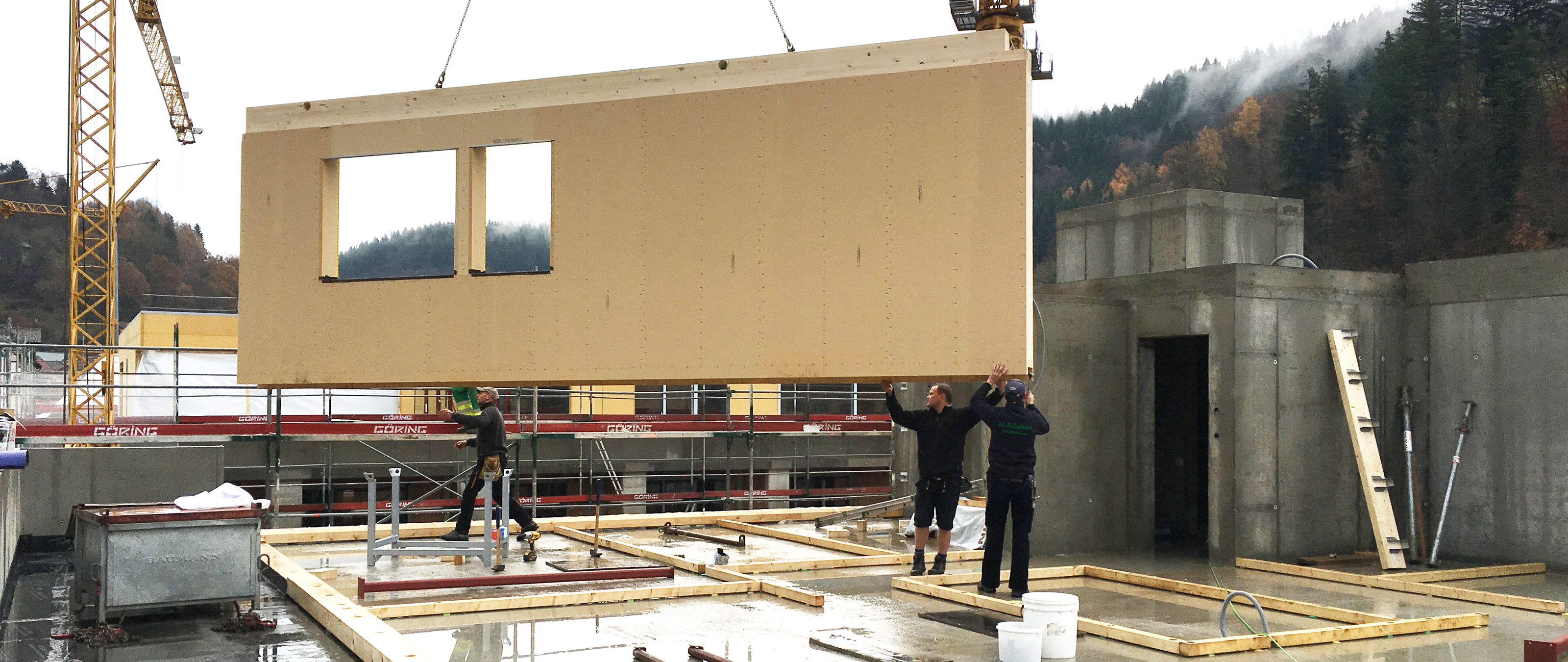
A wood frame construction firm from Schopfheim transitioned entirely to cutting-edge CNC technology over a period of just two years - in a pre-existing, non-custom-built workshop. What prompted M. Räuber Holzbau GmbH to take the plunge and automate its operations? And what has changed since then?
Investment with an eye to the future
M. Räuber Holzbau GmbH is owned by Matthias Räuber, and it was one of his sons - Christoph Räuber - who got to know the company WEINMANN and its products during a trip organized by the training provider Online Meisterschule. He was immediately impressed by its carpentry machines, which sparked an idea that gradually took shape over the course of discussions held after he returned to the family business. After many hours of research, calculations, and visits to other companies, the idea became reality and Räuber invested in the WEINMANN BEAMTEQ B-560 carpentry machine in 2016. The company's own amortization calculations indicated that the decision would pay off, but the fact that this was the first such investment meant that a certain amount of uncertainty still lingered. Today, two years later, no one has any regrets; according to Christoph's brother, Stefan Räuber, "The carpentry machine has absolutely been worth the money." The challenge of integrating the carpentry machine into the existing workshop was a significant one. The WEINMANN machines have an extremely compact design and require no foundation works, but optimal integration into the workshop required careful prior calculations. The machine's infeed and outfeed were shortened to ensure that it could be accommodated in the available space, making it possible to process beams with a length of up to 13 meters, and an excess length option was added, allowing longer beams to be processed within the same footprint, since Räuber often handles beams with a length of up to 14.2 meters. The workforce at the Räuber factory was blown away by the machine and its positive impact on day-to-day operations, and the sense of enthusiasm was immediately palpable. Since the time spent on manual activities is a vitally important but poorly predictable factor in work of this kind, employees also appreciated the fact that they were no longer under such intense time pressure as a result of the high (and predictable) processing speed. According to Stefan Räuber, "The use of machines for joinery tasks allows us to calculate the amount of work involved, and also makes life simpler and easier for our staff since they are no longer under such immense pressure." And the machine's effects have made themselves felt on the construction site as well as in the workshop - accuracy of fit has improved, and the number of simple timber joints and prefabricated drill holes (which are labor-intensive and therefore rarely offered by companies running manual operations) has increased, since the machine can handle everything in one pass. The same is true for joints, as Stefan Räuber explains; "We work a lot quicker with the carpentry machine, which means that we've been able to go back to producing traditional joints again - and not just that, but simple wooden joints without any other fastenings." Examples include dovetail joints which can be assembled as-is, without any extra parts. "This makes the joints cheaper, but it also makes the task of assembly much more pleasant for our guys on site. They get much more out of the job, and together with the improved accuracy of fit this speeds things up yet further," says Stefan Räuber. "Overall, we can achieve an outstanding result for a surprisingly small amount of work, and we only need one or two days on site instead of the previous three or four."
New adventures - new areas of automation
The carpentry machine has had a major impact on the products and services offered by the company, with two inquiries about outsourcing work arriving from the local area as soon as word spread of the automation. But the company is not only exploring new fields - its entire scope of its operations has changed, with an increase in timber frame construction as a result of high levels of interest among building owners and architects. In the words of Stefan Räuber, "We've never seen as much wood as we have over the past two years. What we do has changed a lot, and now encompasses everything from standard joinery through to extensions and even wooden frame home construction." Räuber Holzbau has gradually shifted its focus away from renovations and towards new builds and wood frame construction - meaning that its capacities were pushed to the limit. "Our joining operations were miles ahead in terms of output and quality, and we were unable to produce high-quality elements as quickly as they were needed." Räuber Holzbau's answer? Further automation of element production. The company's decision to make further investments in CNC technology was bolstered by the ongoing skills shortage and the prospect of guaranteeing a consistently high level of quality. Räuber Holzbau has been certified to manufacture closed wall elements since 2017, both for internal purposes and for third-party clients - meaning another increase in demand. Having decided to also automate element production, Räuber Holzbau invested in WEINMANN's WALLTEQ M-380 multifunction bridge, which was combined with the BUILDTEQ A-530 assembly table already owned by the company since 2014. This machine also had to be integrated into the limited space available. WEINMANN and Räuber worked together closely to overcame this challenge, with Räuber making minor alterations to the steel beams and the platform so that the multifunction bridge could be positioned below the platform. As the doors to enter and leave the office building are directly adjacent to the production building, a special safety system was incorporated - red warning lights on the doors are illuminated while the multifunction bridge is operating, and the machine performs an emergency stop if it receives a signal indicating that the doors have nevertheless been opened. These measures were vitally important to maintain high levels of safety while maintaining the existing access route.
Fewer errors thanks to integrated data flows
Automation has also changed the company's approach to planning and preparation. It used to be necessary to add dimensions to all plans manually; panel overhangs or angles for inclined cuts, to name but two examples, had to be calculated and entered into the plans by hand. Quite apart from the amount of work involved, this also posed a high risk of errors. "We don't need to bother with any of that now, since the plans are sent directly from our CAD program to the machine," says Christoph Räuber who - together with his brother, Stefan - is responsible for all the associated preparations. "We spend longer on the preparatory stage, but we spend much less time transferring the plans to the machine, and we're dealing with fewer errors as the data is transferred directly. So our overall workload in terms of data compilation has reduced." The data transferred to the machine is processed directly, and the fact that employees were already familiar with the software and operating structure thanks to their use of the carpentry machine, meant that they could use the multifunction bridge immediately without much training being required. The result? A drop of around 35% in element production times. The process starts with production of the framework on the assembly table, which is fitted with the necessary stops and clamping units for aligning and clamping the elements. The sheathing (fixed and processed using the equipment on the multifunction bridge) is then placed on the finished framework and the element is placed in a vertical position using the assembly table and rotated using the workshop crane. Once the necessary installations and insulation have been added, the second element side is positioned, fixed and undergoes the necessary processes - after which the completed element is made ready for transport.
Custom flexibility for custom-built houses
Every house manufactured by Räuber is different, which means that each of its elements are very unique. After deciding to automate operations, the company needed to find a machine which could satisfy these needs. The WALLTEQ M-380 is specially designed for this very purpose. The integrated 12-slot tool changer accommodates a variety of implements and ensures that the right tool is rapidly available at the right time, set-up times are extremely short and a comprehensive range of processing operations can be carried out. Räuber Holzbau uses a standard and uniform post-and-beam design wherever possible, but customer demands sometimes entail a different approach. The wall panels generally feature soft wood fiber board as a plaster base on the exterior, with cellulose insulation inserted using an insulation plate. An OSB panel is attached to the interior as bracing and a vapor barrier, followed by the installation layer and Fermacell panels.
Optimum use of space
Räuber is now using cutting-edge CNC technology to produce elements in a space measuring just 450 m², of which 138 m² is taken up by element production (assembly table and multifunction bridge) and 150 m² by joinery (the carpentry machine). But the real surprise is that the workshop space is now being used much more effectively. The clearly defined production and material flow means that employees can walk directly to where they need to be, the workshop is clean and tidy and work is more efficient. According to Christoph Räuber, "We used to need a lot of sideways width when we laid out rafters, but the carpentry machine means that materials are taken straight from the warehouse to the machine and from there to the next workstation, with no need to spread them out across the floor. The same is true for element production - since the multifunction bridge operates over the table, the production area available is limited. The employees work in this area and the rest of the space is free." Automation has therefore had a major impact on processes - employees take the time to ensure that the routes along which machines and people need to travel are unobstructed, they organize their own work in order to keep procedures quick and simple, and they also pay more attention to cleanliness and tidiness. According to Christoph Räuber, "Overall, we actually need less space now for production than previously." And there's another side effect of automation - the workshop has become a much more attractive and modern place to work. Stefan Räuber has the following to say; "The new machines have really boosted morale, and the employees who work on them are full of praise." The number of applications for apprenticeship places received by the company has also risen to unprecedented levels, proving that its investments in automation have attracted prospective employees. Räuber Holzbau takes on one apprentice per academic year; it currently employs two, but the figure will increase to three by the end of 2018. Given the problems currently faced by firms looking for well-trained and motivated staff, the company is grateful to have gained an edge in this area.
New opportunities
Räuber Holzbau has discovered that its new machines can be used to complete projects that would previously have been inconceivable - for example, a recent project involving a single element measuring over 10,000 linear meters. Stefan Räuber describes his experience of working with the new technology as follows; "The machines present us with new opportunities and challenge us to accomplish more. We can't get over just how much they can do, and how well everything works. The bridge in particular is just ingenious." A recent project in Switzerland demonstrated that the increases in flexibility and speed which the company hoped to achieve with its investment have indeed materialized. A new story for an existing building - consisting of around 60 elements, 30 of which were walls and 30 of which were ceilings, with 250 m² of floor space, 400 m² of wall surface and 220 m² of roof/ceiling surface - was produced from scratch and delivered in just seven working days. All elements were closed on both sides before being delivered to the construction site. Rapid and flexible response times, short build times and a high level of quality - this was exactly what Räuber was looking for when it invested in the new technology. The company is therefore extremely optimistic about the future, since demand (which is mainly local in nature) is rising not only in the surrounding area, but also in neighboring Switzerland. Businesses such as Räuber have an advantage over large manufacturers of prefabricated houses, because their delivery times are so much shorter. It takes Räuber just eight weeks to manufacture a detached house from the date on which it first receives the order. Demand is also increasing for apartment buildings, extensions, and commercial buildings, and the company now has a clear edge when it comes to custom projects. "What's really great is that someone can come into the workshop in the afternoon and say that they need another wall - we get to work with the drawings, and within an hour it'll be ready. That's the level of flexibility we need, and that's what we have now. We couldn't be happier with our decision to automate operations and invest in our future."
M. Räuber GmbH
The Schopfheim-based wood construction company M. Räuber GmbH has undergone a number of changes and modernization efforts in recent years. It was founded back in 1989 as a traditional carpentry shop in Hausen (Wiesental) by Matthias Räuber, initially with only three employees. In 1994, the company moved to new premises in Schopfheim, after which it moved into new fields of operation and increased its activities in turnkey construction. Matthias Räuber's two sons, Stefan and Christoph Räuber, joined the company in 2002 and 2005 respectively. The company's annus horribilis came in 2013, when the entire building went up in smoke in a fire. The Räuber family was determined to get operations back up and running again, however, and so the new workshop was completed in 2014, and the administration building in 2015. Nowadays the family-run business employs 19 people and focuses on the construction of new houses and extensions, with around 15 houses manufactured and assembled per year. Räuber Holzbau believes that its future is bright and that this figure could rise to as many as 20 houses per year.
An article from Der Zimmermann, 08/ 2018. Here you can read the article.
“The use of machines for joinery tasks allows us to calculate the amount of work involved, and also makes life simpler and easier for our staff since they are no longer under such immense pressure.”Stefan Räuber