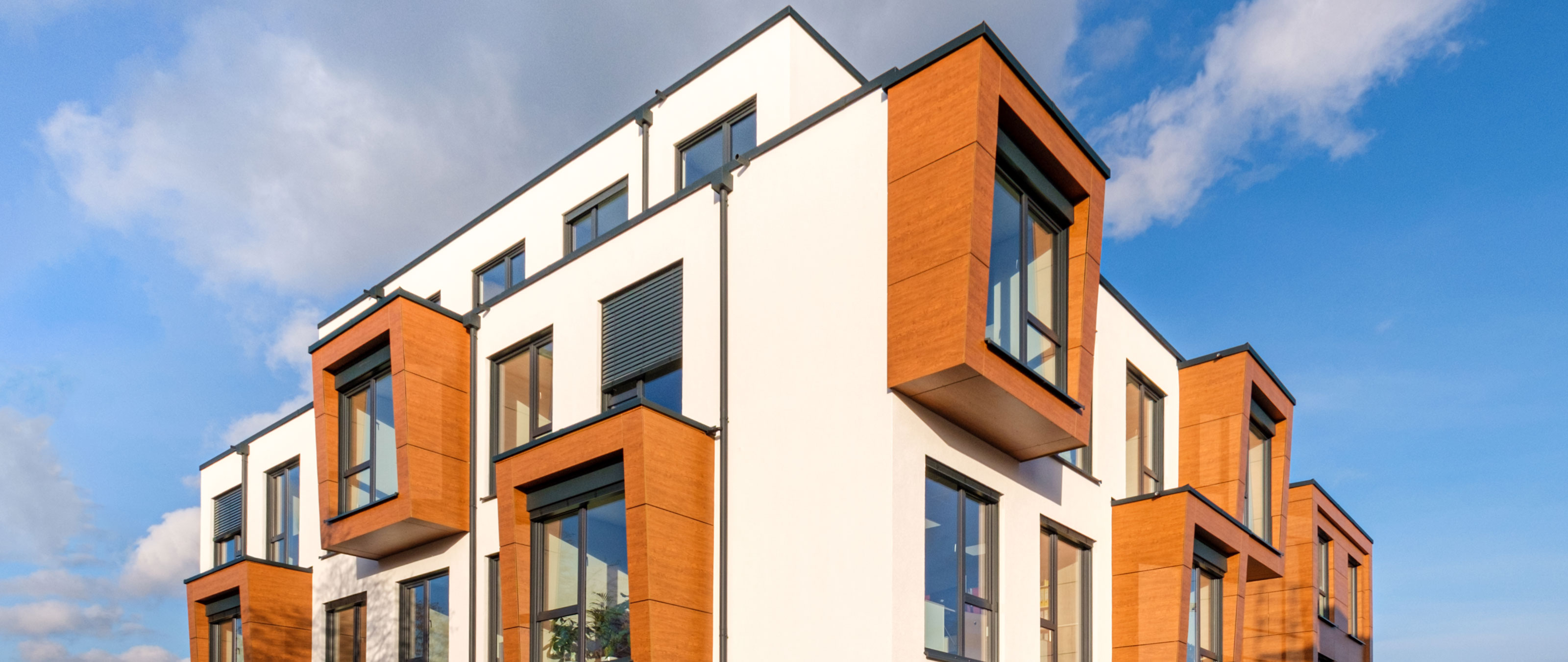
Stefan Höötmann lässt sich ungern von der Arbeit abhalten. Als er sich entschlossen hatte, die Elementfertigung in seiner SH Holz & Modulbau GmbH zu automatisieren, akzeptierte er deshalb keine Verzögerung durch Lieferzeiten: „Die WEINMANN-Selbstbautische hatten wir sofort am Start, auf unsere Multifunktionsbrücke – eine WALLTEQ M-380 – können wir etwas warten, weil wir ja bislang schon manuell produziert hatten.“ Seine Abbundanlage wollte der Unternehmer aber sofort: „Da hatte ich die Einstellung: Wenn ich keinen Mercedes kriege, komme ich auch mit einem VW ans Ziel. Deshalb hatte ich mir schon in Italien eine gebrauchte Abbundanlage angeschaut und war kurz davor, sie zu kaufen. Bei der reinen Absicht blieb es dann aber auch, denn Weinmann machte Stefan Höötmann ein Angebot, das er nicht ablehnen konnte: „Man stellte mir leihweise eine andere Abbundanlage in die Halle – für mich eine Superlösung, die auch optimal abgewickelt wurde: Wenn meine BEAMTEQ B-660 kommt, wird die Leihmaschine abgeholt und weiterverkauft. So etwas liebe ich: wenn nach Lösungen gesucht wird, statt nur die Probleme herunterzubeten. Und diese Lösung passte perfekt.“
Start als verlachter Holzbau-Exot
Damit war ein weiteres Kapitel in einer Firmengeschichte geschrieben, in deren Verlauf sich Stefan Höötmann als ähnlich dynamisch erwiesen hatte wie beim Maschinen-kauf: 1998 als klassische Zimmerei gegründet, stieg sein in Lingen an der Ems ansässiges Unternehmen 2004 in den Holzrahmenbau ein: „Das war es, was wir wollten, so konnten wir die Zügel bei unseren Aufträgen sehr viel besser selbst in der Hand halten.“ Zwar war man damals als Holzbauer in der Region noch ein absoluter Exot, zeigte dem staunenden Publikum aber, „was sich mit Holz alles machen lässt“. Nach diesem Motto erarbeitete man sich – zunächst unter privaten Bauherren – einen exzellenten Ruf. Durch die Nähe zu den Niederlanden „rutschte“ das Unternehmen außerdem auch in den Modulbau für holländische Auftraggeber hinein: Diese Bauweise war hinter der Grenze schon weit entwickelt. „Das machte uns noch mehr Spaß“, erinnert sich Stefan Höötman heute: „Hier hatten wir einen noch höheren Vorfertigungsgrad, waren noch unabhängiger von externen Handwerkern – zum Beispiel davon, wann die Fensterbauer oder Fliesenleger auf die Baustelle kommen. So konnten wir noch schneller mehr bewegen.“ Grund genug, die Modulbauweise ins damals noch weitgehend ahnungslose Norddeutschland zu importieren: „Als Holz- und Modulbauer hat man uns damals in der Region ausgelacht“ – was vielleicht auch mit der schlechten Qualität der holländischen Modulgebäude zu tun hatte. Die hatte man auch in Lingen konstatiert, weshalb man in der Folgezeit die Modulbauweise an die höheren deutschen Qualitätsansprüche adaptierte.
Seit 2015 als Modulbauer etabliert
2008 kam dann mit einem Gewerbeobjekt für BP der Durchbruch: „Das Unternehmen wollte für vier Jahre ein temporäres Bürogebäude für 120 Mitarbeiter. Wir bekamen den Auftrag und haben ein dreigeschossiges Modulgebäude mit 3500 m2 Nutzfläche geliefert, dessen Qualität so hoch war, dass BP es bis heute nutzt.“ In Lingen hatte man aus diesem Projekt die Erfahrung mitgenommen, „wie viel Zeit und Geld wir bei einem Großprojekt einsparen können. Wahnsinn!“ Stefan Höötmann beschloss also, sein Unternehmen in Richtung Objektbau weiterzuentwickeln. Zwar musste man in der Folge der Finanzkrise zunächst kleinere Brötchen backen, nutzte die Zeit aber konsequent zur Optimierung des eigenen Modulbausystems. 2015 folgte dann der Einstieg in den seriellen Modulbau von Flüchtlingsheimen, 2016 eine Partnerschaft mit der Vonovia, die aus Lingen modulare Wohngebäude beziehen wollte. „Das war der Start-schuss für eine rasantes Wachstum“, bilanziert Stefan Höötman im Rückblick. Wir mieteten Hallen für die Modulproduktion an – die braucht ja vor allem viel Platz – und bringen es heute auf eine Hallenkapazität von 13000 m2 an vier Standorten.“ Die Partnerschaft mit der Vonovia lief aus, an ihre Stelle traten Rahmenverträge mit den Großstädten Köln und Hamburg, denen man regelmäßig Wohngebäude zum Festpreis liefert. Außerdem baut die SH Holz & Modulbau GmbH heute Bürogebäude, Schulen, Kitas, Pflegeheime und wie man hofft demnächst auch wieder Hotels. 2021 bezog das Unternehmen sein neues repräsentatives Bürogebäude, das es in Modulbauweise erstellt hat. Momentan ist man in Lingen gerade dabei, die Produktionsabläufe in den Hallen neu zu organisieren. Aus dem Geschäft mit den privaten Bauherren hat sich Stefan Höötman komplett verabschiedet: Aufträge übernimmt er heute erst ab einer Projektgröße von 700 m2 Nutzfläche.
Kleines Team, große Wirkung
Dabei hat der Unternehmer vor allem die Rentabilität im Blick: „Der Aufwand ist bei einem Einfamilienhaus nicht viel kleiner als bei einem großen Gebäude – man muss zum Beispiel beide bemustern. Der Umsatz ist aber bei einem Objektbau sehr viel größer. Um den gleichen Gewinn mit Einfamilienhäusern zu erwirtschaften, hätte ich also gar nicht genug Personal.“ Dies nicht wegen des allgemeinen Fachkräftemangels, sondern weil es zu Stefan Höötmanns Firmenphilosophie gehört, mit einem schlanken Team viel zu bewegen: „Derzeit haben wir 35 Mitarbeiter, etwa die Hälfte im Büro, die anderen in der Halle.“ Dass er mit einem derart kleinen Team auch große Volumina stemmen kann, erreicht Stefan Höötmann durch den Einsatz von Nachunternehmern: „Wir übernehmen mit unseren Mitarbeitern nur die Elementfertigung und die Modulmontage. Sollten unsere Kapazitäten nicht ausreichen, kaufen wir auch Elemente zu. Den Ausbau vergeben wir an bewährte Partner aus dem Handwerk So können wir unsere Kapazitäten schnell und flexibel anpassen, bei Bedarf zusätzliche Handwerker für Großaufträge beauftragen, was für deren Unternehmen angesichts einer Vorlaufzeit von einem halben Jahr kein Problem ist.“ Dies umso mehr, als für die Handwerker mit dem Modul-bau etliche Vorteile verbunden sind: Sie arbeiten – bei Bedarf auch im Schichtdienst – unter kontrollierten und ergonomischen Bedingungen an einem festen, witterungsgeschützten Einsatzort mit kurzen Anfahrtszeiten. Ihr Material können sie bequem zum Arbeitsplatz fahren, statt es auf der Baustelle in mehreren Stockwerken zu verteilen. Vorteile, von denen auch die Mitarbeiter von SH Modulbau profitieren: „Keiner hat heute mehr Lust auf Baustelle. Bei uns reduzieren sich Außeneinsätze auf zwei- oder dreimal 14 Tage im Jahr, da macht es allen Spaß, auch mal rauszukommen. Wir hatten deshalb nie Probleme, neue Leute zu finden. Wenn es bei uns einen Flaschenhals gibt, ist es nicht das Personal, sondern die Hallenkapazität.“
Planung mit Affinität zum System
Auch bei der Planung arbeitet Stefan Höötmann gerne mit Externen zusammen: Im gut besetzten Büro der SH Holz & Modulbau GmbH werden nur die Arbeitsvorbereitung und die Werkpläne erstellt. Wichtig ist, dass das Unternehmen zu einem möglichst frühen Zeitpunkt ins Projekt einsteigen kann: „Beim Modulbau ist das zwingend erforderlich. Man kann damit schicke und hochqualitative Gebäude bauen – auch individuell nach Kundenwunsch. Man braucht in der Planung aber dennoch eine gewisse Affinität zum System. Wie wichtig das ist, haben wir gerade bei einem Pflegeheim erlebt, das von einem Architekten modifiziert wurde, bis es kein modulares Gebäude mehr war und wir den Auftrag ablehnen mussten.“ Dies, obwohl man mit dem hauseigenen Modulsystem sehr flexibel bis fünf Geschosse bauen kann. Die Module haben variable Größen bis 13,50 x 4,70 m, wobei das Vorzugsmaß für die Breite bei 3,40 m liegt. „In diesem Rahmen können wir spielen, bauen derzeit zum Beispiel eine Schule mit großen, offenen Raummodulen und 8,00 m Deckenspannweite. Was mit Modulen nicht klappt, machen wir auch mit Stahl und Beton. Wir würden zum Beispiel nie eine Aula aus Modulen bauen. Wir haben bei unseren Aufträgen also wenig Einschränkungen – aber es gibt eben auch Grenzen der Flexibilität.“ Deshalb vergibt man in Lingen die Planung in der Regel an drei Planungsbüros, mit denen man schon länger kooperiert. – Ein Verfahren, das anfangs nur zähneknirschend akzeptiert wurde, dass sich aber mit zunehmendem Bekanntheitsgrad der Firma etabliert hat. „Heute planen unsere Kunden problemlos mit unseren Planungsbüros – auch wenn sie wissen, dass die Preiskalkulation erst am Ende der Modulplanung steht und sie unsere Pläne zu diesem Zeitpunkt praktisch nicht mehr mit einem konventionellen Unternehmen umsetzen können.“
Modulbau als Problemlöser
Woher dieser Vertrauensvorschuss? „Weil wir heute den Nerv der Zeit treffen, weil sich inzwischen herumgesprochen hat, dass die Bauweise hervor-ragend funktioniert und den Auftraggebern neben etlichen Vorteilen auch mehr Sicherheit bringt. Das ist wie beim Auto: Das wird von einem Hersteller geplant und produziert, und wenn er das vernünftig macht, weiß der Kunde genau, was er wann zu welchem Preis bekommt.“ Das ist natürlich nicht alles. Kunden schätzen an dem Modulbauer aus Lingen auch, dass er als Problemlöser auftritt. Etwa wenn es darum geht, eine Aufstockung in der Großstadt in extrem kurzer Bauzeit und mit minimaler Beeinträchtigung der Umgebung abzuwickeln. Ein Modulbau bedeutet hier zwei Wochen Großbaustelle, danach fahren nur noch hin und wieder Kleinfahrzeuge vor. Da darf man schon etwas teurer sein, zumal der Kunde, wenn man möglichen Ärger einpreist, nicht selten unter dem Strich Geld spart. Als Beispiel führt Stefan Höötmann die Aufstockung über einer Klinik an: „Dort hatte man sich für einen Massivbauer entschieden, weil der um 20 Prozent günstiger anbot als wir. Am Ende musste der Klinikbetrieb wegen Lärm, Schmutz und Nässe über mehrere Monate eingestellt werden, die Löhne und Gehälter für das Klinikpersonal liefen weiter. Wir wären in zwei Wochen praktisch fertig gewesen. – Man darf nachrechnen, welche Variante am Ende günstiger war.“ Ein zweites Beispiel für den Problemlöser-Bonus ist ein geschlossener, 250 m langer Verbindungsgang zwischen zwei Klinikgebäuden. Er führt auf Stützen über ein Klinikgelände mit regem Fahrzeug- und Fußgängerverkehr. SH Holz & Modulbau bot für das Projekt 20 Module mit 19 Stützen an. Die sollen, nachdem die Stützenfundamente mit Kleinbaustellen vorbereitet wurden, in 20 Tagen auf dem Gelände montiert werden – pro Tag eine Stütze und ein Modul. „Ein konkurrierender Massivbauer bot 80 Stützen und ein halbes Jahr Bauzeit an“, erinnert sich Stefan Höötmann. „Obwohl er um die Hälfte billiger war, bekamen wir problemlos den Zuschlag.“ Ein weiterer Pluspunkt für den Modulbau ist die erforderliche Bauherrenressource. Während zum Beispiel der Bauleiter einer Stadt bei konventionellen Wohnbauprojekten regelmäßig auf der Bau-stelle präsent sein muss, wird er bei einem Modulprojekt nur im Planungsprozess und bei der Übergabe aktiv. In der Produktionsphase hat er Kapazitäten frei und kann sich um andere Projekte kümmern, weshalb eine Stadt oder eine Wohnungsgesellschaft mit der Modulbauweise etwa viermal so viel Projekte mit dem gleichen Personaleinsatz abwickeln kann.
Industrielles Bauen
Zentrale Voraussetzung all dieser Vorteile ist eine konsequente Industrialisierung der Bautätigkeit. Ist sie umgesetzt, wird ein Modulgebäude zum Produkt, das unter kontrollierten Rahmenbedingungen gefertigt und als Komplettleistung an seinen Bestimmungsort geliefert wird. Die Bautätigkeit vor Ort reduziert sich auf ein kurzes Zeitfenster für die Montage, die Abhängigkeit von äußeren Einflüssen wie der Witterung oder negativen Wechselwirkungen zwischen den einzelnen Gewerken sinkt gegen Null. Im Zentrum des Bauprojekts steht neben der Planung und Arbeitsvorbereitung die Fertigung der Module in der Halle, die nach dem Vorbild der Automobilindustrie weitgehend automatisiert und rationalisiert werden sollte. Industrielles Bauen macht es dann auch möglich, die Synergieeffekte der Standardisierung und Serialität konsequent zu nutzen. Nicht umsonst hat Stefan Höötmann bei der Produktion von 13 baugleichen Flüchtlingsheimen die Erfahrung gemacht, „dass wir durch die Wiederholung der immer gleichen Abläufe weniger fehleranfällig waren und Arbeitszeiteinsparungen von bis zu 30 Prozent zu verzeichnen hatten. Das haben wir gemessen, da muss der Weg für uns hingehen. Mit einer automatisierten Fertigung werden wir diese Synergieeffekte künftig noch gründlicher ausschöpfen können.“ Die Kontaktaufnahme mit dem Maschinenbauer WEINMANN, der als Teil der HOMAG Group für die Automatisierung im Holzbau steht, war unter diesem Aspekt ein weiterer Schritt in die richtige Richtung. Für Stefan Höötmann ist er Teil seines Bestrebens, „alle Prozesse rund um den Bau selbst in der Hand zu haben und konsequent zu optimieren. Im Bereich der Produktion bedeutet dies einen schnelleren Workflow durch automatisierte Fertigung, außerdem höhere Stückzahlen bei schneller Reaktion auf Auftragsspitzen. Nicht zu vergessen die höhere Qualität – manuell wurden bei uns immer noch zu viele Fehler gemacht.“ Auch in der der Modulmontage will der Zimmermann künftig weitere Rationalisierungspotentiale nutzen: „Momentan stellen wir die Module noch in der Halle ab, montieren sie, bauen sie aus, verpacken sie und transportieren sie ab. So kriegen wir die Module erst raus, wenn sie alle fertig sind – wenn es bei einem ein Problem gibt, ist die ganze Halle blockiert.“ Ein System, das lange funktioniert hat, bei den heutigen Volumina aber an seine Grenzen stößt. Ab 2023 Jahr will das Unternehmen deshalb ein Schiebesystem etablieren, mit dem man die Module durch die Halle fahren kann. „Dann kommen sie zum Handwerker, der in der Halle eine feste Station hat. So können wir jeden Tag ein Modul fertigstellen und draußen lagern.“ Damit hätte die SH Holz & Modulbau GmbH ihre Hausaufgaben gemacht. Im Bereich der Fremdgewerke sieht Stefan Höötmann allerdings noch Nachholbedarf: „Auch die Nachunternehmer haben ja Einsparungen durch die rationale Arbeit in unserer Halle. Allerdings hat sich hier noch nicht die Erkenntnis durchgesetzt, dass man zumindest einen Teil dieser Einsparungen in eine Verbesserung der Kostenstruktur einfließen lassen könnte.“ Darüber hinaus könnten Elektriker und Installateure Kabel- oder Leitungsstränge vorfertigen und in der Halle einbauen. „So könnten sie zusätzliche Kostenpotentiale nutzen, aber leider fehlt vielen Handwerkern dafür noch das Verständnis. Dennoch bin ich überzeugt: Wenn wir beim Modulausbau weitere Schritte in die richtige Richtung machen und darüber hinaus die Möglichkeiten von Großmengenrabatten intensiv nutzen, wird der konventionelle Massivbau immer weniger mit uns mithalten können.“
Dass die Visionen des Zimmerers ernst zu nehmen sind, beweist der Aufstieg seines Unternehmens. Er hat viel dazu beigetragen, dass der Modulbau heute auch in Norddeutschland in aller Munde ist und längst nicht mehr als minderwertige Bauweise angesehen wird. Der SH Holz & Modulbau GmbH hat er eine Marktposition gesichert, in der sich das Unternehmen als einer der ganz wenigen Anbieter ausschließlich auf den Modulbau konzentrieren kann. – Seit sich das herumgesprochen hat, tauchen in der Region erste Nachahmer auf.
Ein Artikel aus dem Kundenmagazin performance 22 | 2023. Mehr Informationen finden Sie hier!
„Im Bereich der Produktion bedeutet dies einen schnelleren Workflow durch die automatisierte Fertigung, außerdem höhere Stückzahlen bei schneller Reaktion auf Auftragsspitzen. Nicht zu vergessen die höhere Qualität – manuell wurden bei uns immer noch zu viele Fehler gemacht.“Stefan Höötmann
SH Holz & Modulbau
Die SH Holz & Modulbau GmbH hat ihren Ursprung in einem traditionellen Zimmereibetrieb und hat sich in den letzten Jahren zu einem innovativen Modulraumhersteller entwickelt. Seit über 25 Jahren ist das Unternehmen auf den Baustoff Holz spezialisiert. Die Gründung der SH Holz & Modulbau GmbH erfolgte 2009 als Spezialanbieter für Modulbauten und seitdem wurden bereits über 100 Projekte umgesetzt. Das Unternehmen realisiert Wohngebäude, Büro- und Betriebstätten, Bildungseinrichtungen sowie Verwaltungsgebäude in fortschrittlicher Modulbauweise und arbeitet dabei eng mit seinen Kunden zusammen.
Erfahren Sie mehr