liste darüber geführt wird, welche Teile nachträglich als Express und ohne Vorwarnung abgebunden werden mussten? In einem Beispiel aus der Praxis waren es im Rückblick drei konkrete Fälle im Jahr, in denen Teile mit einigem Aufwand nachgefertigt werden mussten.
Arbeitsabläufe organisieren
Die Erfahrung zeigt, dass die meisten Nachfertigungen diejenigen Teile betrifft, die in der Elementfertigung oder auf dem Bau nicht gefunden wurden. Oft sind dies Teile, die falsch verbaut oder nicht in der richtigen Reihenfolge bereitgestellt wurden. Organisatorische Probleme solcher Art könnten mit einfachen Massnahmen reduziert werden. Eine weitere Ursache liegt oft in der verspäteten Arbeitsvorbereitung. Die Aufbereitung der CAD-Daten benötigt meist mehr Zeit als angenommen. Ein weiterer Punkt ist der Holzvorrat. Um Teile als Expressauftrag abbinden zu können, ist auch das passende Rohmaterial in der benötigten Qualität und Dimension am Lager erforderlich. In dieser Situation hat ein Abbundwerk andere Rohmaterialvorräte und kann auch grössere Mengen bereitstellen. Beim externen Abbund braucht es allerdings eine frühzeitige Diskussion über Termine und Kapazitäten. Je früher diese bekannt sind, umso sicherer ist die Liefertreue. In der Praxis eines Abbundwerks mit Zwei-Schicht-Betrieb besteht in der Regel sogar mehr Flexibilität als in einem Unternehmen mit nur einem ausgebildeten Mitarbeiter im Abbund. Hinzu kommt, dass das regionale Abbundwerk einen guten Kunden nicht verlieren will und deshalb das Unmögliche möglich macht – so wird auch mal mit nur zwei Teilen zum Kunden gefahren.
Wertschöpfung sichern
Holzbauunternehmen sind bestrebt, so viel wie möglich selber zu machen. Das bringt Wertschöpfung und sichert die Auslastung der eigenen Mitarbeitenden. Wertschöpfung entsteht jedoch nur, wenn der Kunde den Preis für die Leistung auch bezahlt. Dieser Preis muss höher sein, als die eigenen Kosten für dieselbe Leistung wären. Bezüglich der Kostenwahrheit nehmen es manche Unternehmen nicht wirklich genau; Quersubventionierungen zugunsten des Abbunds sind üblich. Auskunft darüber gibt der Betriebsabrechnungsbogen BAB, doch diese Berechnung wird nur von wenigen Unternehmen regelmässig gemacht. Es beginnt schon mit dem Rohmaterialeinkauf. Hier bestimmt die Menge den Preis mit. So haben Abbundwerke andere Abnahmeverträge mit den Lieferanten als ein einzelner Holzbauunternehmer. Ausserdem braucht der eigene Abbund viel Platz. Rohmaterial muss gelagert werden, mit dem Stapler müssen die 13-Meter-Pakete verschoben werden können, die Wendekreise sind gross. Das erfordert entsprechende Zufahrten und Tore. Allein für den Bau einer entsprechenden Halle ist meist eine Investition im siebenstelligen Bereich nötig. Da stellt sich die Frage, ob an Stelle des Abbunds etwas anderes produziert werden und damit weit mehr Wertschöpfung generiert werden könnte. Ein erhöhter Vorfertigungsgrad, beispielsweise indem Fenster, Installationsebenen oder Elektroinstallationen schon in der Werkhalle montiert werden, steigert ebenfalls die Wertschöpfung im eigenen Unternehmen und das oft mit grösserer Chance auf mehr Ertrag. Die Investitionen in die Abbundmaschine, der Unterhalt und die Infrastruktur mit Raumkosten, Hallenkran, Absaugung, Hacker und Entsorgung sind nicht zu unterschätzen. Zudem sind auch regelmässig Anpassungen bei der Software mit Schnittstellen zu den CAD-Systemen nötig. Zu oft werden die vielen Stunden für solche Software-Umstellungen nicht explizit aufgeschrieben und verschwinden in den unproduktiven Stunden oder in einem Auftrag.
«Die Mitarbeiter haben eine Maschine im Wert eines Ferraris vor sich, doch Einarbeitung und Schulung reichen gerade für die Traktorenprüfung.»
Mitarbeiterkosten berücksichtigen
Die Mitarbeiterkosten sind der nächste grosse Aufwandposten. Die Abläufe und Prozesse rund um den Abbund sind anspruchsvoller, als man denkt, und die laufende Weiterentwicklung der Software fliesst selten in die tägliche Arbeit ein. Die Datenaufbereitung für den Abbund ist aufwändig – ob in der Arbeitsvorbereitung oder später an der Maschine. Dafür muss ein zusätzlicher Mitarbeiter pro Jahr eingerechnet werden. Diese Aufgabe übernimmt das regionale Abbundzentrum gerne. Auch die Logistik, das Bereitstellen des Materials und der interne Transport verursachen viele Arbeitsstunden im Betrieb. Jedoch haben fast alle Holzbauunternehmen lediglich einen Mitarbeiter an der Abbundanlage eingeteilt. Ein Blick in die Maschinenleistungskennzahlen zeigt, dass die Abbundmaschine meist nur einen Wirkungsgrad (effektive Produktionszeit) von 60 bis 70 Prozent aufweist. Die Stillstandzeiten der Anlage entstehen, weil das Material nicht rechtzeitig bereitliegt oder nicht rasch genug weggebracht werden kann. Die Aus- und Weiterbildung der Mitarbeiter wird oft vernachlässigt, nicht selten fehlt eine Stellvertretung des Maschinisten. Die Mitarbeiter haben eine Maschine im Wert eines Ferraris vor sich, doch Einarbeitung und Schulung reichen gerade für die Traktorenprüfung.
Wirtschaftlichkeit berechnen
Um die Wirtschaftlichkeit einer Abbundanlage zu berechnen, müssen alle Faktoren wie Kosten, Infrastruktur, Produktionsfläche, technische Abschreibung, Fertigungszeiten und die Ausbildung der Mitarbeitenden eingerechnet und auf die jährlich abgebundenen Kubikmeter umgelegt werden. Beim Entscheid für den eigenen Abbund kann auch die geografische Lage des Unternehmens eine Rolle spielen; dann wenn die Transportwege zum Abbundwerk zu lange und somit nicht wirtschaftlich sind. Es lohnt sich ausserdem, Kooperationen in Betracht zu ziehen. Fazit: Es gibt keine ausschliesslich richtige oder falsche Lösung, denn jedes Unternehmen und jede Situation ist anders.
Text und Fotos: SCHULER (Stephan Zürcher)