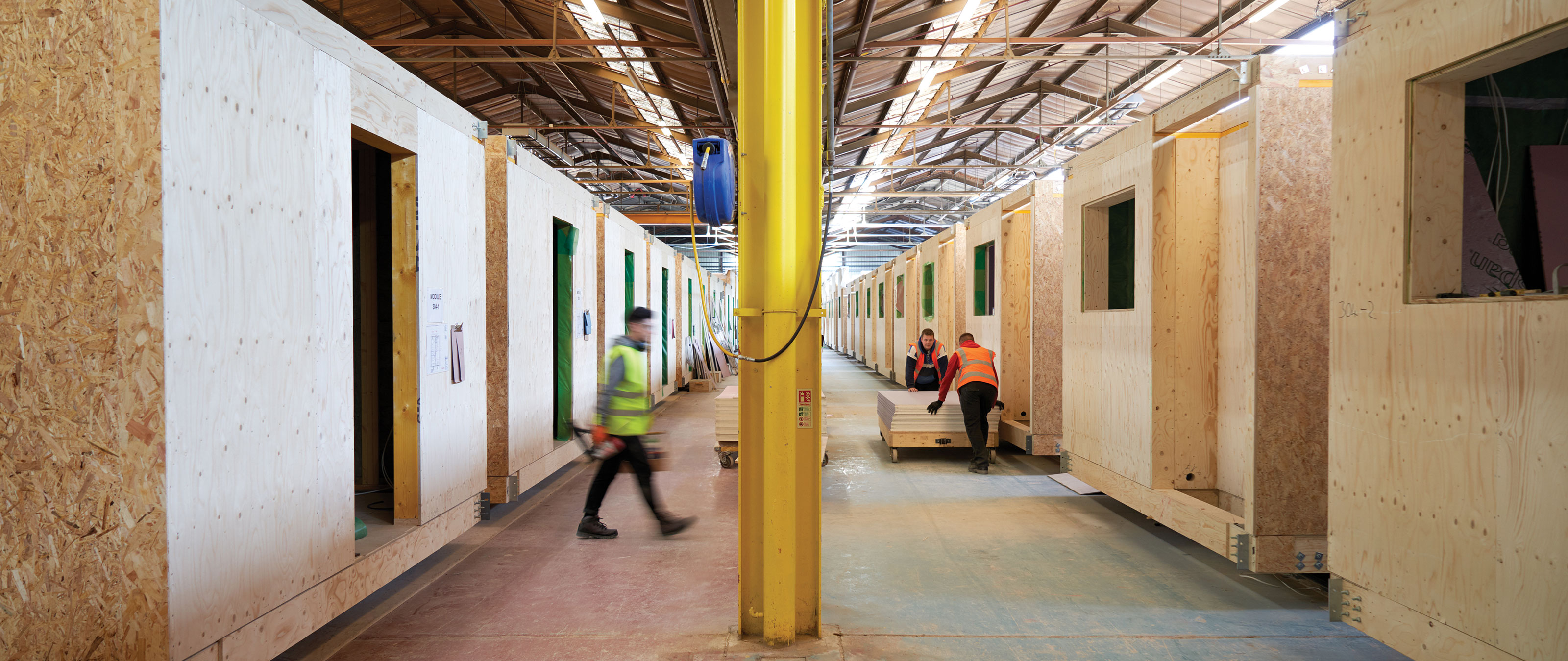
In the UK, the Government has set an ambitious target to build 300,000 homes annually by the mid-2020s but constraints, such as the shortage of skilled workers, mean it cannot meet that target using traditional building methods alone. Consequently, to achieve the target set, a significant proportion of homes must be built using modern methods of construction (MMC). Perhaps the most viable option is to move construction off-site; after all, you wouldn’t dream of trying to make a quality car in the middle of a muddy field in winter and yet every year the construction industry does the exact equivalent – attempting to build quality homes in challenging and less than ideal conditions. Off-site MMC deliver a host of advantages including improved quality, consistency and speed of delivery. The lack of long-term data on the durability of MMC homes in the UK, however, is a considerable barrier to the expansion of such construction methods. Financial service providers, including insurers, mortgage lenders and valuers need to have certainty that MMC homes are safe and durable if they are to engage with them. To address this, leading companies in off-site construction are utilising digital technology to create databases that record the design, processes and materials used in the construction of buildings. Digital technology makes it possible to create a database that stores and tracks data about every aspect of the build. It can also track repairs and alterations and make this information available to relevant stakeholders. Mike Williams managing director of ModularWise, a leading UK manufacturer of off-site constructed modular buildings and extensions for residential and commercial applications, agrees: “As a company, we’ve been manufacturing modular buildings off-site since 2002. In the early days we pioneered the introduction of luxury mobile toilets and since then have gone on to redefine the standards for the quality design and manufacture of modular buildings. “All our products are built to the highest standards to meet individual specifications and all relevant standards and regulations. One of the key reasons we have been able to achieve what we have, is down to a decision we made back in 2016 to partner with WEINMANN, the world’s leading manufacturer of timber frame woodworking machinery and software.“
The tipping point
“In 2010, we’d arrived at a point where we were supplying modular extensions to local authorities in London as part of the ‘Better Homes’ initiative. This included building and installing bathroom/utility and kitchen/utility room extensions at the rate of six a week. To date, we’ve made 800 of these timber-framed modules and have orders for a further 300. “The advantages of off-site modular construction are that the tenants don’t have to be moved out of their houses during the construction or installation phases. Our manufacturing process is much faster than traditional building methods whilst still meeting all building regulations and planning conditions. “The extensions are mounted on helical piles which are installed two weeks before we deliver the units. This means we can handover the new extension within 24 hours of it arriving on site – it’s a very fast and efficient solution. “The success of the modular extensions gave us the confidence in 2016 to invest in a new manufacturing facility in Powys, mid-Wales. This was in addition to our original factory in Herefordshire which still makes the extensions. In the Powys site, we built a complete modular house as an R&D project. “Immediately, there was a huge amount of interest in it and we were approached by a big housing association. They saw the potential and decided to buy a 50 per cent share of our company to help the business to grow and expand. “Since then, the Powys facility has focused on building fully volumetric completed houses on a production line and the Herefordshire factory produces the timber-framed extensions.”
Partnering with WEINMANN
“Up until 2016 we had produced all the timber frames by hand which was not only time-consuming, but also variable in terms of quality and consistency. For the new facility in Powys we knew we had to invest in high quality automated machinery that would deliver the speed, quality, accuracy and consistency we needed for the new venture. “We had no experience of this type of equipment and so we visited Oakwrights, a local specialist in bespoke oak framed builds. They have always invested in the best technologies and recommended we talk to WEINMANN. That proved to be invaluable advice; it led to a relationship which has given us the foundation to grow our business into the multi-million-pound operation it is today. “When we approached WEINMANN they invited us over to Germany and showed us around their manufacturing plant. They also took us to three or four local companies that were using their machinery and software to produce timber frames. “It was all very impressive and so we decided to partner with them. From the outset, it was obvious that they were highly professional and would supply us with machinery and software of the quality and reliability that would give us a good 20-year life expectancy. They clearly understood our business model and we were able to work with them to specify the machinery required for our production line in Powys. “The package we settled on included a FRAMETEQ Framing Station, a WALLTEQ M-120 Multifunction Bridge and a MOVETEQ P-300 Work and buffer Station. At half a million pounds, it was a significant investment for us, but I have to say it was money very well spent. Once our staff had on-site training on the equipment we were up and running very quickly. “The WEINMANN machinery delivers the speed, quality and accuracy that are absolutely essential to our business. Modular housing for local authorities has to adhere to very demanding procedures to meet the needs of council mortgage lenders (CMLs). Before they will grant a mortgage on a modular house it has to have another guarantee which is underwritten by Lloyds of London and is known as the ‘Built off-site Product Assurance Scheme’ (BOPAS). “To get this we have to go through a very rigorous accreditation scheme which is followed up by an extensive quality control system that we have to adhere to at all times. This stipulates that all our timber frames and the way we construct them have to consistently meet a very demanding tolerance of plus or minus 2 mm. “To achieve these criteria we have 120 quality checks throughout the factory for every module that we produce. This enables us to give a 60-year warranty on our products as averse to a traditional build with just a 10-year warranty.”
The advantages of prefabrication
“It all comes down to repeatable quality and really that can only be achieved on a production line, like any product. Why should house building be any different to making a car? A production line built product is far superior in achieving those quality aspects. “It’s interesting that leading house builder has recently announced that it’s going to stop all traditional building of homes and look at modular factory-built solutions. House building is so technical and stringent compared to 10 or 14 years ago when it was just brick and block and done on site in an ad hoc way. “On our production line, every single piece of wood that’s cut or processed is signed off by the individual that does it. Every element goes through quality checks we call gates; before it can go through that gate a supervisor has to sign off the work before it can go to the next process. “By the time it reaches the end of the production it has a final signing off for snagging, and that house module – of which there are four per house – goes with a complete pack of quality management system (QMS) documentation. So, if in ten years’ time there’s a failure we’re able to see who made it, when it was made and who signed it off. That level of traceability is incredibly reassuring and gives local authorities real peace of mind.”
The importance of software
“First-class software is a cornerstone of our production processes. The designers in our office are able to prepare work electronically and send it down to the timber frame workshop where the supervisor has it on his screen and it’s all systems go to produce the work. Without the software, we wouldn’t be able to run an efficient business. “The remote support for diagnostics is fantastic too. We hardly ever have an issue, but when we do it is generally sorted out quickly via the telephone hotline support. We also have a service package which includes annual maintenance to keep the equipment in tip-top condition.”
New developments
“The 80,000 sq. ft. Powys factory now makes all the timber frames for both complete modular houses and the extensions that are made in the 20,000 sq. ft. Herefordshire site. Additionally, we seem to have created a niche for building modular accommodation for ‘traveller’ sites for local authorities. “Every pitch on a new site will have a fully decorated, modular timber frame building with brick on the outside, a slate roof and a high spec bathroom and kitchen. All the timber frames for these will be made in our Powys factory with the most recent order in Sussex being the biggest we’ve received for this type of work. “In terms of our productivity we are now approaching the stage where we will be able to produce one complete house a day off the production line. Currently we’re at three a week, but the aim is to raise that to five a week out of this plant in the very near future. “Most, if not all of our work comes from recommendations. We have always delivered what we said we would on time and in budget, a point the local authorities we deal with really appreciate. We’ve never been late or had any complaints about quality issues which is a real feather in our cap. It means that authorities are happy to recommend us to other boroughs, such as Haringey, who we recently won a tender for not on price (we were actually slightly more expensive), but because of our outstanding quality, experience and delivery track record,” concludes Mike Williams.
An article of our customer magazine performance. Click here to read the whole magazine
“The WEINMANN machinery delivers the speed, quality and accuracy that are absolutely essential to our business.”Mike Williams, CEO ModularWise
ModularWise
ModularWise is a leading UK manufacturer of off-site-constructed modular buildings and extensions for residential and commercial applications. Established in 1990, we pioneered the introduction of luxury mobile toilets – going on to redefine the standards for the quality design and manufacture of modular buildings. All of their products are built to the highest standards to meet individual specifications.
www.modularwise.co.uk