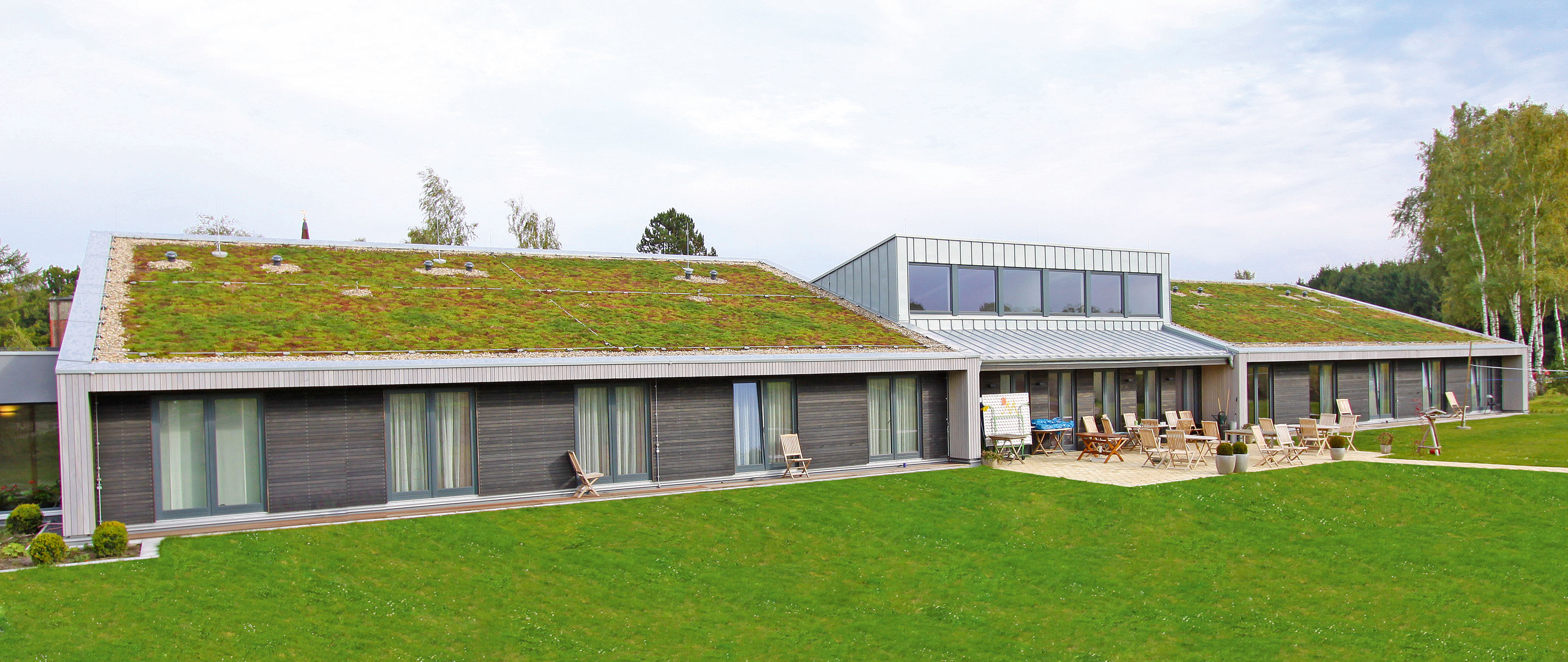
Die letzten beiden Wachstumsschritte brachten ihr eine umfassende Automatisierung der Produktion und ein Sprungbrett in die digitale Zukunft. Alle Zeichen im Holzbau stehen auf Wachstum: Nur so kann man am rasant steigenden Auftragsvolumen partizipieren, die Markposition halten oder gar verbessern und das Risiko steigender Materialpreise bei vollen Auftragsbüchern minimieren. Andererseits mehren sich warnende Stimmen, die angesichts der andauernden Coronakrise mögliche Auftragsrückgänge befürchten. Zwar werden letztere aus heutiger Sicht vermutlich in erster Linie den konventionellen Massivbau treffen, aber etwas Vorsicht kann dennoch nicht schaden. Als sinnvolles Konzept erscheint vor diesem Hintergrund ein modulares Wachstum, das sich stufenweise am vorhandenen Auftragsvolumen orientiert, mit überschaubaren Investitionsschritten eine Anpassung an die Marktlage erlaubt und dabei auch von einer Prise visionärem Unternehmertum inspiriert wird. Denn es ist sinnvoll, mit der Investition von heute schon das Fundament für Entwicklungen von morgen zu legen.
Verzehnfachte Stückzahl
Ein gutes Beispiel für ein solches sukzessives Wachstum ist die Zimmerei Hamdorf im schleswig-holsteinischen Fahrenkrug. Ihr Schwerpunkt liegt im Objekt- und Gewerbebau und in der Fertigung von Holzrahmenelementen für kleinere Zimmererkollegen. Daneben fertigt und montiert das Unternehmen mit seinen 46 Mitarbeitern Nagelplattenbinder, deckt Dächer und ist auch im Fassadenbau aktiv. Heute ist es gute zehn Jahre her, dass Geschäftsführer Daniel Hamdorf mit der Fertigungskapazität für Holzrahmenelemente erstmals an seine Grenzen stieß. Etwa sechs Holzhäuser produzierte er damals im Jahr, und obwohl man 2009 mitten in der Finanzkrise steckte und nicht unbedingt in einem traditionellen Holzbauland angesiedelt ist, wies die Nachfrage nach Holzbauprodukten kräftig nach oben. Um an diesem Aufschwung teilhaben zu können, baute Hamdorf eine neue Fertigungshalle und investierte in eine Dreitischanlage von WEINMANN. Ein bereits bestehender WEINMANN-Arbeitstisch wurde als Tisch für die Riegelwerkproduktion in die neue Fertigungslinie einbezogen, etwas später noch ein fünfter Tisch ergänzt. Er diente als Puffertisch und für Sonderbearbeitungen wie Fassaden. Die neue Fertigungslinie brachte der Zimmerei unter dem Strich eine Verzehnfachung ihrer Holzbaukapazität auf 60 Häuser im Jahr bzw. ein entsprechendes Äquivalent in m2 Elemente. Damit kam man in Fahrenkrug bis etwa 2019 über die Runden. Dann war, obwohl man durch Einführung eines Zweischichtbetriebs die Stückzahl auf etwa 100 Häuser im Jahr gesteigert hatte, erneut die die Grenze des Wachstums erreicht. „Ich glaube, wir haben uns durch eine große Zahl eigener und von unseren Holzbaukunden realisierter Projekte einen guten Ruf in der Region erarbeitet“, erläutert Daniel Hamdorf die Ursachen für seinen Erfolg. „Hinzu kommt, dass der Holzbau mit seinen hohen Qualitätsstandards und einer guten CO2-Bilanz auch im Norden immer mehr dem Zeitgeist entspricht. Deshalb ist er heute bei öffentlichen und gewerblichen Kunden eine fest etablierte Bauweise.“
Modulare Erweiterung
Angesichts der guten Geschäftsentwicklung fasste Daniel Hamdorf 2020 ein weiteres Upgrade für seine Holzrahmenfertigung ins Auge. Dabei dachte er nach Rücksprache mit den Mitarbeitern aus Arbeitsvorbereitung und Produktion zunächst an eine Automatisierung des Dämmprozesses: „Das war der erste Schritt. Darüber hinaus bestand der Wunsch, die Produktionsabläufe weiter zu optimieren. So wollten wir den permanenten Zweischichtbetrieb, den wir seit drei bis vier Jahren fuhren, wieder auf eine Schicht reduzieren – bei gleichem oder vielleicht sogar erhöhtem Ausstoß.“ Mit diesem Konzept ging Daniel Hamdorf in die Beratung mit WEINMANN und entwickelte im Dialog mit Projektleiter Jörg Groß eine maßgeschneiderte Fertigungslinie. Sie besteht aus fünf Arbeitstischen, die – anders als in der früheren Variante – alle von Multifunktionsbrücken überfahren werden. Zwei dieser Brücken sind neu: Eine WEINMANN WALLTEQ M-310 insuFill spart laut Hamdorf durch das vollautomatische Einblasen von Dämmstoffen gut 80 Prozent an Arbeitszeit in diesem Bereich, eine WALLTEQ M-120 übernimmt die Bearbeitung der Beplankungen an den vorderen beiden Arbeitstischen. Auf den beiden hinteren versieht die Multifunktionsbrücke der früheren Dreitischanlage ihren Dienst, die zu diesem Zweck eine neue Software erhielt. Auch die bestehenden Arbeitstische konnten großenteils modernisiert werden. Sie wurden zum Beispiel mit Längstransporten ausgestattet, die auf lange Sicht eine zentrale Steuerung des Workflow ermöglichen (s.u.). Die beiden ältesten Arbeitstische wurden durch Neuanschaffungen ersetzt und leisten heute noch gute Dienste in einer separaten Deckenelement-Fertigung. Besonders beeindruckt war Daniel Hamdorf davon, „wie nahtlos man die bestehenden Fertigungseinheiten in die neue Linie einbeziehen konnte. Ich hätte nicht damit gerechnet, dass die aktuelle Software auf unserer in die Jahre gekommenen Brücke noch laufen würde. Hier und bei den Tischen zeigte sich ganz klar, dass die modularen Erweiterungsmöglichkeiten der WEINMANN-Maschinen kein bloßes Werbeversprechen sind.“ Auch an der Peripherie der Anlage wurde gefeilt, um den Materialfluss rund um die Fertigung zu optimieren. Inzwischen wird jeder Tisch außer der Dämmstation von einem Plattenheber bedient, so dass an vier Stationen auf kurzem Weg Material aufgelegt und von einer Multifunktionsbrücke bearbeitet werden kann. Dies kann gleichzeitig bei der Innen- und Außenbeplankung und im Wechsel an den beiden zugeordneten Tischen geschehen – ohne lange Standzeiten der Brücke. Diese Parallelität mehrerer Arbeitsgänge erklärt in Verbindung mit den stark reduzierten Bear-beitungszeiten an der Dämmstation den deutlich höheren Output der neuen Linie.
In die Zukunft gedacht
Mit der Investition in einen Granit MES Produktionsleit-stand hat Daniel Hamdorf noch ein weiteres Potential zur Erhöhung seiner Stückzahlen genutzt. „Granit war für mich zunächst einmal gleichbedeutend mit Multiwand“, erläutert der Zimmermeister diesen Investitionsschritt. „Dafür mag es auch andere Lösungen geben, aber auf den zweiten Blick sind diese immer mit Problemen behaftet.“ Die Vorteile von Multiwänden liegen vor allem in der Verkürzung der Arbeitstakte: „Wenn ich drei oder vier kürzere Innenwände zu einer Multiwand zusammenfasse, muss ich sie nicht mehr einzeln takten, sondern sie laufen in einem Arbeitstakt durch die Fertigungslinie“, erläutert WEINMANN-Projektleiter Jörg Groß. „Auch im Abbund habe ich eine Zeitersparnis, weil es bei der Multiwand einen durchgehenden Ober- und Untergurt gibt. Wenn so ein System gut eingespielt ist, holt es je nach durchschnittlicher Wandlänge bis zu 20 oder 25 Prozent mehr an Leistung aus einer Fertigungslinie heraus. Besonders deutlich ist dieser Effekt bei Großprojekten mit sich wiederholenden Bauteilen. Das macht Granit auch für solche Unternehmen interessant, für die der Gewinn aus anderen Modulen der Software eher überschaubar ist.“ Natürlich gibt es da auch noch den visionären Aspekt. Er besteht darin, dass Zimmereien bereits heute in die Software einsteigen, um sich mit dem System vertraut zu machen. Wenn die Stückzahlen dann weiter zunehmen, ist ihnen der Umgang damit bereits vertraut und muss nicht unter Stress gelernt werden. Ein Gedankengang, der auch Daniel Hamdorf durchaus vertraut ist: „Unser Unternehmen ist im Lauf der Jahrzehnte stetig gewachsen, weil es unsere Devise ist, einen Gutteil des Gewinns zu reinvestieren. Schon mein Großvater hat quasi bei Null angefangen und eine gut ausgestattete Zimmerei übergeben, und ich habe bei meinen Investitionen auch immer die Zukunft meiner Kinder im Blick. Und die könnte aus heutiger Sicht durchaus so aussehen, dass die Zimmerei Hamdorf noch deutlich größer wird. Vom Grundstück her haben wir noch jede Menge Platz für neue Hallen, und dann könnte ein zentraler Produktionsleitstand eine interessante Sache sein.“ Darüber hinaus ist Granit schon heute Teil eines umfassenden Digitalisierungsprozesses, mit dem man sich in Fahrenkrug auf künftige Herausforderungen vorbereitet. Dazu gehört, dass man die Vielzahl von Softwarelösungen im Unternehmen vereinheitlicht oder durch Schnittstellen so miteinander vernetzt, „dass am Ende ein homogener digitaler Prozess im Unternehmen entsteht, den jedes Projekt durchläuft und auf den jeder Mitarbeiter zugreifen kann. Granit wird in diesem Prozess die Schnittstelle zur Fertigung sein.“
Handwerk 4.0
Also Industrie 4.0? Im Prinzip schon, aber bei aller Automatisierung und Digitalisierung will die Zimmerei Hamdorf ein Handwerksbetrieb bleiben. Heißt in erster Linie: Man bietet Kunden keine Standardlösungen an, sondern liefert jedem, was er gerne möchte. In der Fertigung betrifft das zum Beispiel den variablen Wandaufbau und die verwendeten Materialien – hier ist man mit der neuen Linie absolut flexibel aufgestellt. „Das ist natürlich auch im Bereich der Lohnfertigung wichtig“, erläutert Daniel Hamdorf. „Ein Zimmerer gibt ja einen Gutteil seiner Wertschöpfung an uns ab und setzt eine Menge Vertrauen in uns, wenn er seine Elemente bei uns in Auftrag gibt. Da kann ich ihm die Wände auch so verladen, wie es für ihn optimal ist und ihm auch sonst den entscheidenden Tick mehr an Service bieten, der uns vom Wettbewerb unterscheidet. Unser Ziel muss es hier und in den anderen Bereichen sein, dass ein Kunde vielleicht ein bisschen mehr bezahlt, weil ihm unser Plus an Individualität und Sicherheit das wert ist.“ Zum Thema Sicherheit gehört auch, dass Digitalisierung und Produktionssteuerung auch zu einer erhöhten Planbarkeit der Fertigung führen werden – mit allen positiven Nebeneffekten wie einer noch höheren Kalkulationssicherheit und einer punktgenauen Lieferung der Bauteile, wo man heute noch eine Streuung von ±5-6 Tagen hat. Bis es so weit ist, hat man in Fahrenkrug noch einige Knoten zu lösen, aber der erste Schritt ist getan: „Wir konnten die Fertigung nach einer nahtlosen Übergangsphase schnell in den Einschichtbetrieb zurückfahren“, erläutert Daniel Hamdorf. „Seither fertigen wir mit vier Mitarbeitern die gleiche Elementstückzahl, die wir früher in zwei Schichten mit zwei mal drei Mitarbeitern erreicht haben. Fürs Erste haben wir von der Anlage also eine Kostenreduktion, durch den Einsatz von Granit wird sich demnächst auch unsere Stückzahl noch etwas erhöhen. Auf lange Sicht bringt uns die Fertigungslinie die Option, bei weiterhin steigender Nachfrage unsere bisherige Stückzahl im Zweischichtbetrieb zu verdoppeln. Unsere Zielgröße liegt dann bei 200 Häusern im Jahr.“
Autor: Dr. Joachim Mohr
Ein Artikel aus dem Fachmagazin mikado Ausgabe Juli/August 2021 Mehr Informationen finden Sie hier.
„Ich war beeindruckt, wie nahtlos man die bestehenden Fertigungseinheiten in die neue Linie einbeziehen konnte.“Daniel Hamdorf, Geschäftsführer Zimmerei Hamdorf
Zimmerei Hamdorf
Die Zimmerei Hamdorf liegt im schleswig-holsteinischen Fahrenkrug und hat ihren Schwerpunkt im Objekt- und Gewerbebau und in der Fertigung von Holzrahmenelementen für kleinere Zimmererkollegen. Daneben fertigt und montiert das Unternehmen mit seinen 46 Mitarbeitern Nagelplattenbinder, deckt Dächer und ist auch im Fassadenbau aktiv.
Website