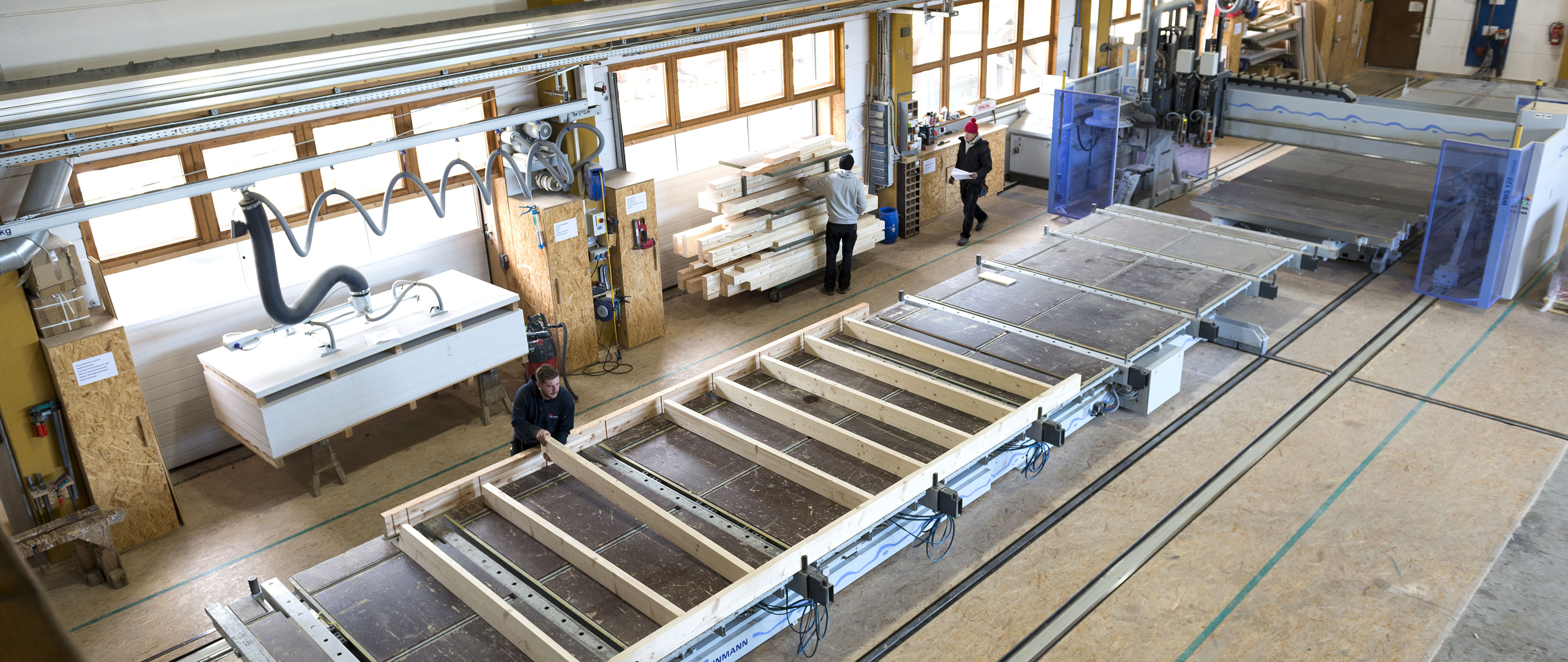
An article from the specialist magazine Mikado, 07/ 2016.
Here you can read the article on www.mikado-online.de.
The question is what a small and a large timber work company have in common. The answer is currently obvious: high levels of utilization and good opportunities for growth. In many companies, the order book is so full that meeting demand will take well into next year. In practical terms, this has canceled out the advantage of short construction times, which is an important aspect of timber work.
So the answer appears to be to increase capacities.
Not the easiest thing to do at a time when there is a chronic shortage of skilled staff. Many companies are therefore modernizing their production facilities — and this is where the difference between small and large comes back into play.
Where large companies are primarily interested in the capacity of a new production line, small operations have other questions. One person who has some extraordinary answers to these questions is Andreas Gamper from Bellenberg, Germany. His joinery business, which also handles roofing and plumbing, is where he plans and builds family homes, extensions and loft extensions, as well as industrial and commercial buildings and residential buildings up to a height of 13 meters.
With the growing number of orders, Gamper's company has grown in recent years and the outlook is positive as well. Currently, around 20 houses are built in Bellenberg every year, and on top of that, timber frame elements for office and administrative buildings are also manufactured increasingly often.
While restructuring the company in 2014, Gamper purchased a WEINMANN compact line with turningtable and multifunction bridge. That meant that integrating the existing WEINMANN assembly table into the compact line was straightforward. Regarding profitability, Gamper says: "Of course I can use the machine to produce at a lower cost, but calculating profit isn't a priority for me. If I were only thinking about profit, then I'd also have to ask myself whether my truck or my beam processing system pay for themselves; although both of them see pretty heavy use, they can also stand idle for maybe two weeks at a time. Thinking like that would just put me under pressure and then that would result in poor prices."
If we look at the sample calculations from WEINMANN Holzbausystemtechnik, Gamper and his company are already in the black. The breakeven point is achieved from around 15 houses or the corresponding element area in a year.
It can be even earlier, depending on the complexity of the element construction and the targeted product price. This is because savings are made both in terms of pure processing time for the plant and as a result of avoiding significant non-productive times for manual production. To give an example, drilling a socket manually involves a lot of individual steps: reading the drawing, marking the box, fetching the tools, drilling the socket, clearing up the material and so on. None of these steps are necessary during automated manufacturing.
Furthermore, the issue of monitoring product quality becomes even more important. In this context, implementing the static calculations and the associated number and spacing of the staples is a not insignificant quality aspect, which can be guaranteed using the multifunction bridge.
However, Gamper Holzbau had different reasons for the new purchase: "We built a new hall for our beam processing system and we also restructured production in the old hall during this expansion." Initially, that meant three new gates in the side of the hall for the company, so that materials could be supplied for production.
Level of prefabrication and employee motivation
The carpenter felt that there were several reasons for a compact line: "First of all, I wanted to optimize production and increase the level of prefabrication. Next was motivating employees by providing an attractive workplace, where people would no longer have to mark up by hand and then climb on the elements with a circular saw, trimmer or nailer.
Nowadays, the multifunction bridge has automated these process steps, while employees clear up around the machine. The result is a pleasant, clean workplace, where everyone enjoys working and where we can bring potential customers at any time. And problem areas that were difficult to get to and which possibly even distorted themselves are no longer an issue. All in all, production is now more rounded and professional and takes place in a much better environment."
Gamper sees a third advantage: the fact that the new technology has freed up proven employees, who he can use in other areas. This alone has significantly increased the production capacity. From the joiner's point of view, production at the company is now also much more "powerful". In other words, in busy periods it's easier to absorb order peaks, insert short-term orders in between and serve builders with a very tight time window.
Better workflow in the company
The new technology has also improved the workflow in the company; to the right of the compact production line, there is still enough room to install the windows in the elements. Completed elements are positioned vertically for this purpose and are loaded onto transport carriages, which can be moved through the hall on rollers. After installing the windows, a forklift truck carries the carriages through the old gate into the yard, where they are loaded up. So the material flow, which used to be restricted to one gate, now runs smoothly across the hall.
With hindsight, Gamper views the purchase of the compact line as a wise investment: "We have achieved the related goals and the collaboration with WEINMANN was positive throughout (with the exception of a misunderstanding about the production layout). All in all, I see the restructuring and the new production technology as important course markers that will prepare my company for further growth in the next few years."
Investment sets the course for the future
Although Wolf System in Osterhofen, Germany is in a different league, some of the frame conditions and intentions are definitely comparable. This company also views investment in a production system as an important course marker for the future and here it also forms part of a solid growth strategy that has been in place for years. This company also produces elements for family homes and apartment buildings, alongside — following a strongly rising trend — components for commercial buildings (offices, sales outlets etc.) and communal buildings such as schools and kindergartens.
The company also has a good market standing in Osterhofen, with the German branch being part of a group of companies. This branch is involved in the construction of tanks and silos for agriculture and industry, as well as in steel, concrete and timber constructions in agricultural, commercial and industrial construction and in building turnkey family homes and apartment buildings.
The company has dramatically accelerated timber work in the last ten years, as it sees significant potential for growth in this field. In 2011, Wolf System purchased a WEINMANN plant with four work tables and two multifunction bridges. Since they did so with an eye on increasing capacity, the plant is optimized for a fast production speed. With this goal in mind, the usual "bottlenecks" were reduced by distributing time-consuming activities (positioning the timber frame, installation, inserting the insulation, applying the external insulation) across several tables.
The figures speak for themselves
In order to make full use of the potential of the plant, the material pathways around production have also been optimized. Materials for beam processing, sheathing, installation and insulation are positioned at the appropriate stations right next to the production line. Elements that have left the work table are taken away using transport carriages; the windows are installed in the elements which are then taken to the plaster station or placed in the wall magazine. This peripheral area was also planned and supplied by WEINMANN.
Given that the timber frame constructions were previously supplied from partners within the group, the in-house capacities in Osterhofen have since been utilized to achieve a significant level of growth. In 2011, Wolf System sold around 100 wooden houses; by 2015, the figure had risen to 180. In the last year, the WEINMANN line has been used to produce approximately 62,000 m² in elements for timber panel construction.
Managing Director Jean-Luc Herrmann cites the expansion of timber panel construction from house construction to commercial construction as one of the reasons for purchasing the production line: "We also wanted to increase our level of prefabrication. In view of the shortage of skilled staff, it makes sense to slim down the assembly sequences and thus to reduce the man hours (and the sources of errors).
This applies to commercial construction as well as timber house construction; in terms of the former, for example, we install the holders for the facade systems on the elements as early as in the beam processing hall. The reduction in assembly times that is generated by prefabrication also delivers a significant cost advantage for us."
Second production line already in the pipeline
In the meantime, reality has already overtaken the growth scenario from 2010/11. The company in Osterhofen is already reaching the limits of its production capacity again, even though the WEINMANN plant is operating in two shifts. From time to time, they even have to outsource part of production to subsidiaries.
As a result, the hall for a second line is already being constructed in Osterhofen. It will include three tables and a multifunction bridge and (from the middle of the year) it will produce all the elements that do not have exterior plaster; in other words, internal and external walls with a hanging facade. The tables for the production of roof and floor elements — which are currently still located next to the four-table system — will also move into the new hall.
In the future, the four-table system will only be used to manufacture external wall elements, which have a compound heat insulation system. This will mean a production process without any changeovers and should improve the work flow still further.
Herrmann's assessment of the collaboration with the machine manufacturer was — and still is — positive: "They gave us good advice and the first plant operated smoothly right from the start. If we ever have any questions, then we simply give them a call and talk things through. At the start, we just had to adjust our IT systems, as we have our own in-house programmers who program our CAD macros and control the EDV interfaces."
That makes sense as the company in Osterhofen also uses CNC-controlled machines in other areas — for example, in steel construction, where drilling and sawing components is CNC-controlled. The advantage is that, with mixed constructions — for instance, in halls with steel supporting structures and timber panel walls — everything is from one source and fits precisely. And if there are bottlenecks in production, the subsidiaries in the group can share orders amongst themselves simply by sending the data records.
This alone is good reason for Wolf System to think in industrial terms and manufacture using CNC-controlled production systems in timber work as well. The profitability of these systems is not in any doubt in Osterhofen: at full capacity with a two-shift operation, a figure of more than 180 houses a year and numerous projects from industrial and commercial construction, there is no alternative to industrial manufacturing anyway.
Published in Mikado 7 / 2016
Many thanks to the editor Jessica Jahn and Dr. Joachim Mohr
Many thanks also to our customers Gamper Holzbau and Wolf System
“I see the restructuring and the new production technology as important course markers that will prepare my company for further growth in the next few years.”Andreas Gamper, Gamper Holzbau - Bauprojekt GmbH
Downloads
Gamper Holzbau
From a traditional company for carpentry, roof and tinsmith works, Andreas Gamper Holzbau developed to a modern timber framer. Gamper connects design, practical construction methods and current scientific knowledge.
Wolf System
As a part of the Wolf System group, this branch is involved in the construction of tanks and silos for agriculture and industry, as well as in steel, concrete and timber constructions in agricultural, commercial and industrial construction and in building turnkey family homes and apartment buildings.