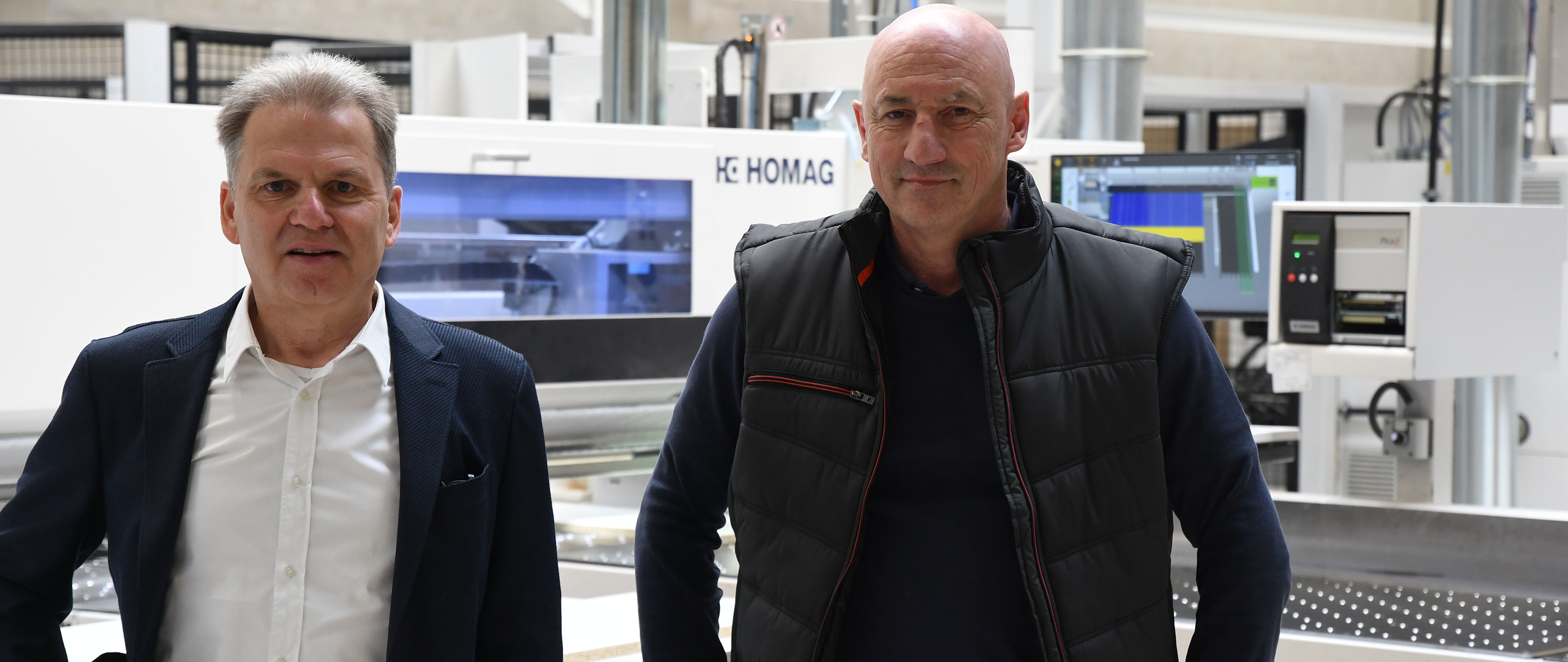
Der Zug muss rollen
In der Produktion wird diese Individualität mit ehernen Prinzipien umgesetzt: Qualität und Flexibilität natürlich, vor allem aber auch die Ausfallsicherheit in der Fertigung. Von Anfang bis Ende der Produktion übernehmen dafür Systeme von HOMAG die Gewähr.
Massivholz in der Küche? Kombiniert mit Glas? Steinarbeitsplatte oder Keramik? Breitschopf macht solche Vorstellungen tagtäglich zur Realität – und fertigt so die exklusive Wunschküche. Der Kunde kann dafür sein Unikat zusammen mit 50 Planern in ganz Österreich entwerfen. Gefertigt wird die Küche dann aus hochwertigen, oft heimischen Materialien. Weil Breitschopf von der Qualität seiner Küchen überzeugt ist, gewährt der Hersteller auch zehn Jahre Garantie. Und weil eine Küche aus Steyr-Dietach ohne Umwege direkt vom Produzenten stammt, können diese Qualität und Individualität zum attraktiven Preis-Leistungs-Verhältnis angeboten werden. „Und zwar in sechs Vertriebsstützpunkten, mit denen wir einen Großteil Österreichs abdecken und unsere Küchen im unmittelbaren Kontakt zum Kunden verkaufen“, unterstreicht Geschäftsführer Johann Breitschopf. 20 Montageteams übernehmen schließlich den Aufbau bei ihrem neuen Besitzer.
2000 Unikate pro anno
Wie aber wird diese Individualität von der Planung über die Produktion und Montage bis hin zum Service in ganzer Breite umgesetzt? Immerhin fertigt Breitschopf 2000 Küchen pro Jahr. Im ganzen Oberflächenspektrum von Holz, Furnier, Melamin bis hin zu Lack. Aber auch in drei Linien als klassische, Design- und Landhausküchen. Außerdem greift Breitschopf jährlich neue Trends auf: „Matte Oberflächen zum Beispiel, die derzeit vor allem bei Lack angesagt sind. Oder die helle Küche in Kombination mit Holz. Stark im Kommen sind auch Anthrazit- und Betonfarbtöne.“ Der Phantasie und dem Geschmack sind keine Grenzen gesetzt, betont der Geschäftsführer weiter: „Über 90 Prozent unserer Küchen enthalten dafür auch Steinarbeitsplatten oder Keramik. Das macht sonst keiner.“ Die Abnehmer der Einzelstücke sind ausschließlich Privatpersonen: Häuslebauer, oft auch Menschen, die ihre erste, eher einfache Küche nun hochwertig ersetzen wollen. „Unser typischer Kunde möchte etwas Gescheites und zugleich Langlebiges.“ Was also sind die Fertigungsmittel, mit denen Breitschopf dieses Spektrum realisiert? Und welche Prinzipien liegen zugrunde? Zum ersten eine hohe Fertigungstiefe, mit der die 150 Mitarbeiter von der Planung bis zur Montage nahezu alles selbst machen. Synonym für den Fertigungsansatz und seine Prinzipien ist vor allem jedoch ein Zug, der durch die gesamte Fertigung läuft, jede Küche mitnimmt und diese nach neun Tagen fertig ans Ziel bringt.
Von Schienen und Wasserstraßen
Dieser Zug, der durch die Fertigung in Steyr-Dietach rennt, setzt die Einzelfertigung im Fließprinzip um. Bei einer Durchlaufzeit von exakt neun Tagen wird eine Küche damit auftragsbezogen und kommissionsweise produziert: drei Tage in der AV plus sechs Tage in der Fertigung. „Die Prozesse sind straff getaktet, weshalb der Maschinenpark entsprechend ausgerichtet sein muss“, betont Produktionsleiter Manfred Hoffmann. „Was bedeutet: Wir brauchen nicht nur eine hohe Flexibilität, sondern vor allem auch Ausfallsicherheit. Das Material muss stetig fließen, darf nie liegenbleiben, denn der Liefertermin ist fix.“ Die Waggons des Zuges – um im Bild zu bleiben – sind dann Kommissionswagen, seine Gleise eine durchgängige Rollenbahn. „Ist das Material erst einmal zugeschnitten, kommt es auf die Wagen und läuft auf der Rollenbahn durch die gesamte Produktion. Immer gleich schnell, niemals zurück“, so Hoffmann.
Die sechs Fertigungsabschnitte, bei denen der Zug durchkommt, hat Breitschopf nach den Flüssen Inn, Donau, Drau, Enns, Steyr und Moldau benannt. Und so startet der Zug bei Gruppe Inn, wo mit einem Plattenlager „STORETEQ S-200“ sowie drei Sägen von HOMAG aufgeteilt wird. Ausfallsicherheit ist auch hier das bestimmende Thema. Darum drei Sägen – unter anderem eine „SAWTEQ B-400 profiLine“. „Wir hätten die 1500 Teile, die hier Tag für Tag durchlaufen, auch vollautomatisiert mit nur einer Säge schneiden können. Aber uns ist wichtig, dass der Zug rollt – auch wenn eine Maschine ausfallen sollte. Unsere kurze Durchlaufzeit und das kommissionsweise, auftragsbezogene Arbeiten lassen nichts anderes zu.“
Nun auch noch Luft
Gleiches gilt auch für die Gruppe Donau, wo vier Kantenmaschinen arbeiten, davon zwei von HOMAG. Während die ältere ausschließlich Dünnkanten bearbeitet, werden die Kanten auf einer neuen „EDGETEQ S-500 profiLine“, die alle Verfahren beherrscht, mit Laser- und Heißlufttechnologie gefahren. So werden etwa per „airTec“-Verfahren Nullfugen in hoher Qualität erzeugt. Ein Rotationslufterhitzer erwärmt dafür die Luft und dient zugleich als Wärmespeicher für die spätere erneute Erhitzung. Damit wird eine geringere Luftmenge benötigt und das Umfeld weniger erwärmt. Zur EDGETEQ S-500, die Breitschopf speziell an die Belange in Steyr-Dietach anpassen ließ, hebt Hoffmann noch hervor, dass man neben airTec vor allem einen Winkelanschlag wollte. Heute wird folglich mit einem Fügeaggregat gearbeitet, bei dem der Winkelanschlag für das exakte Fräsen im rechten Winkel sorgt. „Wir haben jahrelang gesucht, bis wir die Maschine gefunden haben, die genau zu uns passt. Die EDGETEQ S-500 ist die Maschine, die unsere Ansprüche komplett erfüllt.“
Immer weiter, immer vorwärts
Nach der Kante laufen ausgewählte Teile dann auf ein Bearbeitungszentrum „BMG 311 Venture“ von HOMAG, wo sie ohne Puffer und Liegezeiten gefräst werden. Bei diesen Teilen handelt es sich um Karussellböden, Anbautisch- oder Abdeckplatten, die allesamt keine geraden Kanten haben. „Das ist aber nicht die Menge“, ordnet Hoffmann ein. Und so rollt – nachdem die Bearbeitung erfolgte und noch geschliffene und lackierte Teile auf den Zug geschleust wurden – das Gros weiter zum Bohren und zur Montage. Während hier mit zwei vertikalen HOMAG-BAZ „DRILLTEQ V-500“ die Fronten gebohrt werden, übernimmt eine „DRILLTEQ H-600“ die großflächigen Teile. Für Ausfallsicherheit hat an diesem Fluss schon einmal eine V-500 gesorgt, als eine separate Dübelmaschine längere Zeit nicht zur Verfügung stand. „Wir haben die V-500 mit einer Einheit zum Dübeleintreiben ausstatten lassen, so konnten wir den Ausfall kompensieren“, erzählt Hoffmann.
Das Stellwerk der Fertigung – oder anders: ihr Hirn – ist bei all dem die ERP- und PPS-Software „MCS“ von Schuler Consulting, mit der Breitschopf seit Jahren arbeitet. „MCS war auch ein wichtiger Grund, weshalb wir uns – mit Blick auf reibungslose Schnittstellen – für HOMAG entschieden haben. Von der ERP- und PPS-Software werden die Daten dann an „woodWOP“ übergeben, das die WOP-Programmierung und als CAM-System die Steuerung der Maschinen übernimmt. „So laufen zum Beispiel auch die Bohrprogramme der V-500 und H-600 direkt an die Maschinen. Und das problemlos“, schildert der Produktionsleiter.
Auf direktem Weg zum Kunden, …
Für die Bauteile, die gefräst, gesägt, gebohrt und gedübelt wurden, geht es schließlich – nach einer Weiche – auf zwei Schienen weiter: entweder in Richtung Montage, wo die Korpusse unter anderem mit Korpuspressen zusammengebaut werden, oder zu mehreren Handarbeitsplätzen für die Arbeiten, die sich maschinell nicht umsetzen lassen. „Auch hier rennt alles wie auf der Rollenbahn durch und wird nach der Reihe abgearbeitet“, so Hoffmann. Sind die Küchen fertiggestellt, wechseln sie auf die Straße – per eigenem Lkw direkt zum Kunden. „In den Süden Österreichs dagegen liefern Speditionen; unsere regionalen Montageteams übernehmen dann den Aufbau der Küche beim Kunden.“
… egal, was passiert
„Wir haben in jüngster Zeit viel investiert“, erklärt Geschäftsführer Breitschopf. „Mit diesem Potenzial wollen wir in den nächsten Jahren kontinuierlich den Umsatz steigern. Die Reserven dafür haben wir mit unseren Maschinen.“ Die Strecke dahin wie auch die Anforderungen werden sich freilich nicht ändern: „Der Durchlauf muss stimmen. Der Tagespulk muss immer geschafft werden, damit wir die sechs Tage Durchlaufzeit einhalten“, unterstreicht Hoffmann nochmals. Um dies zuverlässig gewährleisten zu können, hat der Küchenhersteller mit HOMAG auch einen Servicevertrag vereinbart. „Außerdem können wir auf Fernwartung zurückgreifen“, ergänzt der Produktionsleiter. „Letztlich übernimmt so eine Maschine, sollte ihr Pendant einmal ausfallen, sofort dessen Aufgaben. Damit läuft die Produktion immer weiter, egal, was passiert.“