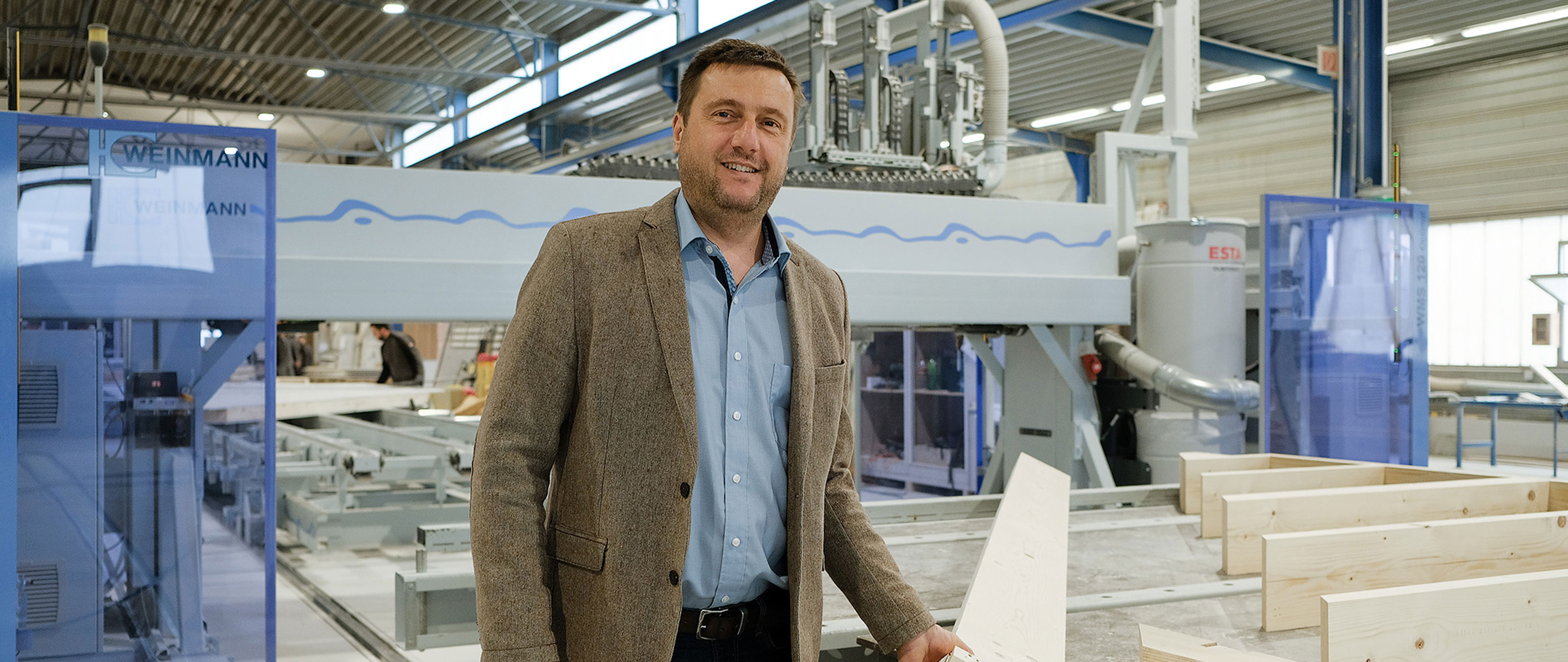
Die neue Fertigungslinie von WEINMANN war gleichzeitig auch ein Pilotprojekt für künftige Großinvestitionen. Und der Ausgangspunkt für eine tief greifende Vereinheitlichung der Prozessleittechnik im Unternehmen. 2019 habe Elk die Fertighausproduktion von zwei Standorten im niederösterreichischen Schrems konzentriert, berichtet Schandl: „Dadurch hatten wir von einem Tag auf den anderen eine Kapazitätserhöhung um fast 60 % und Zweischichtbetrieb. Da war die Frage, was tun wir? Einerseits wollten wir modernisieren, aber auch in der Umbauphase weiterproduzieren. Deshalb war WEINMANN so interessant für uns, das war praktisch die einzige Plug & play Anlage. Die man anschließt und mit der Produktion beginnt. Und die vor allem in der industriellen Fertighausproduktion erprobt ist.“ Immerhin produziere man – trotz Corona – derzeit vier Häuser am Tag.
Kompakt und flexibel mit BEAMTEQ
Natürlich kann die Linie – zwei BEAMTEQ B-560 Abbundanlagen mit 6 und 13 m Arbeitslänge, eine WEINMANN 3-Tischlösung mit einer Multifunktionsbrücke WALLTEQ M-340 und zwei Wendetischen, sowie sechs Pufferplätzen– auch ganz normale Elemente produzieren, wird aber überwiegend für Schrägelemente und Überhöhen verwendet. „Gefertigt werden die komplette Zenker- Linie und dann für Elk alles was Giebel und Gaube ist, also die Schrägelemente.“ Für die „normalen“ Elemente habe man die wesentlich größere Hauptlinie, die aber durch ihre Serienfertigung unflexibler sei. Auf der WEINMANN-Linie bedeute ein Wechsel des Wandaufbaus viel weniger Aufwand, sagt Schandl: „Wir haben uns bemüht, alle Arbeitsgänge, die bisher manuell durch Mitarbeiter erfolgten, zu optimieren und dadurch die Taktzeiten zu verringern. Beispielsweise unterscheiden sich Hanfisolierungen oder Mittelschichtputz in der Taktzeit wesentlich vom normalen, seriengefertigten Wandaufbau. Hier konnten wir das meiste herausholen. Dann war das Thema Flexibilität vor allem für den deutschen Markt wesentlich. Dort sind überdurchschnittliche Wandhöhen ein Trend - genau genommen ähnelt kein Haus mehr dem anderen“, hält Schandl fest. „Grundsätzlich können wir auf dieser Anlage bis 4,5 m Höhe produzieren – transporttechnisch ist das aber eine andere Geschichte, bei 3,05 m ist es in der Regel aus. Alles darüber hinaus sind Sondertransporte.“
Prozessvernetzung Schlüssel für Produktivität
Mit der neuen Linie wurden auch alle Fertigungsprozesse vernetzt: „Wir haben uns ja alle Anlagen am Markt angesehen. Ein Punkt war natürlich schon, dass man alles aus einer Hand hat. Denn wir haben ja in diesem Umstellungsjahr auch die komplette Software getauscht und vereinheitlicht, beziehungsweise Schnittstellen etabliert. Von der Visualisierung über die Einreichplanung bis zur Maschinendatenerstellung. Das hatte ja noch einen zweiten Aspekt für die Zukunft – man könnte zwar mit den Daten unserer Sema Konstruktionsplanung die neuen WEINMANN-Anlagen direkt ansteuern. Aber nicht unsere Altanlagen. Deshalb war es nötig, dazwischen diese Granit-Schnittstelle zu stellen, die uns Produktionsdaten für alle Linien optimiert. Das ist einfacher, weil ich damit von der Lagerwirtschaft über Durchfluss- und Taktzeitoptimierung alle Möglichkeiten habe Anlagen anzubinden, wie zum Beispiel den Plattenzuschnitt. Die Auflösung solcher Inseln war ganz wesentlich für einen künftigen Ausbau.“
„Losgröße 1 ist die Zukunft“
„Wie kann man die individuellen Wünsche des Kunden in einen industriellen Fertigungsprozess fassen?“ fragt sich Schandl. Der Kunde erwarte, dass man seine Wünsche erfülle: „Also läuft alles auf eine Losgröße 1 Produktion im industriellen Maßstab hinaus. Andere Branchen machen das schon, wir versuchen das nun auf ein ganzes Haus anzuwenden.“ Man feile natürlich an Strategien für die Zukunft: „Die Frage, die sich mir stellt, ist, wie schaut das Fertighaus in 15 Jahren aus? Ich kann mir gut vorstellen, bei der Art und Weise wie wir produzieren viel zu verändern. Beim Puffer der neuen Linie haben wir das bereits verwirklicht. Fenstereinbau oder Verputz erfolgen am stehenden Element. Der geringere Platzbedarf ermöglicht mir einen größeren Puffer und damit ausreichende Trockenzeiten. Die kleine Linie hat insofern Pilotcharakter, als wir mit ihr Erfahrungen für künftige Investitionen sammeln konnten.“
Erfolgreiches Pilotprojekt
Entsprechend positiv bewertet Schandl die Zusammenarbeit mit WEINMANN: „Das Projekt war sehr erfolgreich. Wir konnten ab der Inbetriebnahme produktiv arbeiten. Der Aufwand für die notwendige Adaptierung an unsere Prozesse war erfreulich gering. Ja, wir sind mit WEINMANN als Partner zufrieden.“
Autor und Fotos: Robert Kittel
„Der Aufwand für die notwendige Adaptierung an unsere Prozesse war erfreulich gering.“Ing. Markus Schandl, technischer Leiter Elk-Haus
Elk-Haus
Das 1959 in Schrems gegründete Unternehmen beschäftigt heute über 1200 Mitarbeiter. Mit Niederlassungen in zahlreichen Ländern Europas ist das ELK Haus Unternehmen heute einer der europaweit führenden Hersteller für Häuser in Fertigbauweise.
Website