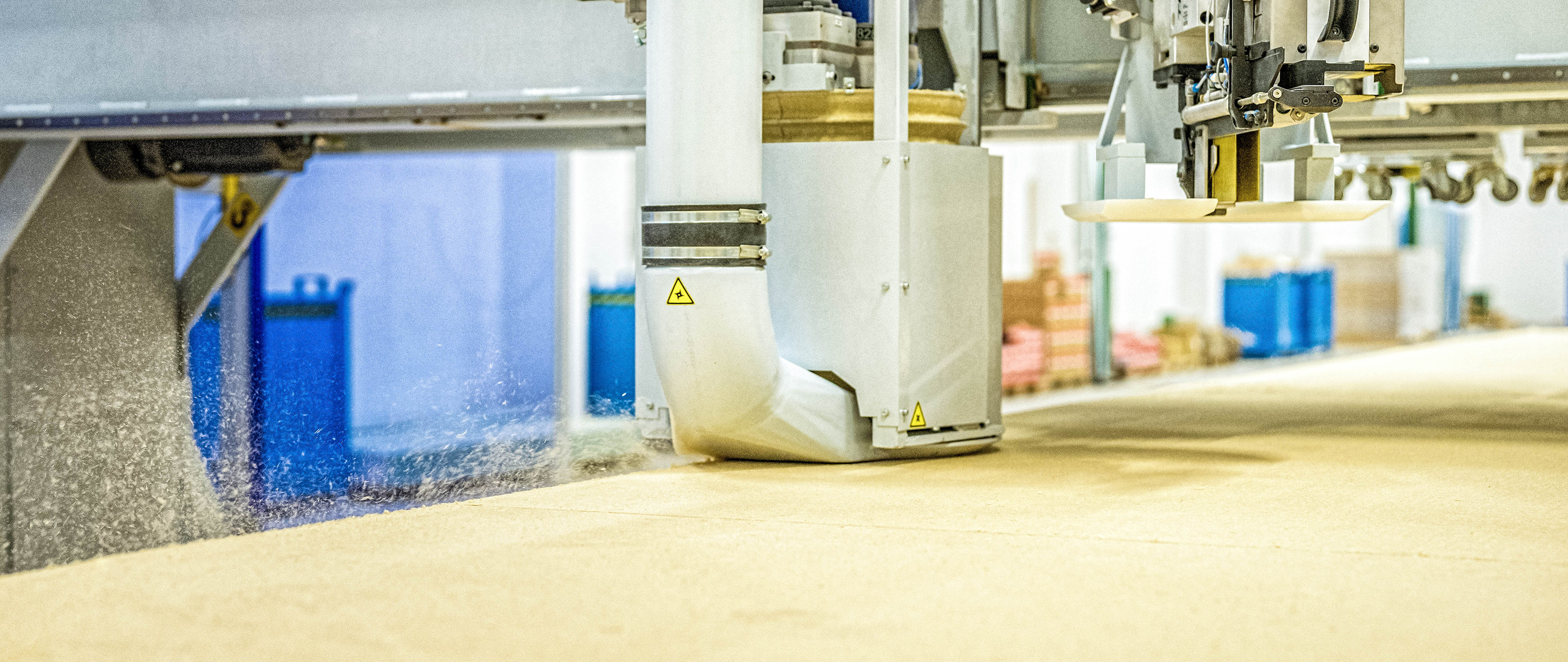
What is important in the production of modern prefabricated housing?
Wolf Systembau has been thoroughly exploring the answer to this question
for the past few years. The results are clear to see—literally:
customers now have the opportunity to watch their own four walls being produced in Scharnstein.
Clear objectives
Wolf began the initial preparations for the new prefabricated housing manufacturing line four years ago. The objective was to integrate the new plant into an existing hall. To achieve this, the building in question was insulated and equipped with a heating system. In addition, a 200-kW photovoltaic plant was installed on the roof of the hall to provide the production line with its own power supply. Ensuring more flexibility while also increasing productivity and quality were central requirements for the production itself. Another
aim was to significantly increase the level of prefabrication taking place in the hall. "Our employees and materials are protected from the weather while at our plant. By decreasing the time spent on the construction site, we also reduce the number of accidents and installation costs," says Wolf's Managing Director Thomas Stadler, explaining the advantages of a higher degree of prefabrication. On delivery,
depending on the customer's requirements, the wall elements are already fitted with full thermal insulation, including mesh and primer on the outside and plasterboard paneling on the inside.
Beam processing system with fully automatic material feed
The concept for the wall and floor production was developed by Wolf in close collaboration with WEINMANN. The beam processing specialists based in Germany's Swabian mountains had previously produced a similar production line back in 2011 at Wolf's German site in Osterhofen. "We have only ever had positive experiences working with WEINMANN. And working with the same system enables us to better network our sites," says Stadler. A major challenge was the integration of the line into the existing hall. Here, WEINMANN had the opportunity to impress with some particularly sophisticated solutions. Particularly remarkable is the compact solid construction timber storage unit with automatic feeding Portal upstream of the WBZ 160 carpentry machine. While the carpentry machine, equipped with 12-slot tool changer and 5-axis technology, cuts the solid construction timber elements to length and carries out all of the necessary trimming processes and adds the required bore holes, a portal system(see Figure 6) automatically feeds raw material into the 60-m3 storage unit. Depending on the requirements, the WBZ can then automatically retrieve up to 20 solid construction timber dimensions. Due to the predetermined room height, the portal is equipped with a special scissor lift system. "With conventional technology, the existing room height would not have been sufficient," explains WEINMANN Sales Manager Michael Marschall. Stadler is very satisfied with the quality of the beam processing: "The speed and precision meet our expectations perfectly."
Wall and floor production
Following the beam processing, the solid construction timber elements move on to be used to produce walls or floors. Staff position the elements on the 12-m-long processing tables and three multifunction bridges take care of the rest. The lap joints trimmed by the WBZ make precise manual positioning of the beams simple. Two WMS 150 bridges create the wall elements, while the floor elements are produced using a WMS 120. These systems primarily attach and process the planking, for example milling the door and window openings or installation ducts. The systems receive the requirements for these processes from CAD data records that are created as part of the work preparation stage. "Most of our prefabricated houses are unique projects, tailored to the customer. This is where the automatic multifunction bridges offer clear advantages. In addition to saving time, the precision is particularly remarkable," says Stadler.
80-km prefabricated house
On average it takes 30 minutes to process a floor element and around 45 minutes for a wall element. "Operating in two shifts, that's 32,000 linear meters of exterior walls, 20,000-m of interior walls and 27,000 linear meters of floor elements per year," explains Marschall. Wolf is aiming for an annual output of around 250 houses, but according to Marschall, the system has a capacity of up to 300 units in two-shift operation. Wolf's bespoke software ensures a smooth production process. "We have assigned every component a barcode. For a holistic production overview, the elements are checked in and out of the individual production stations. That way we always know precisely what the current situation is," explains Technical Director Johann Viechtbauer. The Networking with the raw material storage unit also allows stock to be managed easily and efficiently. To make optimum use of the system, there is also the option of combining several jobs. For example, two 5-m wall elements could be produced as "multi-walls" in a single process and only divided during the last working step.
Europe-wide expansion
Across five European sites, Wolf produces a total of 700 houses per year. In addition to the manufacturing sites in Germany and Austria, an Italian site was also equipped with a WEINMANN line a few months ago. "On this project, WEINMANN proved once again to be an expert partner with the best solution. Using the same system across three sites enables us to absorb additional volumes at a regional level without a problem," the managing director concludes.
“WEINMANN supplied the best solution for our complete production process. Using the same Technology at three Locations, we are able to compensate different production volumes.”Thomas Stadler, Wolf Systembau, Austria
WOLF Haus Austria
With more than 50 years of experience, the WOLF Group has developed into an internationally successful company and is a reliable partner for the construction of prefabricated houses incl. floor slabs/cellars, commercial and industrial buildings, steel construction and agricultural buildings. Wood, steel, concrete and carefully considered material combinations facilitate economic solutions tailored to your individual requirements.
Read more