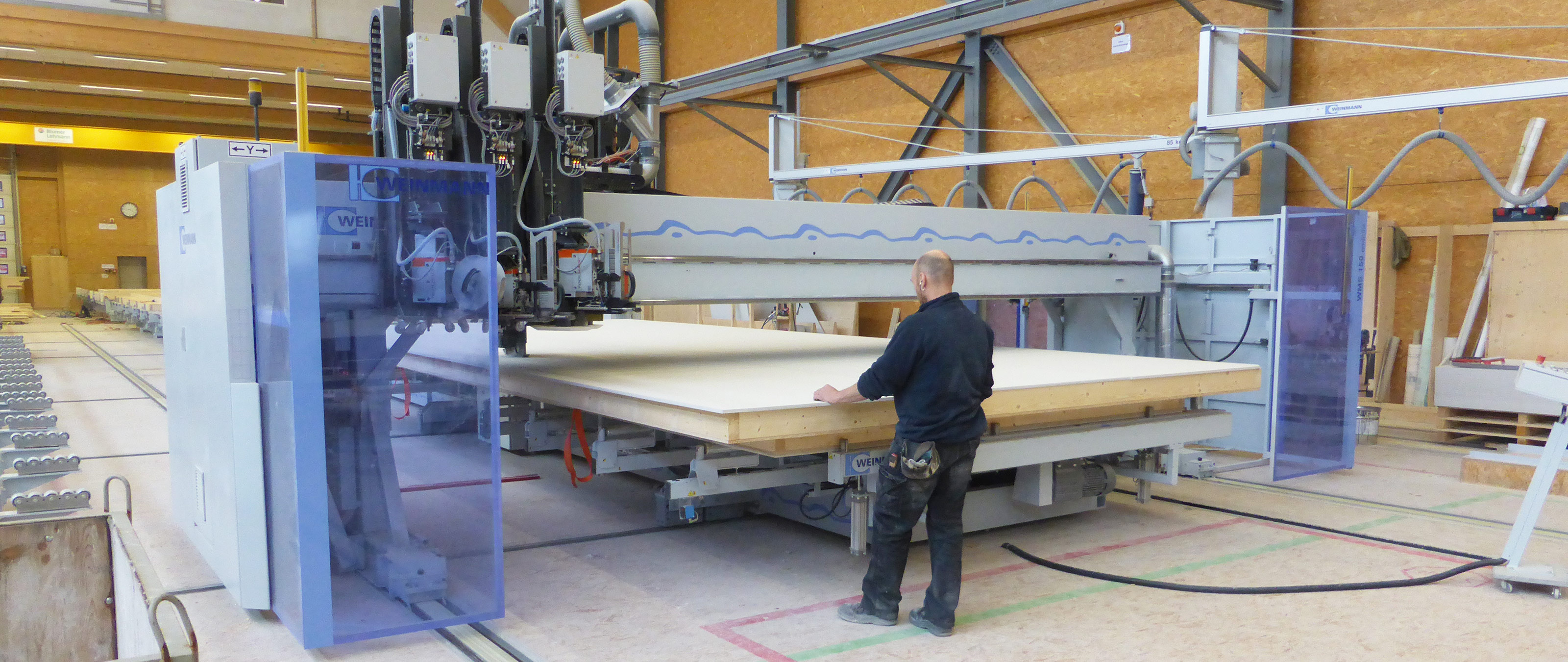
Nicht nur provisorisch
Für zahlreiche innovative Holzbauideen bekannt, gehört die Blumer-Lehmann AG in der Schweiz auch zu den Pionieren des Holzmodulbaus. Ihre hochqualitativen Modulgebäude sind heute auch für Bauherren interessant, die eine hochwertige und dauerhafte Lösung suchen. Gebaut werden sie mit Holzrahmenkonstruktionen, die das Unternehmen auf einer modernen, automatisierten Fertigungslinie produziert.
Zu den Bauweisen, für die der Holzbau geradezu prädestiniert zu sein scheint, gehört auch der Modulbau. Die noch vor einigen Jahrzehnten als "Containerbau" belächelte Bauweise stellt genau genommen sogar eine Potenzierung zentraler Holzbauprinzipien dar, erreicht man mit den fertig ausgebauten Raumzellen doch einen Vorfertigungsgrad von bis zu 90 Prozent. Und eine Qualität, die nicht nur die Auftraggeber temporärer Gebäude anspricht.
Vielseitigkeit auf begrenztem Markt
Zu den Modulbauern der ersten Stunde gehört in der Schweiz die Blumer-Lehmann AG in Gossau, die vor 20 Jahren in dieses Marktsegment eingestiegen ist. Seither hat sie ihre Modulbau- Produkte laut Geschäftsführer Richard Jussell kontinuierlich weiterentwickelt. Dabei agiert sie als Schweizer Unternehmen in einem Markt, in dem viele leistungsfähige, in den letzten Jahren stark expandierte Wettbewerber um ein regional variierendes, durch die Landesgröße und geographische Besonderheiten begrenztes Auftragsvolumen konkurrieren. Eine der Strategien, mit denen man bei Blumer-Lehmann auf diese Marktsituation reagiert, ist die Besetzung unterschiedlicher Geschäftsfelder. So betreibt man in Gossau unter anderem ein Säge- und Holzwerk, eine eigene Pelletierungsanlage und ein Kraftwerk, engagiert sich außerdem in industriellem Maßstab im Salzsilobau. Im Holzbau ist das Unternehmen nicht nur als Modulbauer aktiv, sondern auch im konventionellen Wohn- und Gewerbebau mit Holzelementen, in Umbau und Sanierung, im schlüsselfertigen Bauen, im Bau landwirtschaftlicher Gebäude und im großvolumigen Holzbau von Mehrgeschossern oder Siedlungen. Der Schwerpunkt liegt in all diesen Bereichen auf dem Holzrahmenbau. Hinzu kommen innovative Bautechniken im Freiformbereich oder metallfreie Holzverbindungen für den Mehrgeschossbau. In mehreren Geschäftsbereichen hat das Unternehmen in den letzten Jahren durch innovative Projekte international auf sich aufmerksam gemacht. Bekannt sind zum Beispiel das siebengeschossige, mit metallfreien Holzverbindungen konstruierte Tamedia-Bürogebäude in Zürich oder das Hotel Säntispark, das erste viergeschossige Holz-Hotelgebäude im Kanton St. Gallen. Momentan hat die Blumer-Lehmann AG rund 300 Mitarbeiter.
Modulbau 1: Temporäre Gebäude
Der Modulbau macht etwa 30 Prozent des Produktionsvolumens in Gossau aus. Dies entspricht einer Größenordnung von etwa 2500-3000 Elementen im Jahr und einem Umsatzanteil von 25-30 Prozent. Generell legt man bei Blumer-Lehmann dabei den Schwerpunkt auf hochqualitative Modulbauten in Holzrahmenbauweise - auch wenn diese preislich im oberen Segment liegen: "Zum einen stehen wir für eine Holzbaukultur, bei der die Zimmerei die Verantwortung für den gesamten Wandaufbau übernimmt", erläutert Geschäftsführer Richard Jussel: "Zum anderen sind wir der Meinung, dass die Ressource Holz bei Holzrahmenkonstruktionen besonders nachhaltig genutzt wird." Der hohe Qualitätsanspruch des Unternehmens schlägt sich unter anderem in einem hochwertigen Abdichtungssystem zwischen den Modulen nieder: Ein Blower-Door-Test am fertigen Gebäude gehört dementsprechend zu den Standardleistungen der Schweizer. Geprüft wird außerdem die Luftqualität in den Innenräumen, Zielvorgabe sind dabei die Werte des Labels Gesundes Wohnen des eco Instituts. Dass alle Modulgebäude von Blumer-Lehmann auch energetisch hohen Standards entsprechen, versteht sich vor diesem Hintergrund von selbst. Für dieses Qualitätsniveau lassen sich laut Richard Jussel auch die Auftraggeber temporärer Gebäude begeistern - besonders, wenn es sich um eine Schule oder ein Bürohaus handelt. Nachfrage nach einem solchen Gebäude entsteht zum Beispiel dann, wenn die alte Schule oder das alte Bürohaus saniert oder energetisch optimiert und danach wieder bezogen werden soll. Oder wenn der Bau einer neuen Wohnsiedlung eine kurzfristige Erhöhung der Schulkapazität erfordert, ein Neubau - zum Beispiel wegen langwieriger Genehmigungsverfahren - aber erst in einigen Jahren zu realisieren ist. Die Nutzungsphase einer temporären Lösung kann also durchaus einige Jahre dauern. Modulgebäude bieten in derartigen Situationen den Vorteil, dass man sie kurzfristig am gewünschten Standort in Betrieb nehmen und nach der Nutzungsphase ebenso kurzfristig an einen anderen Standort verlegen kann. Die Schulbehörde kann das Gebäude also mehrfach einsetzen, während ein privater Auftraggeber es vermutlich nach Gebrauch verkaufen wird. Für den von Blumer-Lehmann vertretenen Qualitätsanspruch sprechen vor diesem Hintergrund gewichtige Argumente. Richard Jussel: "Zum einen eine gesunde, angenehme Lern- oder Arbeitsumgebung, die mit dem schier unerträglichen Raumklima in Wohncontainern nicht zu vergleichen ist. Wenn das Provisorium über längere Zeit andauert, lohnt sich ein hochqualitativer Holzbau also in jedem Fall und wird sich in besseren Lernerfolgen und Arbeitsergebnissen niederschlagen. Unsere Kunden haben aber noch einen weiteren Vorteil: Wir bieten ihnen ein geprüftes, ganzheitlich durchdachtes und hochwertiges Bausystem, das am Ende seiner Nutzungsphase seinen Wert nicht verloren hat. Unsere Modulgebäude lassen sich also ohne Abstriche über einen langen Zeitraum wiederverwenden, was sich für öffentliche Auftraggeber in einer langen Laufzeit, für private in einem höheren Wiederverkaufswert auszahlt."
Modulbau 2: Serielles Bauen
Vor diesem Hintergrund verwundert es nicht, dass die Modulgebäude der Blumer-Lehmann AG schon längst über das temporäre Stadium hinaus sind. Schließlich bieten sie auch den Auftraggebern stationärer Lösungen ein Bündel von Vorteilen, die sie als attraktive Alternative zu konventionellen Bauweisen erscheinen lassen.
Hierzu gehört zunächst das breite Spektrum möglicher Zeitvorteile:
- eine kurze Planungs- und Genehmigungsphase dank hohem Standardisierungsgrad
- eine zeitlich komprimierte Abwicklung, da Gebäudeproduktion und Vorarbeiten auf der Baustelle synchron ablaufen können
- eine Fertigstellung des Gebäudes vor Ort in zwei bis drei Wochen mit geringer Beeinträchtigung des Baustellumfelds und ohne Schlechtwetterpausen
- schließlich - teilweise aus diesen Faktoren resultierend - eine hohe Termin- und Kostensicherheit.
Hinzu kommen die Vorteile eines Vorfertigungsgrads, der die Möglichkeiten des konventionellen Holzbaus noch übertrifft:
- hohe Detailqualität und Präzision der Raummodule, die unter industriellen Bedingungen von erfahrenen Teams auf modernen Produktionsanlagen gefertigt werden - inklusive Innenausbau und Finishing
- hoher Standard bei komplexen Gebäudeinstallationen, die in der Arbeitsvorbereitung geplant und in der Raumzellenmontage eingebaut werden.
Vorteile, die den hochqualitativen Modulbau auch bei stationären Projekten mit engem Zeitfenster oder beengten Baustellenverhältnissen als ideale Lösung erscheinen lassen - also zum Beispiel im städtischen Bauen, wo auch die Belästigung im Baustellenumfeld eine zentrale Rolle spielt. Auch bei technisch hochinstallierten oder seriell strukturieren Gebäuden - komplexen Bürohäusern, Kliniken, Labors - spielt der Modulbau seine Vorzüge aus. Dies umso mehr, als er dem Holzbauunternehmen zusätzliche Synergieeffekte beim seriellen Bauen bringt: Als typische Beispiele für diesen Bereich nennt Richard Jussel Hotels oder Altenheime. Dem Holzbauunternehmen ermöglicht die Realisierung derartiger Modulgebäude eine hohe und kontrollierbare Wertschöpfung in der eigenen Montagehalle: "Wir arbeiten in diesem Bereich mit eingespielten Teams aus Fensterbauern, Malern, Gipsern, Sanitär-, Heizungs- und Elektroinstallateuren", erläutert Richard Jussel. "All diese Teams arbeiten effizient am gleichen Montageort und profitieren dabei von weiteren Synergieeffekten, die durch den hohen Standardisierungsgrad des seriellen Bauens entstehen."
Moderne Fertigung mit optimierter Logistik
Schon die Stückzahlen im Modulbau machen es nachvollziehbar, dass die Schweizer 2013 in eine neue Halle und in eine hochautomatisierte Produktionslinie investierten. Rechnet man das gesamte Produktionsvolumen anhand der Angaben zum Modulbau hoch, gibt es eigentlich keine Alternative zu einer industriellen Fertigung: Demnach laufen jährlich 7500 bis 9000 Elemente über die Produktionslinie in Gossau. Entsprechend seinem Schwerpunkt stattete das Unternehmen den Hallenneubau mit einer Produktionsanlage für Holzrahmenelemente aus. Dabei ging es der Firmenleitung angesichts der guten Auslastung weniger um eine Erhöhung der Stückzahl. Im Fokus standen eher ein konstant hohes Qualitätsniveau und eine klare Strukturierung des Fertigungsablaufs. Auch letztere kommt am Ende der Qualität zugute, erlaubt doch ein gut geplanter, klar strukturierter Fertigungsprozess ein umso effizienteres Qualitätsmanagement. Auch in Punkto Mitarbeiterzufriedenheit sah das Unternehmen, das vorher auf engem Raum manuell produzierte, Bedarf für eine Modernisierung seiner Fertigung. Parallel zur Neuaufstellung in der Produktion erhöhte es den Standardisierungsgrad einzelner Module und Elemente. Geschäftsführer Richard Jussel: "Nur mit einer automatisierten Fertigung wird man in der Produktion nicht zwangsläufig schneller. Um ihre Potentiale wirklich auszuschöpfen, muss man auch seine Abläufe und Produkte optimieren." Dazu gehört auch eine gut durchdachte Materiallogistik rund um die Fertigungslinie: Das von WEINMANN konzipierte Hallenlayout legt deshalb Wert auf kurze Wege zwischen Materialdepots und Arbeitstischen, schnelle und ergonomische Handlingsysteme und ausreichend Platz für den problemlosen Materialan- und -abtransport.
Flexibilität und kurze Reaktionszeiten
Im Kern besteht die von WEINMANN gelieferte Produktionsanlage in Gossau aus einer Multifunktionsbrücke WMS 150 und fünf Arbeitstischen. Dieses Fertigungskonzept ist nach Maß auf die im Unternehmen anfallenden Stückzahlen und das breite Spektrum der bedienten Geschäftsfelder abgestimmt: Über die Anlage laufen ja nicht nur Wand-, Dach- und Deckenelemente für konventionelle Holzgebäude und für den Modulbau, sondern auch Sonderbauteile und Fassadenelemente für Hybridgebäude. Auftragsspitzen sind vorprogrammiert, Flexibilität und kurze Reaktionszeiten werden großgeschrieben. So erklärt sich zum Beispiel auch, dass der Fertigungslinie eine Plattenbearbeitung mit Zwischenlager vorgelagert ist. Von hier aus können Beplankungsmaterialien vorkonfektioniert zu den Arbeitstischen geliefert werden, wenn dort besonders viel zu tun ist. Die eigentliche Elementfertigung beginnt bei Blumer-Lehmann mit dem Einlegen und Nageln des Holzrahmens auf Tisch 1. Die Beplankung wird auf Tisch 2 aufgelegt, wo die Platten auch von der WEINMANN-Multifunktionsbrücke zugeschnitten und mit den gewünschten Öffnungen versehen werden. Die Aufteilung dieser Arbeitsgänge auf zwei Tische verkürzt die Taktzeit der Anlage: Auf Tisch 1 kann bereits der nächste Holzrahmen eingelegt werden, während das vorherige Element auf Tisch 2 weiterbearbeitet wird. "Bottlenecks" in der zeitaufwändigen Holzrahmenfertigung werden so vermieden. Balken für Decken- und Dachelemente werden auf Tisch zwei eingelegt, der mit den passenden Fixiereinrichtungen ausgestattet ist. Nach dem Beplanken erfolgt der Wendevorgang von Tisch 2 auf Tisch 3, auf dem die Dämmung und die Installation eingelegt werden - auch dies zeitaufwändige Arbeitsgänge, weshalb sie parallel auch auf Tisch 4 ausgeführt werden können. Quer zu Tisch 5 transportiert, wird das Element abschließend beplankt und noch einmal von der Multifunktionsbrücke bearbeitet. Von Tisch 5 gelangen die aufgestellten Holzrahmenelemente über eine vertikale Wandspur zu einem Verteilwagen und von dort auf einen Hallenkran, der sie auf Pritschen verlädt. Elemente für die Modulproduktion werden zu einer weiteren Wandspur weitergegeben, die in der Modulproduktion endet. Dort lassen sich die Elemente an zehn Modul-Montagepunkten entnehmen, wo sie zu Raumzellen zusammengesetzt und komplett ausgebaut werden. Nur die oberste Schicht des Fußbodens wird erst später auf der Baustelle aufgebracht. Die fertigen, bis zu 12,00 m langen Module werden auf speziellen Lagerplätzen auf dem Firmengelände gelagert, von wo sie bei Baubeginn auf die Baustelle transportiert werden.
Fazit
Ihre primären Ziele - ein klar strukturierter Produktionsprozess und ein konstant hohes Qualitätsniveau - hat die Blumer-Lehmann AG im Rückblick mit der Investition in die neue Produktionsanlage erreicht. In Kombination mit den flankierenden Maßnahmen in der Produktionsperipherie konnte das Unternehmen außerdem seine Produktionszeiten deutlich reduzieren und - trotz eines höheren Aufwands in der Arbeitsvorbereitung - die Produktionskosten senken. Leichte Vorteile bietet die neue Technik dem Unternehmen auch im Marketing. Richard Jussel: "Die klar strukturierte und geordnete Halle passt sehr gut in unser Erscheinungsbild, die Anlage mit ihren präzisen, gut nachvollziehbaren Produktionsschritten begeistert Architekten wie Privatkunden. Unter dem Strich gibt sie ihnen die Sicherheit, dass wir hohe Qualität mit minimierten Risiken liefern. Dazu genügt es freilich nicht, eine solche Anlage anzuschaffen. Mann muss auch darüber reden."
Quelle Bildmaterial: Blumer-Lehmann AG
Ein Artikel des Fachmagazins BAUEN MIT HOLZ, Ausgabe 11/ 2017. Hier lesen Sie den kompletten Artikel.
„Die klar strukturierte und geordnete Halle passt sehr gut in unser Erscheinungsbild, die Anlage mit ihren präzisen, gut nachvollziehbaren Produktionsschritten begeistert Architekten wie Privatkunden. Unter dem Strich gibt sie ihnen die Sicherheit, dass wir hohe Qualität mit minimierten Risiken liefern.“Geschäftsführer Richard Jussel, Blumer-Lehmann AG
Blumer-Lehmann AG
Die Blumer-Lehmann AG plant und baut individuelle Gebäude aus Holz – vom Wohnbau über Gewerbe, Industrie und Landwirtschaft bis zu öffentlichen Bauten und Free Forms. Das Team von Blumer-Lehmann erstellt Neubauten, baut bestehende Objekte um oder saniert sie.
Lesen Sie hier mehr!