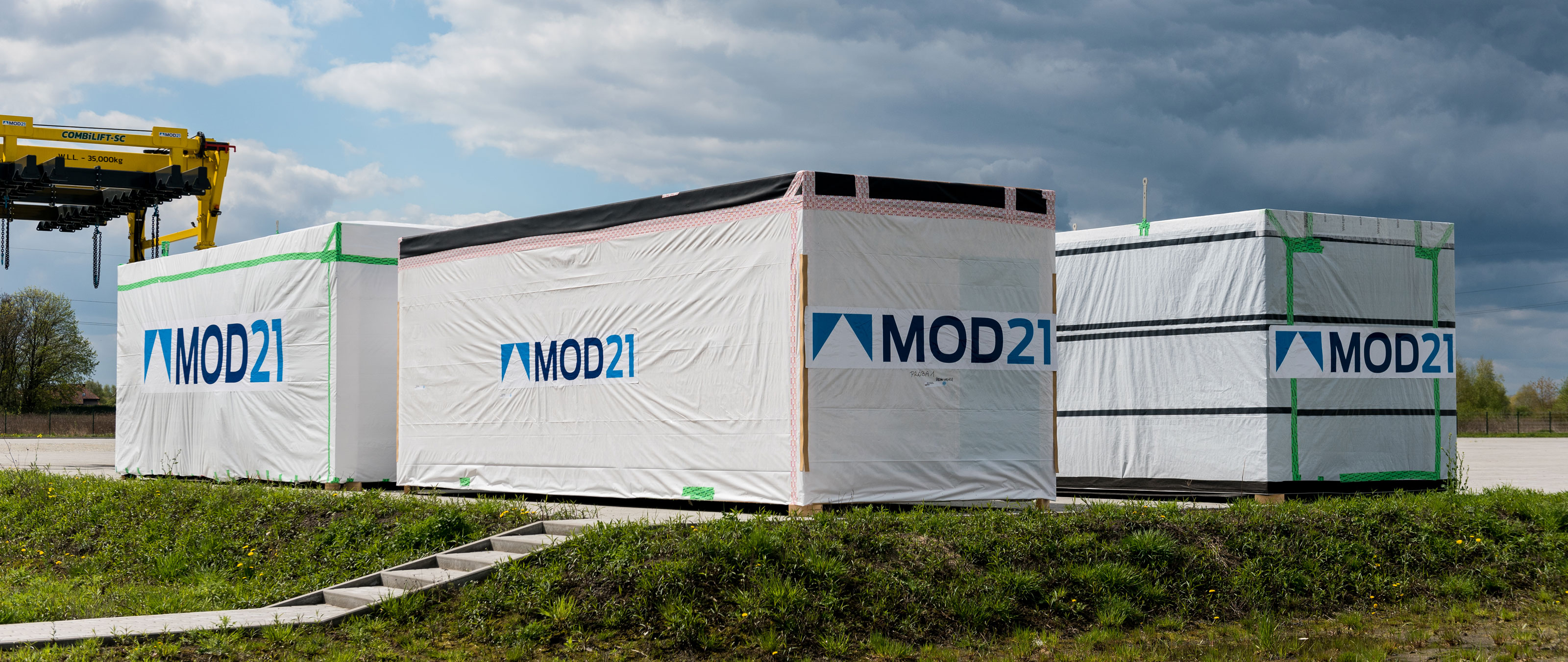
Der Mehrgeschossbau bringt für den Holzbau eine gewisse Internationalisierung mit sich. Diese schlägt sich hierzulande in einer zunehmenden Marktteilnahme ausländischer Unternehmen bei Großprojekten nieder, wobei es sich momentan noch überwiegend um größere Anbieter aus der Schweiz und Österreich handelt. Weitere Big Player auf dem Holzbaumarkt entstehen durch Startups mit Investorenhintergrund oder konventionelle Bauunternehmen, die ihre Aktivitäten in den Holzbau verlagern.
Von konventionell zum Holzmodulbau
Auch die MOD21 GmbH in Düsseldorf ist in diesem Sinne ein alter Bekannter, führte die Tochter der polnischen ERBUD SA doch schon seit 1993 Großprojekte im Raum Düsseldorf aus – damals noch unter dem Namen GWI und ausschließlich in Stahl und Beton. Auch im Stahl-Modulbau hat das Unternehmen langjährige Erfahrung. 2021 erfolgte ein radikaler Neustart, der mit einer Umfirmierung einherging: Auf Initiative des geschäftsführenden Gesellschafters der ERBUD, Dariusz Grzeszczak, der bereits einige Initiativen zum ökologischen Umbau der Gruppe auf den Weg gebracht hatte, erfand sich das Unternehmen unter dem Namen MOD21 neu: Begonnene Projekte werden bis ins kommende Jahr hinein in konventioneller Bauweise zu Ende geführt, neue Projekte werden seit dem 01.01.2022 nur noch in Holzmodulbauweise realisiert. Vertriebsdirektor Marius Schneider: „Angesichts der Klimaziele und der veränderten politischen Rahmenbedingungen – insbesondere der Förderung des seriellen Bauens mit nachhaltigen Baustoffen – liegt für uns die Zukunft im Holzbau.“ Dabei ist die Antwort des Unternehmens auf die neuen Anforderungen am Markt klar und konsequent: Künftig will man – außer im Raum Düsseldorf – selbst für Erdarbeiten, Tiefgaragen etc. nur noch auf externe Partner zurückgreifen. Als Holzmodulbauer ist das Unternehmen quasi ein Startup, kann aber gleichzeitig auf seine Erfahrungen, Referenzen und Kontakte aus 30 Jahren Hochbau zurückgreifen. Die Startbedingungen sind also besser als bei einer reinen Neugründung, zumal das öffentliche und gewerbliche Klientel seine Bauprojekte zunehmend in Holzbauweise realisiert sehen will. Bei MOD21 registriert man vor diesem Hintergrund bereits seit einigen Jahren, dass sich der deutsche Markt für die Modulbauweise öffnet, dass zum Beispiel Architekten sich zunehmend für Modulgebäude interessieren. Marius Schneider: „Es spricht sich immer mehr herum, dass Modulbauten nicht nur Container oder temporäre Lösungen sind, sondern qualitativ hochwertige Gebäude für den langfristigen Gebrauch, denen man ihre Bauweise nicht anmerkt. Insofern sind wir inzwischen auf Augenhöhe mit dem konventionellen Hochbau, bieten aber die konstante, um ein Vielfaches höhere Qualität eines unter kontrollierten Bedingungen vorgefertigten Gebäudes.“
Neustart auf 22.000 m2 Produktionsfläche
Auch wenn der Modulbau derzeit mit rund fünf Prozent noch einen bescheidenen Marktanteil hat, geht man in Düsseldorf von einem exzellenten Wachstumspotential aus. Weshalb man den Wandel zum Modulbau-Startup entschlossen und unter Einsatz beachtlicher finanzieller Mittel in Angriff nahm. Im März 2021 gegründet, erwarb die MOD21 GmbH im polnischen Toruń, dem Gründungssitz der ERBUD SA, ein 150.000 m2 großes Areal, das bereits mit einer 14.000 m2 großen Halle und einem Bürogebäude mit 3.000 m2 Nutzfläche bebaut war. An die bestehende Halle baute man eine weitere mit 8.000 m2 Fläche und offenem Übergang an, so dass man heute über 22.000 m2 zusammenhängende Produktionsfläche verfügt. Die alte, mit sechs Metern deutlich niedrigere Halle, stattete man mit zwei Weinmann Produktionslinien aus, auf denen Wand-, Boden- und Deckenelemente gefertigt werden. Das Layout der Halle erarbeitete man zusammen mit dem Maschinenbauer aus Lonsingen, für den man sich entschieden hatte, „weil man uns hier die überzeugendste Komplettlösung für die Fertigung und eine umfassende Beratung im Umfeld bot, etwa zur Hallenlogistik oder zu möglichen Fördermitteln.“ Die Wandlinie ist hochautomatisiert und verfügt über die gängigen Arbeitsstationen: eine Weinmann-Abbundanlage BEAMTEQ B-660 mit allseitiger Bauteil-Bearbeitung und halbautomatischer Materialzufuhr, eine Riegelwerkstation, den obligatorischen Wendetisch mit Multifunktionsbrücke und zwei Puffertische, auf denen unter anderem die Brandschutzbeplankung ohne Bottleneck ausgeführt werden kann. Die Linie endet in einem Aufstelltisch, der die fertigen Wandelemente an mehrere Verteilwagen weitergibt. Letztere bringen die stehenden Wandelemente in ein achtspuriges Wandlager, in dem sie teilweise einen Finishing-Prozess mit Fenstereinbau, Putz etc. durchlaufen. Am Ausgang des Lagers gelangen sie über einen Verteilwagen und einen Kran in die Modulproduktion. Gedämmt wird aus wirtschaftlichen Erwägungen momentan noch manuell, der Platz für eine WALLTEQ M-300 insuFill ist aber bereits vorgesehen. Auch auf Industrieroboter hat man verzichtet, da für Geschäftsführer Theodor Kaczmarczyk bei den anvisierten Stückzahlen mögliche Nachteile dieser Technik die Vorteile noch überwiegen. Auf der ähnlich ausgestatteten Linie 2 werden Boden- und Deckenelemente produziert. Böden werden am Ende der Fertigung von einem Kran aufgenommen und zur Modullinie in den elf Meter hohen, neuen Hallenteil transportiert.
Modulproduktion in einer separaten Linie
Hier werden sie sofort auf Wagen gesetzt und ausnivelliert, damit die Module beim Zusammenbau absolut im Lot stehen. Anschließend werden die Raumzellen zusammengebaut. Dabei werden sie nicht über Schienen, sondern auf Wagen von Station zu Station bewegt. MOD21-Geschäftsführer Theodor Kaczmarczyk: „Das gibt uns mehr Flexibilität, weil wir die Module auch drehen, diagonal bewegen und je nach Breite in unterschiedlichen Stückzahlen nebeneinander anordnen können. Wenn es einen Engpass gibt, kann ein fertiges Modul auch mal ein noch in Arbeit befindliches überholen.“ Wandelemente werden in einem Takt von 29 Minuten produziert, Boden- und Deckenelemente brauchen 59 Minuten – eine Differenz, die vor allem aus dem höheren Anteil an manuellen Arbeitsgängen resultiert: In den Böden gibt es schräge Verbindungen zwischen den Konstruktionshölzern, die bislang noch manuell geschossen werden. In der Elementfertigung arbeiten derzeit zwölf Mitarbeiter. Raumzellen sind – die Fertigung der Elemente eingeschlossen – nach zwei Tagen fertig. Der Innenausbau benötigt weiter 12 Tage, so dass der Gesamttakt für ein fertiges Modul bei 14 Tagen liegt – inklusive fertiger Installation, Einbauschränken, Küchen und Sanitärobjekten bis hin zur Toilettenbürste im Wandhalter. Dabei arbeitet MOD21 überwiegend mit eigenen Mitarbeitern und setzt nur bei einzelnen Gewerken wie Dach und Fassade, die Nacharbeit auf der Baustelle erfordern, externe Handwerker ein. Der Vorteil: Die Zeit- und Kostenvorteile der in der Halle erbrachten Handwerkerleistungen fließen in die Gesamtkalkulation mit ein. Externe Handwerker sind dagegen noch nicht bereit, diese Vorteile in ihre Leistungen einzupreisen.
Bis 2026 100.000 m2 Gebäudefläche pro Jahr
Fürs erste Jahr hat man sich bei MOD21 mit 30.000 m2 verkaufter und gelieferter Gebäudefläche ein sportliches Ziel gesetzt, liegt aber nach Auskunft von Geschäftsführer Theodor Kaczmarczyk mit diesem Plan gut in der Zeit. 6.000 m2 sind bereits in der Fertigung, der Rest befindet sich in der Pipeline – angesichts der kurzen Montagezeiten im Holzmodulbau ist die Sollerfüllung bis zum Jahresende durchaus möglich – auch wenn private Investoren derzeit wegen der Kosten- und Zinsentwicklung eher verhaltenen am Markt agieren. Bis 2026 will man die Stückzahlen peu à peu auf 100.000 m2 Gebäudefläche erhöhen. Dann wird man in Toruń im Zweischichtbetrieb arbeiten. Eine dritte Schicht ist nicht geplant, wohl aber ein zweiter Produktionsstandort, für den Theodor Kaczmarczyk bereits erste Planungsgespräche mit Weinmann aufgenommen hat. Der neue Standort wird deutlich höhere Stückzahlen ermöglichen und einen deutlich höheren Automatisierungsgrad aufweisen – unter anderem, weil die schrägen Metallverbindungen in Böden und Decken auf einen Vorschlag des Maschinenherstellers hin durch gefräste Holzverbindungen ersetzt werden. Auch Industrieroboter sollen in diesem Werk zum Einsatz kommen. Möglicherweise wird der neue Standort in Deutschland liegen. Dies ist insofern konsequent, als MOD21 momentan ausschließlich Kunden in Deutschland bedient – der Export ins deutschsprachige Ausland ist angedacht, polnische Kunden stehen Modulgebäuden dagegen noch nicht allzu aufgeschlossen gegenüber. Für den Werksstandort in Polen hatte man sich deshalb aus anderen Gründen entschieden. „Wir konnten hier Ressourcen unserer Konzernmutter nutzen“, erläutert Theodor Kaczmarczyk. „Außerdem genießt ERBUD in Polen einen exzellenten Ruf als Arbeitgeber, weshalb wir an diesem Standort absolut keine Personalprobleme haben.“ Kostenvorteile ergeben sich aus der Standortwahl kaum: Laut Theodor Kaczmarczyk ist das Lohngefüge in Polen inzwischen fast auf dem gleichen Niveau wie in Deutschland. „Und weil junge Polen aus diesem Grund lieber im eigenen Land arbeiten, sind wir mit dem Werk zu ihnen gekommen.“ Da der Geschäftsführer den Besuch des Werks dennoch für entscheidend hält, um sich bei Besichtigung der modernen Fertigung und eines Musterhauses mit Showroom und Bemusterungsbeispielen ein Bild von den Leistungen seines Unternehmens zu machen, bezahlt MOD21 Interessenten Reise und Unterkunft.
Planung und Leistungen
Beim Besuch bietet ihnen das Unternehmen bevorzugt die Abwicklung von Projekten an, bei denen die Vorteile einer seriellen Fertigung besonders zum Tragen kommen: Bildungsimmobilien wie Schulen, KITAs und Unigebäude, Büro- und Verwaltungsgebäude, Hotels oder Gesundheitsimmobilien wie Bettenhäuser und Altenheime, außerdem Anbauten und Aufstockungen. Dies mit den inzwischen bekannten Vorteilen des Holzmodulbaus:
eine sorgenfreie Umsetzung, bei welcher der Kunde nur in der Planungsphase und bei der Abnahme gefordert ist, so dass er Personalressourcen spart
ein transparentes Qualitätsmanagement und eine hohe, konstante Gebäudequalität dank weitgehend automatisierter, hochpräziser Fertigungsprozesse unter kontrollierten Bedingungen
eine extrem schnelle Fertigstellung dank hohem Vorfertigungsgrad und paralleler Abwicklung von Baustellen-Vorarbeiten und Modulproduktion
damit verbunden eine kurze Sperrung von Verkehrswegen, eine geringe Beeinträchtigung der Anwohner (Aufstockungen!) und eine risikolose Montage von KITAs und Schulen in der Ferienzeit
eine flexible Nutzung mit Abbau der Module und Neuaufbau an einen anderen Standort, wobei ein großes Gebäude auf Wunsch auch in mehrere kleine aufgeteilt werden kann. Das Demontagekonzept ist bei MOD21 Standard, das Unternehmen bietet seinen Kunden auch Mietmodelle an.
Damit das alles funktioniert, sollte das Gebäude natürlich zum Modulsystem passen. Deshalb hält man es bei MOD21 für sinnvoll, schon in der Planungsphase in ein Projekt einzusteigen. Zwar kann man jeden noch so individuellen Grundriss planen und bauen, mit der Entfernung vom System steigen aber der Zeitaufwand und vor allem die Kosten. Weshalb sich die Planung, die man mit eigenen Architekten, externen Partnern und auch gemeinsam mit Kundenarchitekten abwickelt, in einem modulkonformen System bewegt. Dem gebauten Ergebnis merkt man seine Modul-DNA praktisch nicht an. Dafür sorgen flexible Module bis 12,00 m Länge, 4,20 m Breite und 3,20 m lichte Höhe, die auch unter Transportgesichtspunkten sinnvoll sind. Bei Sonderwünschen sind sie vertikal und horizontal kombinierbar, so dass man auch große Klassenräume, hohe Rezeptionsbereiche oder Treppenhäuser in Modulbauweise abbilden kann. Wo dies nicht möglich ist, kann man auf externe Partner zurückgreifen.
CO2-Rechner auf Basis einer Universitätsstudie
Ein Angebot, das mit seinen seriellen und nachhaltigen Aspekten nahtlos in unsere Zeit passt, wie das Lob von Bundebauministerin Klara Geywitz bestätigt, die das Werk in Toruń kürzlich besuchte. Ebenfalls in die Zeit passt ein Außenwand-Standard, der mit 140 mm gedämmtem Holzrahmenwerk, zwei Gipsfaserplatten innen und einer OSB-Platte mit Vorhangfassade oder WDVS außen die bauliche Voraussetzung für einen guten Energiestandard bildet. Bei MOD21 geht man aber noch weiter: Interessenten können mithilfe eines CO2-Rechners auf der Website des Unternehmens nachrechnen, wie viel CO2 beim Bau ihres Gebäudes freigesetzt wird – kein Showeffekt, steht doch hinter dem Rechner eine aufwändige Studie der Universität Krakau, in die „eine Unmenge der für Bauprojekte relevanten Daten einflossen“. Bei einem aktuellen Projekt – einem Flüchtlingswohnheim mit 3.700 m2 Nutzfläche in München – ergab die Berechnung eine CO2-Einsparung von 97 Prozent im Vergleich zu einer konventionellen Bauweise. „Die LKW-Tansporte schlagen bei uns natürlich zu Buche, weshalb wir derzeit über Wasserstoffantriebe nachdenken“, erläutert Theodor Kaczmarczyk. „Aber die Transporte stehen in keiner Relation zur monatelangen Reiseaktivität von Handwerkern auf einer konventionellen Baustelle.“ Für viele Kunden ist dieser Nachhaltigkeitsaspekt Grund genug, die etwas höheren Baukosten der Holzmodulbauweise zu akzeptieren. Zumal sich die Mehrkosten dank der kurzen Abwicklungszeit relativieren: Wer bis zu 70 Prozent schneller baut, erspart seinem Kunden Finanzierungskosten und ermöglicht ihm, durch Einzug, Vermietung oder Verkauf schneller Geld zu verdienen. Rechnet man diese Vorteile ein, sind Modulbauten in den Augen von Theodor Kaczmarczyk in etwa preisgleich mit anderen Bauweisen.
Ein Artikel aus dem Fachmagazin mikado, Ausgabe 11/2023. Mehr Informationen finden Sie hier.
„Die überzeugendste Komplettlösung für unsere Fertigung und eine umfassende Beratung.“Geschäftsführer MOD21 Theodor Kaczmarczyk
MOD21
Das Düsseldorfer Unternehmen, wurde 1993 im Rheinland gegründet und ist heute bundesweit tätig. Als Teil der europaweit aktiven ERBUD-Gruppe verfügt MOD21 über ein exzellentes Netzwerk und großes Know-How im Bereich Modulbau. Der neue Produktionsstandort wurde innerhalb von nur 12 Monaten Bauzeit errichtet. Auf einer Fläche von 22.000 qm² werden dort ca. 375 m² Modulfläche fast vollautomatisch produziert.
Mehr Infos