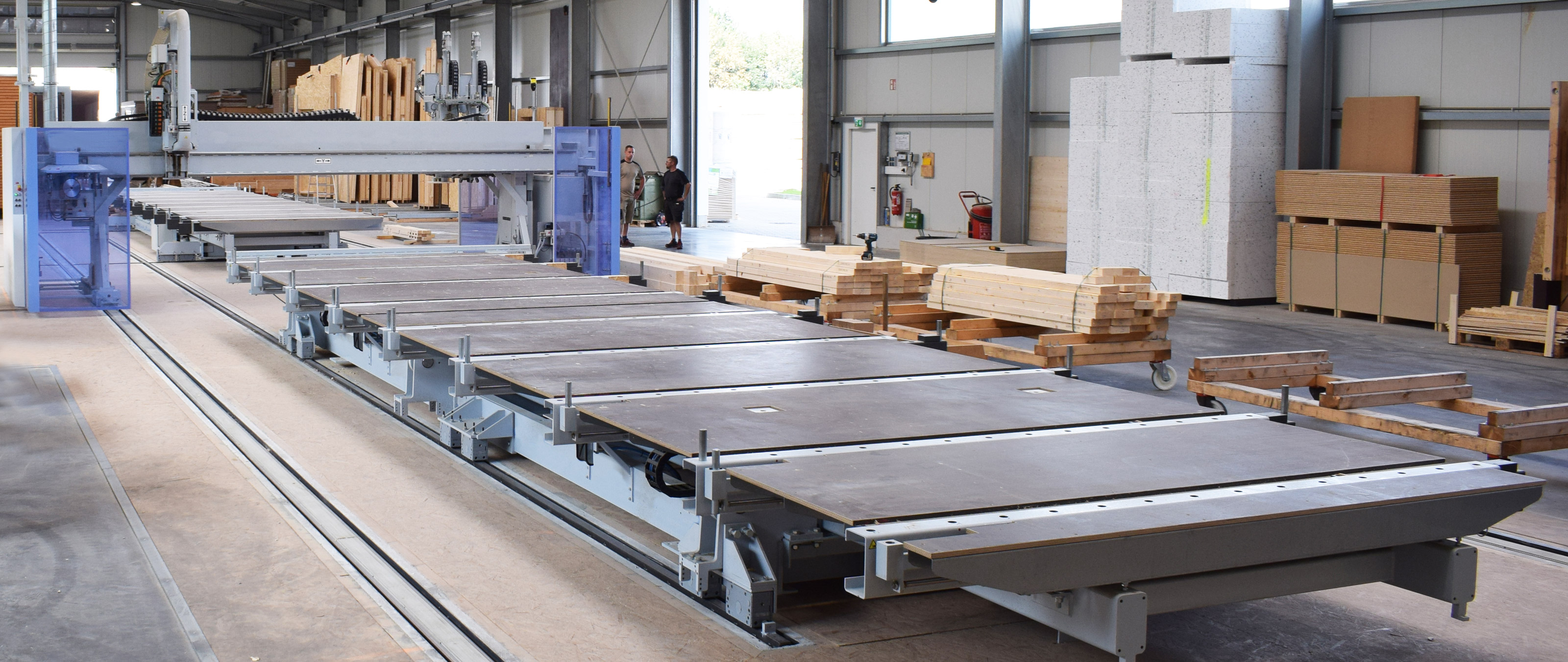
In 2001, Ernst-Otto Rönnau took over the Kurt-Werner Voss carpentry business. Up until that point, the carpentry business had been involved in wood work, produced nail plate trusses and, to some extent, installed these on the construction site itself. Ernst-Otto Rönnau saw great potential in the company and decided to expand the areas of activity in production to have a wider portfolio. At the same time, he wanted to stop the assembly work at the construction site. The industrial business known as Holzbindervoss was created and is still active today.
New areas of activity
In 2010, beam production was added to the production of nail plate trusses, which involved investment in a beam processing system — today, Holzbindervoss has three such systems. Ernst-Otto Rönnau also thought about what carpentry businesses need in addition to beam processing and what services they require. This gave rise to the third large area of activity, wood frame construction. Customer demand in this area increased over the years too. To be able to continue meeting the demand, Holzbindervoss needed greater capacities. Because production was primarily manual and employees were subject to strong physical loads, in 2018, Ernst-Otto Rönnau decided to invest in automation. In his search for the right machine technology, he was impressed by the compact system from WEINMANN. This system enables automated manufacture of closed and open elements, as well as all wall, roof and ceiling elements. Beside the technology, for Ernst-Otto Rönnau the many years of experience in wood work and the proximity were decisive factors: "We were impressed by the good market position and experience that WEINMANN has in Germany."
The compact system consists of one WALLTEQ M-380 multifunction bridge and two BUILDTEQ A-550 assembly tables. This enables Holzbindervoss to produce all elements in an automated process. The frame work is created and the first side of the element is sheathed on the first assembly table. The multifunction bridge attaches the sheathing using clamping devices. All formatting and cut-outs, such as windows, sockets and doors, are also executed with the multifunction bridge. Using the two assembly tables, the element, which is now closed on one side, is turned without using an overhead crane. There is no damage to the element and turning takes only 2.5 minutes. On the second assembly table, the insulation and installations are attached, before the second side of the element is closed and also secured and processed using the multifunction bridge. While the element is being finished on the second table, the employees can create the next frame work on the first table. By investing in the WEINMANN compact system, Holzbindervoss increased its capacities significantly.
Flexible approach
As the company produces wood frame construction elements for various carpentry businesses, it was important for the production system to be versatile. "Every element, every house is different," explains Ernst-Otto Rönnau. "The elements have different thicknesses, wall structures and expansion levels." With the compact system, Holzbindervoss can produce a wide variety of wall elements, as well as roof and ceiling elements, without long setup times. To enable this, the multifunction bridge is equipped with a 12-part tool changer that holds different tools ready. Depending on the processing required, the corresponding tool is inserted fully automatically. There are also two fastening units for attaching different sheathing materials.
Production of the wood frame construction elements has been taking place with the compact system for one year and is now much more structured. Physically demanding tasks have been reduced to a minimum, thus making everyday work more attractive and ergonomic for the employees. Because automated production requires a higher quality of planning, the effort involved in work preparation has increased. The higher quality, beginning with the work preparation right through to the automated production process, leads to a finished element of much higher quality. Ernst-Otto Rönnau: "Our customers appreciate this. The assembly of the elements with precise dimensions on the construction site is much faster."
Bright prospects for wood work
The operating premises of Holzbindervoss cover 35,000 m², with wood frame construction taking up a production area of 1000 m². Based on sales, the nail plate truss area is the largest area, producing 50% of the sales. Beam production and wood frame construction each produce approx. 25%. The aim is to increase sales from wood frame construction to 30%. Compared with southern Germany, the wood work market in northern Germany is significantly weaker, but is growing strongly and is currently at approx. 12%. "The proportion of wood work will continue to increase and prefabrication is a significant factor here. This is because it makes assembly at the construction site easier and faster. The house is erected in the shortest possible time." Ernst-Otto Rönnau is certain "that expanding the wood frame construction area was and is the correct step. The demand from carpentry businesses for wood frame construction elements will continue to increase. We also offer our customers an integrated product portfolio: nail plate trusses, beam processing and wood frame construction."
An article of the magazine Quadriga, edition of 12.08.2019. Here you can read the full article.
“Every element, every house is different”Ernst-Otto Rönnau, HBV Rönnau GmbH
HBV Rönnau
In 2001, the Kurt Werner Voss joinery business, founded in 1968, became the industrial business Holzbindervoss HBV Rönnau GmbH. Since 2010, the areas of beam processing and wood frame construction have been added, in addition to the nail plate truss area. As a medium-sized company, HBV Rönnau offers expert advice on all matters concerning nail plate trusses, wall elements and beam processing and has qualified technicians, engineers and master craftsmen.
Webseite