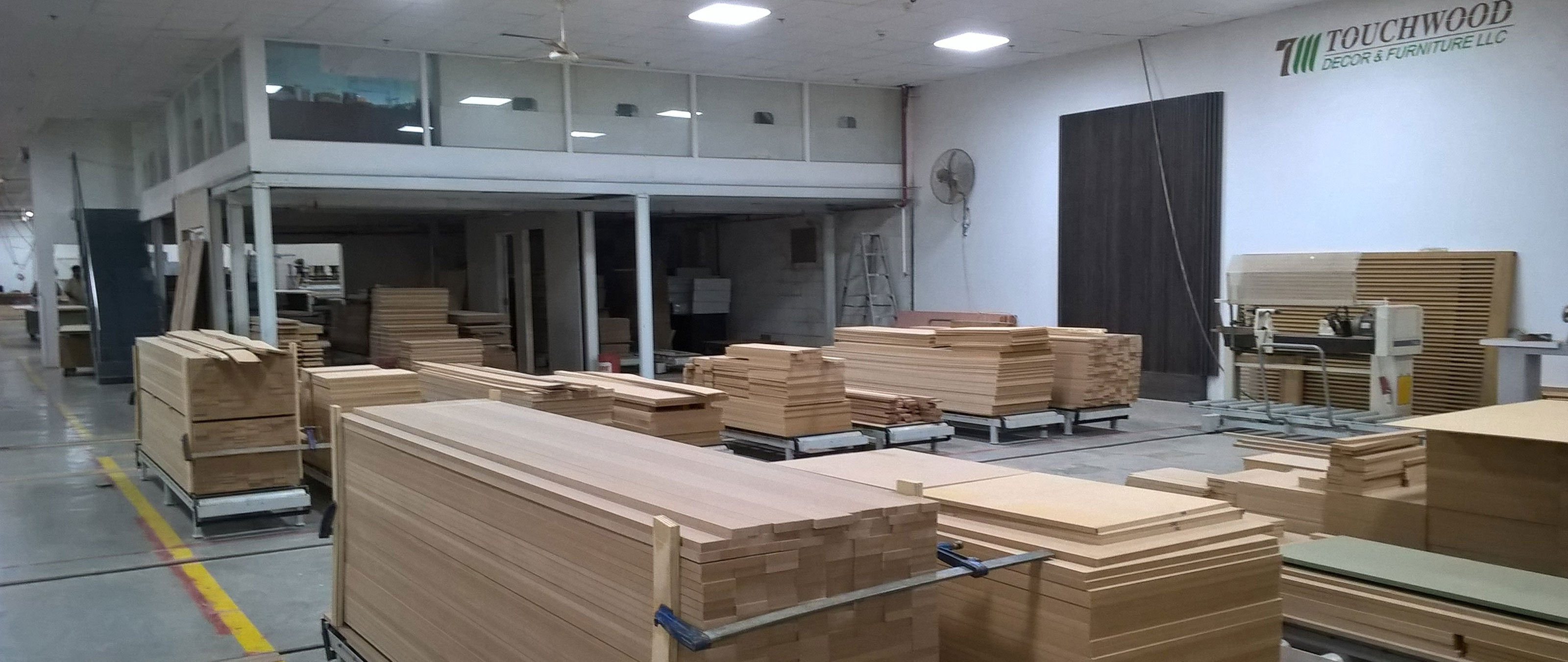
Sie soll eine Veranstaltung der Superlative werden: die Expo 2020 in Dubai. Die Organisatoren der Weltausstellung rechnen mit rund 25 Mio. Besuchern. Auch die Möbelindustrie will von dem erwarteten Auftragsboom profitieren. Dafür sind effiziente Fertigungsprozesse notwendig, wie man bei Touchwood frühzeitig erkannt hat. Der Hersteller von Möbeln und Innenausbauten aus den Vereinigten Arabischen Emiraten hat gemeinsam mit Schuler Consulting seine Produktionsabläufe optimiert. Im achten Teil der HK-Serie „Internationale Möbelproduktion“ schildert Martin Kintscher seine Eindrücke von der Zusammenarbeit.
Dubai, das wohl bekannteste der insgesamt sieben Vereinigten Arabischen Emirate, steht für viele Menschen auf ihrer persönlichen Tourismus-Landkarte weit oben. 2015 kamen 14,3 Mio. Besucher in die Hauptstadt Dubai-City, im internationalen Wettbewerb rückt die Metropole damit immerhin auf Platz vier der meistbesuchten Städte der Welt vor.
Die Temperaturen in Dubai liegen zwischen angenehmen 15 bis 26 Grad im Winter und anstrengenden 40 Grad im Sommer. Es ist ein Land der Extreme: Scheichs in Luxus-Sportwagen, Touristen am Meer, Kamelreiter am Strand, Skifahrer in der Wüste, gepflegte Grünanlagen, choreographierte Brunnen und Wasserspiele sowie das höchste Gebäude der Welt, der Burj Khalifa. Die gesamte Stadt profitiert vom Reichtum des Emirats, fast alle Schönheit ist künstlich geschaffen. Die Straßen sind sauber, die Grünanlagen bestens gewässert, das Grün besser gepflegt als mancher Golfplatz – alles glitzert und blendet.
Wirtschaftlich geht es dem Land wieder deutlich besser als noch vor einiger Zeit. Die kommende Weltausstellung im Jahr 2020 ist bereits überall präsent, an vielen Stellen wird gebaut. Doch zahlreiche dieser Gebäude stehen leer – es gibt ein Überangebot und die Mieten sind teuer.
Das Wirtschaftswachstum erreichte 2015 ungefähr vier Prozent. Es wird befürchtet, dass sich die Wirtschaft in der Region nach 2020 rasch abkühlen könnte. Die Emirate zählen zu einem der größten Absatzmärkte für die deutsche Industrie in der arabischen Welt und stehen in der Rangliste deutscher Exportziele im Moment auf Platz 20.
Seit der Entdeckung der Ölvorkommen Ende der Sechzigerjahre hat sich Dubai zu einem der Vorreiter der arabischen Länder entwickelt. Da die Ölvorkommen im Vergleich zu denen der Nachbarn aber relativ klein sind, setzte die Stadt schon früh auf andere Einnahmequellen, nämlich auf Tourismus und Industrie – und dies macht sich jetzt, wo nicht mehr allein auf Reichtum durch die fossilen Brennstoffe gesetzt werden kann, bezahlt. Auch die Möbelindustrie hat sich in den vergangenen Jahren gut entwickelt.
Viele Fabriken der Branche lassen sich folgendermaßen beschreiben: Gefertigt wird meist alles unter einem Dach, etwa furnierte oder lackierte Möbel und Zimmertüren. Damit kann ein Großprojekt von einem Produzenten komplett abgewickelt werden. Typische Projekte der Kunden sind zum Beispiel der Ausbau von hunderten nahezu identischen Hotelzimmern oder Unterkünften mit einer entsprechenden Logistikkette bis zur Installation. Gefertigt werden dann in Serien etwa Massivholz-Türrahmen aus Meranti-Massivholz mit der typischen Fingerzinkenverbindung der Region, furnierte Türblätter in Sandwichbauweise und Möbel aus Spanplatten und MDF. Andere Unternehmen bauen Empfangshallen oder Restaurants mit Hochglanzoberflächen, ergänzt mit viel Glas, Gold oder Edelstahl.
In den Fabriken herrscht meist ein Klassensystem: Der Besitzer ist (und muss laut Gesetz sein) ein Emirati, die sogenannten „White Collar Worker“ (also Mitarbeiter mit weißem Hemdkragen oder Ingenieure) sind meist qualifizierte Europäer oder Inder und die sogenannten „Blue Collar Worker“, also Fabrikmitarbeiter, kommen oft aus Südostasien, Pakistan oder Indien. Die Fertigung ist handwerklich geprägt, viele Mitarbeiter zaubern mit einfachen Maschinen, Geschick und Fachwissen die unglaublichsten Produkte. Die Qualität entspricht am Schluss fast europäischen Schreinervorstellungen. Doch bis das Möbelstück wirklich fertig ist, wird einiges „gebastelt“, geändert und neu gemacht.
Anfang 2016 startete Schuler Consulting in Dubai ein Projekt bei Touchwood. Das Unternehmen ist ein lokaler Hersteller von qualitativ hochwertigen, exklusiven Möbeln und Innenausbauten in Scharjah, einem 30 Kilometer entfernten Nachbar-Emirat von Dubai. Seine Projekte sind mehrheitlich Großaufträge, also schlüsselfertige Entwicklungsprojekte von ganzen Hochhäusern, sowie Innenausbauten von Wohnungen, Bürolandschaften, Villen und Krankenhäusern.
In der Produktion von Touchwood arbeiten rund 200 Mitarbeiter aus verschiedenen Nationen unter einem Dach. Der deutsche Ingenieur und leitende Manager Jens Otterstedt hat 2015 begonnen, die Produktion effizienter zu gestalten. Der Materialfluss war unübersichtlich, die Arbeitsplätze waren ungünstig angelegt, zu viele Mitarbeiter standen in der Produktion herum. Die vorhandenen Maschinen wurden nicht oder nur unzulänglich genutzt. So schliffen 20 Personen von Hand statt mit der Breitbandschleifmaschine, die keiner richtig bedienen konnte.
Für Otterstedt war rasch klar, dass hier die Leistung extrem erhöht werden könnte und 30 Prozent mehr Output mit deutlich weniger Mitarbeitern machbar sein müsste. „Die Verschwendungen in Prozessen und Abläufen sind einfach zu groß, da müssen wir rasch und mit deutlichen Schritten Verbesserungen erzielen. Wir haben seit Anfang des Projektes gewusst, dass wir diese ehrgeizigen Ziele nur mit professioneller Hilfe erreichen können. Schuler Consulting ist der perfekte Partner für unser Geschäft. Wir haben große Herausforderungen in Angriff zu nehmen und bauen dabei auf einen kompetenten Partner mit Kenntnissen in der Möbelfertigung, Planung, Software und Optimierung“, formulierte er seine Vorstellungen. Darauf aufbauend konnte Schuler ein Projektteam aus Spezialisten zusammenstellen, die durch eine Ist-Analyse in wenigen Tagen die Prozesse bei Touchwood genau benannten und das Optimierungspotenzial aufzeigten.
In einem Strategie-Workshop mit dem Management und den Investoren von Touchwood wurden die Potenziale und Ziele der nächsten Jahre gemeinsam definiert. Als Basis dienten Kennzahlen, welche laufend die Verbesserungen vom Ist- zum Zielzustand dokumentieren. Für das Management fasste man alle Maßnahmen in einer Planung von Investitionen und Optimierungen zusammen und berücksichtigte entsprechend die Einsparung und die Leistungssteigerung je Schritt. So entstand für Touchwood ein priorisierter Entwicklungsplan für die nächsten Jahre, der nun in der Finanzplanung wie auch in der Planung der Fertigung seinen Niederschlag findet.
Ein Spezialist für die Optimierung von Fertigungsprozessen setzte bei Touchwood sogleich erste Maßnahmen um. In Schritten – manchmal in fast zu großen – mit schneller Taktfolge wurde die Effizienz in der Fertigung gesteigert. Damit setzte das motivierte Management bei den Mitarbeitern deutliche Zeichen der Veränderung. An Orten wie Dubai müssen die Veränderungen in Unternehmen klar, direkt und mit Nachdruck gestartet werden. Ansonsten kann die aufgrund klimatischer Bedingungen existierende Trägheit der Menschen (wie würde man selbst bei 40 Grad in der Produktion im Sommer arbeiten?) nicht überwunden werden.
Auch Jens Otterstedt musste große Sprünge machen, um die Investitionen in die bestehende Fertigung, wie zum Beispiel die Anschaffung von zusätzlichen Maschinen und Logistikhilfsmitteln oder die Re-Allokation von bestehenden Produktionsmitteln, im Einklang mit den Investoren starten zu können. So entstand in zehn Monaten eine komplett veränderte Produktion. Die Leistungskennzahlen zeigen deutlich, was sich alles getan hat.
In einem weiteren Workshop hat dann der Schuler-Spezialist Christof Ehrenbrink gemeinsam mit den Ingenieuren von Touchwood das enorme Potenzial identifiziert, das in der designtechnischen und auch fertigungstechnischen Optimierung der Produkte liegt. Anschließend hat man die bestehenden Produkte standardisiert und einen Leitfaden für die Konstruktion der künftig zu fertigenden Möbel und Innenausbauten erarbeitet.
Im Gesamtkonzept war natürlich auch Industrie 4.0 ein Thema. Die Spezialisten von Schuler erarbeiteten dazu zusammen mit dem Management ein Informationskonzept, in dem die digitale Beschreibung aller Möbelteile sowie auch die Vernetzung der kompletten Fertigung mit zusätzlichen Modulen und Schnittstellen definiert wurde. Die Homag-Software „Wood CAD/CAM“ dient bei Touchwood jetzt der Auftragskalkulation und Auftragserfassung sowie der Konstruktion der vielschichtigen Aufträge. Hier werden auch die Maschinendaten für die CNC-Bearbeitung und den Zuschnitt generiert.
Die automatische Stücklistenauflösung wird dann im ERP-System mit Preisen hinterlegt und ist gleichzeitig die Basis für die Angebotskalkulation. In der Produktion melden Fertigungs-Clients mit Barcode-Lesegeräten die Ist-Zeiten der Aufträge und aktualisieren den Auftragsstatus. Jens Otterstedt ist begeistert und freut sich über die Ergebnisse der harten Arbeit im Team. „Dank der soliden Erfahrungen in der Holz- und Möbelindustrie konnte uns Schuler Consulting zeigen, wie wir internationale Trends und Neuerungen für uns sinnvoll anwenden können. Das Ergebnis sind für uns effiziente Prozesse und eine wirtschaftliche Fertigung, die in der Region ihresgleichen suchen“, sagt er.
Aktuell ist Schuler Consulting noch für die weitere Schulung der Mitarbeiter vor Ort in Dubai. Gemeinsam hat man das Layout der Produktion umgesetzt und die neuen Prozesse eingeführt. Die Mitarbeiter erkennen die Vorteile der Optimierungen, die Leistungskennzahlen beweisen den Erfolg. Für die Vorarbeiter und den Produktionsleiter ist die Steuerung der Produktion und die Auftragsnachverfolgung deutlich einfacher geworden. Die Zahl der Fehler, der „Feuerwehrübungen“ und die Unruhe in den Prozessen haben deutlich abgenommen. Und der erbrachte Aufwand schlägt sich auch im wirtschaftlichen Gesamtergebnis nieder.
Durch diese Resultate ist den Investoren klar geworden, dass sich eine neue Produktion mit weniger baulichen Einschränkungen, mit neuen Maschinen und weiteren Schritten in Richtung Industrie 4.0 lohnen wird. Deshalb wurde die Planung für die neue Arealentwicklung abgeschlossen, die Maschinen für den ersten Schritt sind bereits bestellt und werden bald installiert.
Projekte wie diese, mit guter Kommunikation, klaren Schritten, direkter Umsetzung, breiter Thematik und sichtbaren Ergebnissen, machen allen Spaß – nicht nur den Kunden
Fotos: Schuler