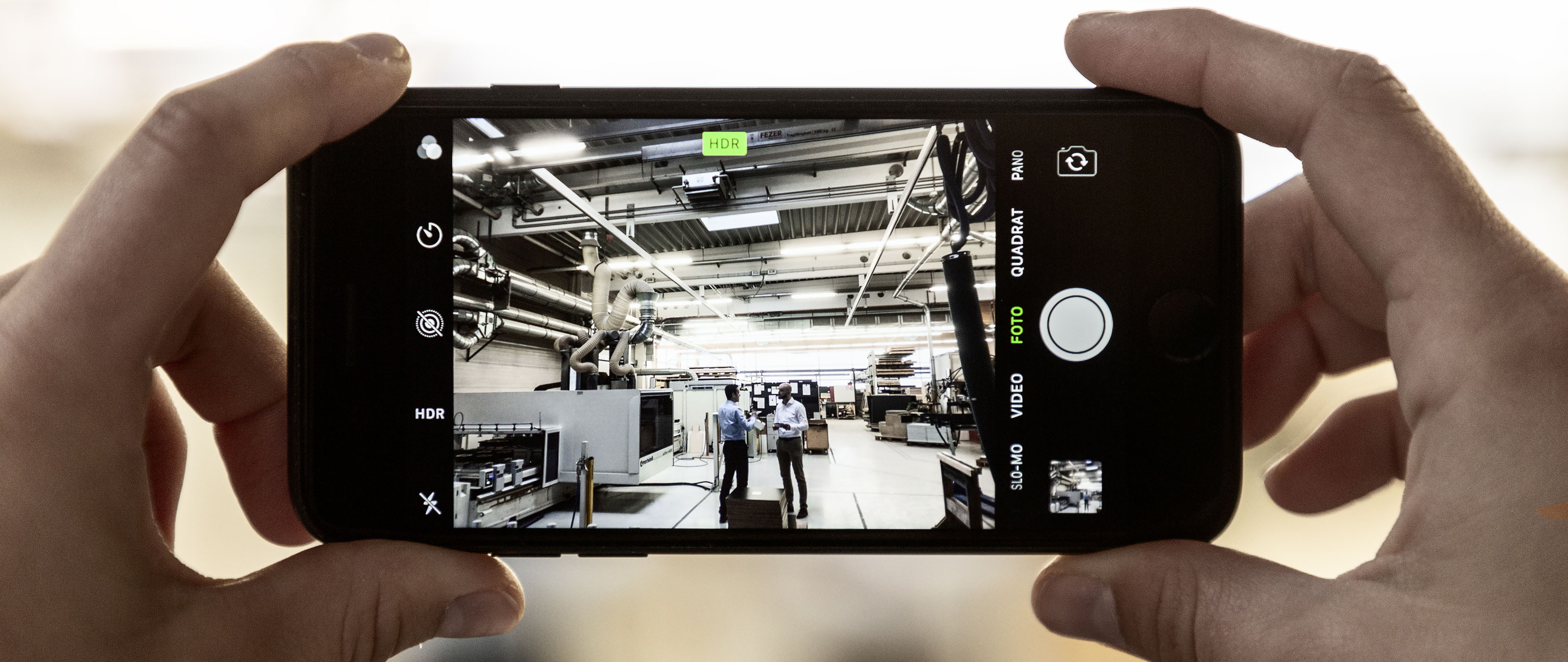
More and more companies are asking this question and are investing in the increasing range of IT solutions available on the market. In most cases, directly after the deal is closed, these solutions unfortunately fail to live up to expectations in terms of their integration into the existing IT infrastructure. Quite often, the standalone systems touted as the optimum solution can only be integrated into the existing system landscape to a limited extent. Due to budget restraints, the desirable objective of having a continuous information flow and integrated manufacturing is obstructed, often for several years.
Continuous production according to the Industry 4.0 vision, along with all related benefits, is only possible with a comprehensive system analysis of the existing IT infrastructure and considering the specific challenges of the industry. And as ever, not all the systems that are already in use have to be replaced immediately and not all the systems that are considered viable for the future meet the necessary requirements.
In April 2013, the german panel of experts for Industry 4.0 published the “implementation recommendations for the future project Industry 4.0” and quite a few people have been asking what the furniture industry has accomplished since then. To be able to evaluate that, one needs to take a look at the current state of the art of the software hierarchy applicable to our industry.
From the creation of a customer order at the point of sale to the final manufacturing process, the information flow passes three to four different software products. Each of these products is specially tailored to this field of application, therefore features its own data model. At each software hierarchy level, the order data is enriched for the respective processes, e.g. production.
Customers’ requests for increasingly customized products requires the production of highly diversified products, e.g., with batch size 1. The graphic planning of the piece of furniture is usually done directly in the shop, with features that are clearly described. Special features that can only be described in text form in the trade software require manual rework at the work preparation stage.
The vision of Industry 4.0
The current software landscape still requires separate databases and data models for the main systems. Ideally, standardized interfaces are used to forward data to downstream systems. Nevertheless, primarily older PPS solutions require redundant and duplicate data creation, storage and maintenance. The vision of Industry 4.0 is to have one singular cross-system database for all functions between CAX, ERP and MES.
This software architecture allows redundancies to be avoided, or at least substantially reduced. The database can be operated in the cloud, on a company-owned server or via an XaaS provider. However, from a system point of view, the reality is still far behind this vision, irrespective of the industry. As a result, even major providers, such as SAP or Oracle, are focussing more on their core processes and the related data models again, not least due to architectures that are ready for release.
The potential in existing fields of action
An uninterrupted and therefore low-maintenance information flow is also possible without the solutions with connections to a singular database which are not yet ready for introduction. Significant improvements can be made in daily working life with a targeted system change, the creation of new interfaces and the optimization of existing interfaces. These include:
- Efficiency increase in the manufacturing process
- Improvement of the material flow in production
- Increase in machine utilization time
- Reduction in administrative expenditure in IT
- Prevention of redundant and fault-prone data maintenance
These effects become increasingly noticeable, the better data is integrated into only a few databases.
By generating increasingly customized products, sales also continue to change from a B2B to a B2C market, outside of the trade associations. However, expectations of the traditional B2B business in terms of product variation and related systemic plausibility checks have also become increasingly demanding. Yet, with the expenditure required to functionally design the POS solution, it pays if the same data model can be used in trade and CAM. This even makes it possible to make the customer themselves act as the order entry division.
General data import proves to be increasingly problematic because many manufacturer-independent software products are used in trade.
Many companies therefore decide to completely do without data import, and even large companies often only manage to import a maximum of 50% of the trade orders. This is where great potential is still hidden in the cooperation between trade and manufacturer. Automation is already showing considerable gaps at the beginning of the process chain.
Connecting core systems
When using trade software, it is possible to import the standard items directly into CAD/CAM, while special items are designed, calculated and prepared for manufacturing directly in CAD/CAM.
CAD/CAM
Particularly for producing special solutions, the use of CAD/CAM systems offers great advantages:
- Systematic description of parts with all relevant features
- Automatic creation of manufacturing drawings, CNC programmes, item parts lists, and exploded-view drawings for assembly
- Control of all CNC machines of different manufacturers via post-processors
The use of a CAM system enables machine-independent design, leading to great time savings in the designing and manufacturing company departments as a result.
ERP
In the next step, the order generated in the CAD/CAM system can then be transferred to the ERP system via an interface. Parts or even entire parts lists can be passed to the ERP system. Billing and materials management are completely transferred to the appropriate system and centrally administered. If the ERP system offers additional possibilities for variant configuration, in addition to the usual tools for production management, then further plausibility checks can be introduced which help to prevent errors, e.g. in the procurement of material.
If the manufacturer does not use CAD/CAM, then the order is mostly generated directly from the trade software or is manually recorded in the ERP system. In this case, the CNC programme is created using ERP tables, but special parts still need to be manually recorded. These special parts are then produced with the help of suitable CNC software programmes at the work preparation stage, which is very time-consuming.
Most ERP systems are not capable of processing graphic representations, so in these cases an additional interface with a specific graphics system is usually required. In the furniture industry, PPS systems are still often used, which due to their rigid structures allow for only a few release-capable adjustments and are therefore extremely limited in terms of their functionality, data integration and flexibility.
MES
The use of MES (Manufacturing Execution System) in the furniture industry is still not widespread among small- and medium-sized companies. Often, the required manufacturing documents are still produced in ERP or PPS. Many manufacturers are satisfied with the creation of production orders and their rough scheduling in these pre-systems. For a better utilization of production capacities, it would however be possible to transfer these orders from the ERP system to an MES solution. In a partially or fully automated production, MES ensures a direct connection of the information systems to the machine level. This enables the directing, controlling and monitoring of production in real time. Alternatively, production orders could be directly created or taken over from the used CAD/CAM systems. The MES also records machine and operating data and sends it back to the information systems. The use of an MES solution automates the following:
- Sending information back to materials management and commercial order processing
- Recording of operating, production and product data and transferring this to the reporting level
- Controlling of production control stations and related resource utilization
- Creation of planning periods in manufacturing, depending on current prioritization
- Manufacturing processes and resource planning for production
- Planning and execution of maintenance work
- Administration of production means
When selecting an MES solution, the focus is on the flexible applicability to technological requirements in the furniture industry, such as cutting, nesting or batch size 1. Ideally, the data is passed to the existing or planned systems via standardized interfaces.
Inventory changes should also be recorded via the MES so that the information can be sent back to the ERP system. This automates the process of creating procurement proposals. In order to achieve paperless manufacturing, production should be equipped with terminals, which enables, among other things, the visualization of manufacturing orders, including required drawings and the related CNC programmes.
Most companies still have a long way to go before they reach this stage. However, given the increasingly short reaction times, this step starts to really pay off, because it means that orders that are already in production can still be changed in some circumstances. It is important that the usual manufacturing principles (make to stock, make to order, assemble to order) can be implemented.
Conclusion
Even five years after the implementation recommendations made by the Industry 4.0 work group, many areas of the furniture industry are still lagging far behind the existing possibilities of a connected, automated production. IT structures that have grown over the years build on individual or standalone solutions and therefore consist of many databases and data models that need to be operated manually in parts.
To a great extent, systems are connected via insufficiently developed interfaces and often cause redundant data creation and data administration, which, in turn leads to high expenditure and error rates. The greatest source of potential in the industry certainly lies in the fact that POS, complete ERP and MES solutions are mostly not in place. And still many continue to neglect this opportunity.
The international context has shown that technological pioneers in terms of the level of automation are furniture producers that manage to free themselves from the old system landscape. The coming 5 years will be decisive for traditional companies if they seize the opportunities of Industry 4.0. In any case, the face of the international furniture industry will change drastically given these developments.
Text and pictures: Klaus Fickler and Elias Wagner (SCHULER Consulting)