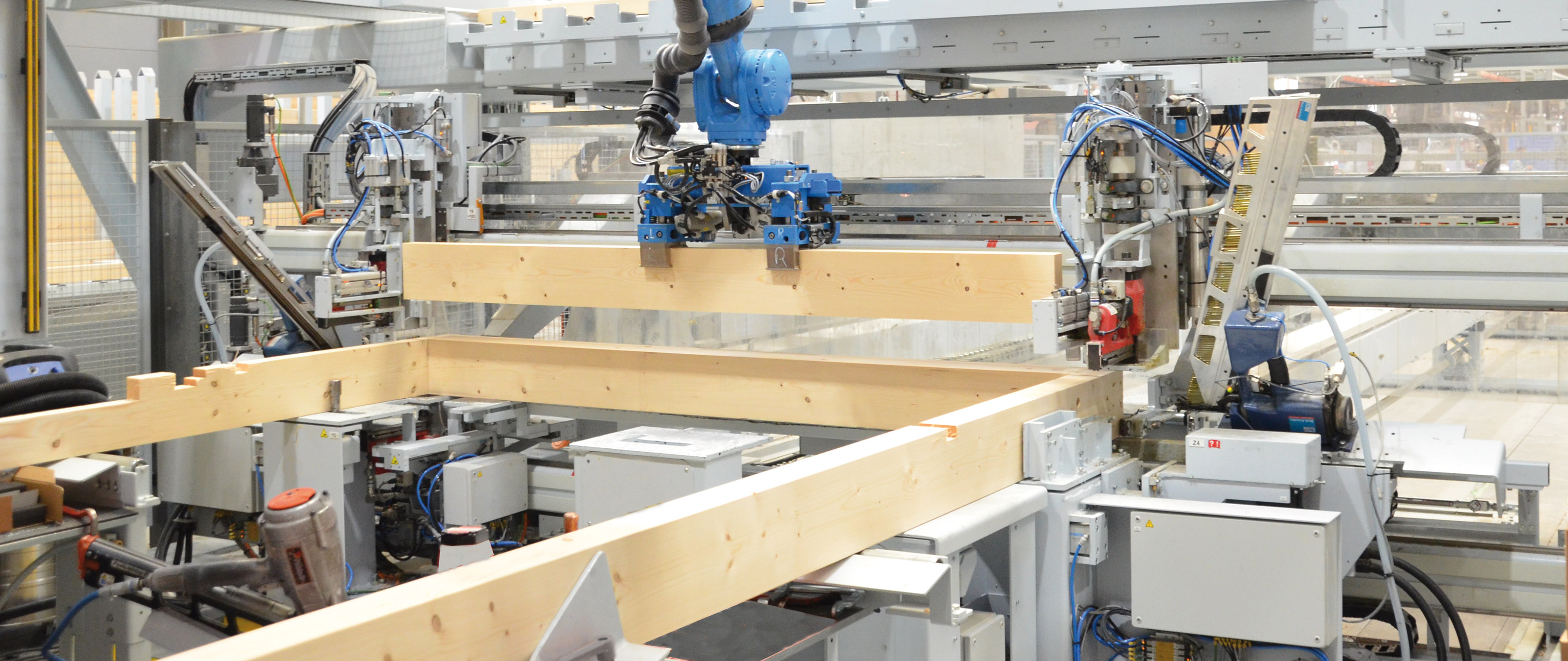
Fertigbau: Die Bien-Zenker GmbH im hessischen Schlüchtern ist eines der ersten Holzbauunternehmen, die in ihrer Fertigungslinie einen Industrieroboter einsetzen. Der in eine Riegelwerkstation integrierte Roboter erreicht nicht nur eine bisher nicht dagewesene Flexibilität und Schnelligkeit, er sorgt im Fertigbauunternehmen auch für attraktivere Arbeitsplätze.
In vielen Zimmereien geht die Modernisierung der Fertigungsmittel nach der Automatisierung des Abbunds in die zweite Runde. Während sie in eine vollautomatische Elementfertigung investieren, läutet der Fertigbau bereits Runde drei ein. Sie bringt den Holzbauunternehmen neben einer Automatisierung der Handling- und Logistiksysteme eine grundlegende Neuerung in die Fertigungshallen: den Industrieroboter. Da die Erfahrung lehrt, dass der Fertigbau die Entwicklungen im Zimmereibereich oft nur um einige Jahre vorwegnimmt, und da die eingesetzten Systeme in der Tat für kleinere Holzbauunternehmen interessant werden könnten, lohnt es sich, einen genaueren Blick auf diese Entwicklung zu werfen.
Das Ziel lautet: mehr Präzision und Kapazität
Einer der Vorreiter der neuen Technologie ist die Bien-Zenker GmbH im hessischen Schlüchtern. 1906 in Birstein als Zimmerei und Sägewerk gegründet und Ende der 90er-Jahre durch Übernahme von Zenker Hausbau in seiner heutigen Form entstanden, gehört dieses Unternehmen derzeit zu den Big Playern des deutschen Fertigbaus.
780 Häuser werden das Werk in Schlüchtern in diesem Jahr verlassen, im nächsten Jahr sollen es deutlich über 800 sein. Geplant, gefertigt und montiert werden diese Häuser derzeit von mehr als 500 Mitarbeitern; der Jahresumsatz des Unternehmens liegt bei rund 150 Mio. Euro. Da die Zeichen für Bien-Zenker bereits seit einigen Jahren auf Wachstum stehen, stieß man bereits im Jahr 2014/15 einen Prozess zur Erneuerung der Fertigungsanlagen an. Dabei ging es laut dem technischen Leiter René Honrath zum einen darum, sich auf steigende Stückzahlen kommender Jahre auszurichten, bei denen man mit der alten Fertigungslinie an die Kapazitätsgrenze gekommen wäre. Zum anderen "hatten wir dabei auch die Verbesserung der Präzision im Blick, die man durch eine automatisierte Fertigung erreichen kann". Damit ist bereits angedeutet, dass es in der Fertigungshalle in Schlüchtern vor der Modernisierung deutlich "händischer" zuging. So wurden an der früheren Riegelwerkstation nicht nur die Stiele teilweise von Hand eingelegt, auch Fräsungen und Bohrungen am Rahmenwerk wurden teilweise manuell ausgeführt. Hin und wieder musste ein Mitarbeiter auch Hölzer nachrichten, um die geforderte Präzision zu erreichen.
Vollautomatischer Materialtransport
Vor diesem Hintergrund erscheinen die heutigen Produktionsverhältnisse einen großen Schritt weiter: Stiele, Ober- und Untergurte werden von einem WEINMANN Beschickungsportal STORETEQ H-700 vollautomatisch in ein Rungenlager eingelagert und dann bedarfsgerecht der Abbundanlage zugeführt. Der Transport erfolgt dabei materialschonend mit Vakuum-Flächensaugern, sodass das Beschickungsportal auch Hölzer in Sichtqualität problemlos bewegen kann. Den Abbund übernimmt eine WEINMANN BEAMTEQ B-660, die mit einem 20-kW-Flex- 25-Sägeaggregat für Fünfachsbearbeitungen (z. B. für Winkel,- Kerven-, Schifter- und Längsschnitte) ausgestattet ist. Hinzu kommen ein 6,6-KW-Unterfluraggregat für Fingerfräser, Schwalbenschwanzfräser oder Bohrer und ein Vierachsaggregat mit 18,5 kW und Zwölffach-Werkzeugwechsler. So ausgestattet, bietet die Maschine eine hohe Abbundleistung, Präzision und Flexibilität. Dank Unterfluraggregat ist während der Bearbeitung kein Umkanten erforderlich. Bei Bien-Zenker häufig genutzt werden die Markierungs- und Beschriftungsaggregate, die den Mitarbeitern an späteren Arbeitsstationen eine eindeutige Zuordnung der Bauteile zu den jeweiligen Elementen ermöglichen. Dies gilt vor allem für Bauteile für die Giebel- und die Kniestocklinie, die manuell aus dem Abtransport der Abbundmaschine entnommen werden. Unter- und Obergurte werden nach dem Abbund vereinzelt und automatisch über Quertransporte zur Riegelwerkstation geführt, wo sie vollautomatisch positioniert werden. Abgebundene Sonderstiele kommen über einen horizontalen Kettentransport in den sogenannten Stieleturm. Dabei handelt es sich um ein chaotisches Lagersystem, in das jeder Stiel kontrolliert eingelagert wird, so dass er zum Einbauzeitpunkt sofort abgerufen und automatisch an einem Abholplatz an der Riegelwerkstation bereitgestellt werden kann. Standardstiele liegen stapelweise in einem zweiten Lager und werden von dort automatisch in eine "Mini-Abbundmaschine" eingefördert, die lediglich Bohrungen und Markierungen ausführt. Von dort gelangen sie nicht in den Stieleturm, sondern über ein zweites STORETEQ H-700-Handlingsystem zu einem zweiten Abholplatz an der Riegelwerkstation.
Das Interesse an Robotern im Holzbau nimmt stetig zu
Entnommen werden die Stiele an beiden Abholstationen von einem Sechsachsindustrieroboter, der sie automatisch ins Riegelwerk einlegt. Der Kuka-Roboter wurde von HOMAG geliefert und gemeinsam mit WEINMANN in die Fertigungszelle integriert. Dort erreicht er eine Geschwindigkeit und Präzision, die über derjenigen der vergleichbaren Technologien zur Riegelwerkerstellung liegt. Außerdem bietet er eine hohe Maschinenverfügbarkeit und Produktionssicherheit. Die Erwartungen, die man bei Bien-Zenker in die neue Anlage gesetzt hat, wurden in dieser Beziehung erfüllt. Produktionsleiter Herbert Vestert: "Wir stellen heute sowohl eine deutliche Leistungssteigerung als auch eine klare Verbesserung in der Maßhaltigkeit der Bauteile fest." WEINMANN greift mit dem Einsatz eines Industrieroboters in der Holzrahmenfertigung eine Entwicklung auf, die den Automobilbau bereits revolutioniert hat. Vieles spricht dafür, dass damit auch im Holzbau eine ähnliche Entwicklung angestoßen wird, auch wenn sie hier noch ganz am Anfang steht.
Zu beobachten ist immerhin schon seit geraumer Zeit, dass das Interesse an Robotern im Holzbau kontinuierlich zunimmt.
Das hat Gründe:
1. Roboter sind flexibel. Mit der übergreifenden Produktionssteuerung der Fertighausfirma vernetzt, lässt sich der Roboter bei Bien-Zenker auf immer neue Situationen im Produktionsablauf einstellen. Das heißt in erster Linie, dass er in Echtzeit Informationen erhält, welchen Stiel er welcher Abholstation entnehmen und an die aktuelle Position im Rahmenwerk einlegen muss. Flexibilität heißt außerdem, dass der Roboter jede Art von Stiel in jedem beliebigen Winkel einlegen kann. Deshalb können auf der Riegelwerkstation in Schlüchtern auch Giebel- und Kniestockwände, Fenster- und Türöffnungen vollautomatisch hergestellt werden.
2. Roboter haben einen geringen Wartungsbedarf und sind ermüdungsfrei. Sie arbeiten nicht nur sehr schnell, sie halten diese Geschwindigkeit auch ohne Abstriche und Pausen während der gesamten Schicht. Körperliche Arbeiten werden deutlich reduziert, was zu einer Entlastung der Mitarbeiter führt. Da die Holzgewichte in der Fertigung kontinuierlich steigen, ist dieses Thema von zunehmender Bedeutung. Außerdem wertet die bessere Arbeitsergonomie den Arbeitsplatz auf.
3. Roboter sind Massenware. Das heißt zum einen, dass Holzbauunternehmen auf ausgereifte und bewährte Systeme zurückgreifen können, zum anderen, dass sich das Investitionsvolumen im Rahmen hält.
4. Positiv auf die Akzeptanz der neuen Systeme wird sich auswirken, dass der "Kollege Roboter" den Handwerker zwar entlasten, aber nicht ersetzen kann. In der Automobilindustrie hat sich gezeigt, dass gut ausgebildete menschliche Arbeitskräfte in der Produktion unverzichtbar sind. Dies war auch Bien-Zenker schon im Vorfeld der Investition bewusst.
5. Dank der Flexibilität der Industrieroboter ist auch ein Einsatz an anderen Stellen in der Produktion denkbar. Roboter sind die ideale Lösung für serielle Arbeitsschritte, an denen sie schnell und präzise arbeiten und ihre menschlichen Kollegen entlasten. Sie eignen sich auch für die Arbeit an Maschinen, die für den Menschen Gefahren bergen (z.B. Bandsägen). Einmal eingelernt, könnte ein Roboter zum Beispiel in Materialtransport und Lagerlogistik eingesetzt werden, etwa zum Sortieren und Einlagern von Beplankungsmaterialien. In der Fertigungslinie könnte es dann wieder ein Roboter sein, der die Platten aus dem Lager oder dem Transportsystem entnimmt und auf die Elemente auflegt. Derartige Überlegungen gibt es bereits im Fertigbau, erste Schritte in diese Richtung wurden bereits unternommen. Denkbar wäre auch, dass Roboter auf lange Sicht in weiteren Bereichen eingesetzt werden, etwa beim Aufbringen von Kleber oder Putz.
Die Elementfertigung läuft auf drei Linien
Die Dämmung wird bei Bien-Zenker momentan manuell eingelegt. Das passiert auf einer Fertigungslinie, die insgesamt fünf Arbeits- bzw. Wendetische und zwei WEINMANN Multifunktionsbrücken der Baureihe WALLTEQ M-380 umfasst. Letztere sind mit einem Zwölfachwerkzeugwechsler, Aggregatträgern auf beiden Seiten und je zwei parallel arbeitenden Klammergeräten ausgestattet, um eine hohe Bearbeitungsflexibilität und einen schnellen Workflow zu realisieren. Bemerkenswert: Die Arbeitstische, auf denen die Elemente gefertigt werden, versehen ihren Dienst in Schlüchtern bereits seit dem Jahr 1996. Die Beplankungsmaterialien werden von einem HOMAG Plattenbearbeitungszentrum BHC 911 vorkonfektioniert, das ebenfalls von einem automatischen WEINMANN Handlingsystem STORETEQ H-700 beschickt wird. Die Platten werden für die automatische Fertigungslinie nur auf Kontur zugeschnitten und per Rollwagen an den Übergabepunkt bei den Multifunktionsbrücken gebracht. Letztere übernehmen nach dem Auflegen per Saugheber die restlichen Bearbeitungsschritte. Bei den Platten für die manuellen Linien werden auch die Öffnungen für Steckdosen, Schalter etc. im Plattenbearbeitungszentrum vorbereitet. Trotz der Flexibilität der Hauptlinie sind diese Nebenlinien parallel im Betrieb, um auf der Hauptlinie Belastungsspitzen abzufedern und Kniestockwände zu produzieren, die wegen ihrer geringen Höhe (≤100 cm) nicht über die Riegelwerkstation laufen können. Nach der zweiten Beplankung auf der Hauptlinie trennen sich die Wege der einzelnen Elemente: Innenwände gehen in die Qualitätskontrolle und von dort weiter zu den Verladestationen, während Außenwände vor dem Verladen die Stationen für den Fenstereinbau, das Aufbringen des WDVS und der Fassade durchlaufen.
Nicht die Menschen beseitigen, sondern deren Fehlerquellen
Die 2017 in Betrieb genommene Fertigungslinie hat der Bien-Zenker GmbH einen deutlichen Zuwachs an Qualität und Kapazität gebracht, auch wenn sich das Unternehmen bei der Herausgabe von genauen Zahlen bedeckt hält. Als Indiz für die Leistungsfähigkeit der Anlage kann man aber nehmen, dass die derzeit ausgelieferte Stückzahl - im Schnitt rund drei bis vier Häuser am Tag - im Zweischichtbetrieb produziert wird. Im Zentrum der Automatisierung steht dabei der in die Fertigungslinie integrierte Industrieroboter, der dank Sechsachstechnologie die Anpassung des Einlegeverfahrens an unterschiedliche Stiele ermöglicht. Dies erhöht nicht nur seine Flexibilität und Geschwindigkeit, sondern sorgt darüber hinaus für eine höhere Betriebssicherheit. Bien-Zenker ist ein gutes Beispiel dafür, dass eine Automatisierung im Holzbau nicht zulasten der Mitarbeiter gehen muss: "Wir wollten menschliche Fehlerquellen aus dem Arbeitsprozess entfernen, nicht den Menschen selbst. Deshalb haben wir im Zuge der Modernisierung nicht etwa Personal abgebaut, sondern im Gegenteil neue Mitarbeiter eingestellt. Deren Arbeitsplätze sind deutlich attraktiver geworden, weil es uns wichtig war, dass die Menschen im Zuge der Automatisierung entlastet wurden." Zu den Voraussetzungen für einen reibungslosen Betrieb der Anlage gehört, dass man die Holzqualität auf die Anforderungen des erhöhten Automatisierungsgrads abstimmt. Auch andere Bereiche im Unternehmen - allen voran die Logistik - gilt es im Zuge der Neustrukturierung weiterzuentwickeln. Als Beispiel führt René Honrath den Umgang mit Beplankungsmaterialien an: "Früher konnte man bei den Platten vom Stapel runterarbeiten. Heute sind sie vorkonfektioniert, und wir brauchen ein wohldurchdachtes Konzept, um die einzelnen Plattenlagen zu sortieren, zu lagern und schnell wiederzufinden." René Honrath empfiehlt außerdem eine komplette Fertigungslinie aus einer Hand: "Da alle Komponenten einer solchen Fertigungslinie vernetzt und perfekt aufeinander abgestimmt sein müssen, ist es sinnvoll, wenn sie von einem Hersteller stammen. Der sollte insbesondere für die Steuerungssoftware die Verantwortung übernehmen." Von WEINMANN stammt deshalb nicht nur die neue Fertigungslinie, sondern auch ein Baustein der Produktionssteuerung.
Ein Artikel des Fachmagazins bauen mit Holz, Ausgabe 09/2018. Hier lesen Sie den kompletten Artikel.
„Durch den Einsatz eines Industrieroboters haben wir heute eine deutliche Leistungssteigerung sowie eine klare Verbesserung in der Maßhaltigkeit der Bauteile.“Herbert Vestert, Produktionsleiter