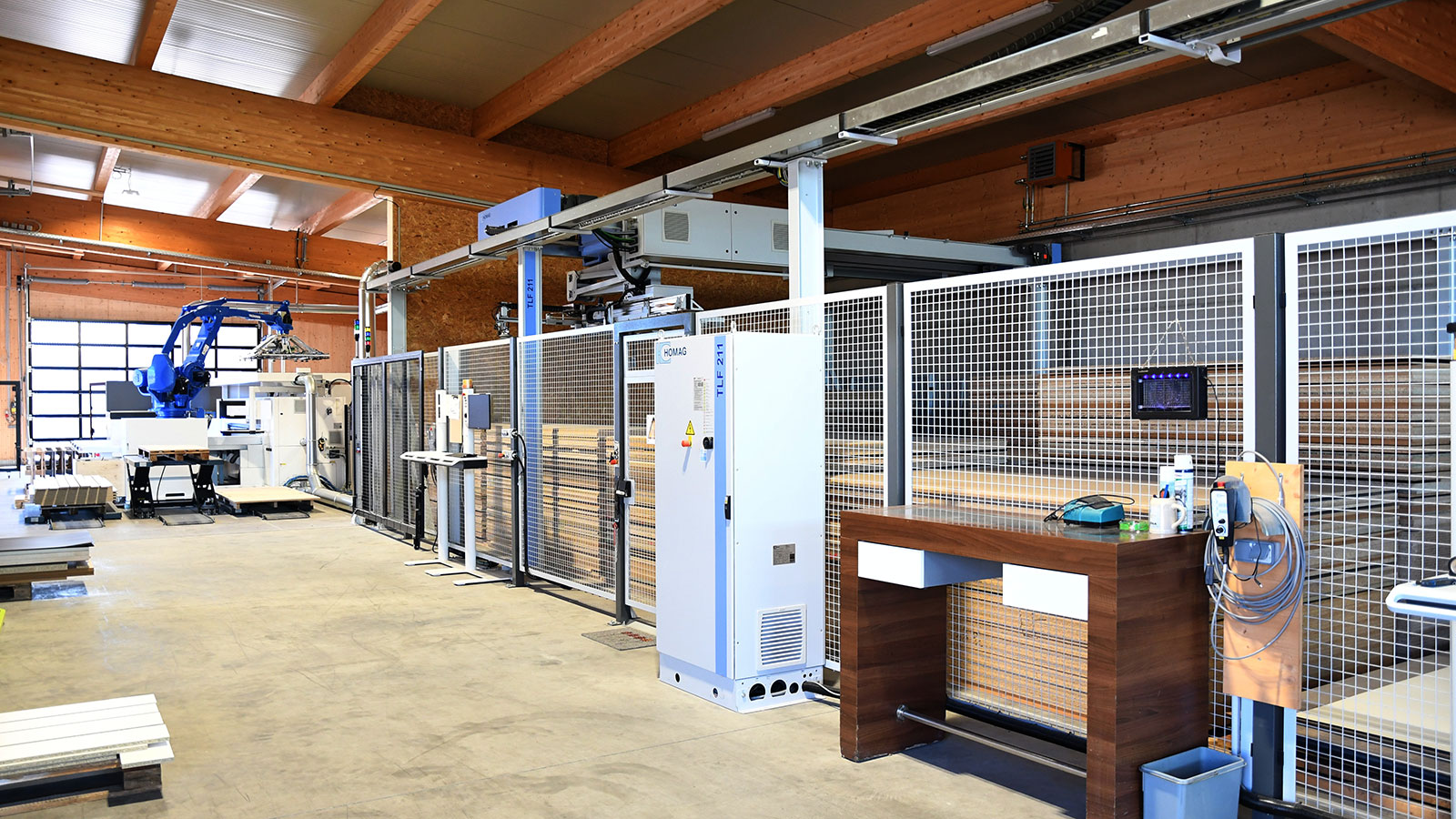
Die Tischlerei Alfred Baumgartner im niederösterreichischen Ruprechtshofen ist ein regionaler Betrieb wie aus dem Bilderbuch: 13 Mitarbeiter, universelle Leistungen, oft in Einzelteilfertigung, höchste Qualität. Dass die Tischlerei dies mit großer Termintreue verbinden kann, verdankt sie nicht zuletzt einer „SAWTEQ B-300 flexTec“ von HOMAG.
Der Termindruck im Handwerk ist hoch. Und er wächst weiter. Zugleich steigen die Ansprüche der Kunden: Oft muss noch schnell ein Extrawunsch umgesetzt werden, und zu fertigen hat der Tischler der Region ohnehin meist das Einzelstück. Hohe Qualitätsanforderungen vor Augen, gibt sich der Kunde nicht mit dem Angebot von der Stange zufrieden. Gleichzeitig können seine Vorstellungen auch bei Kosten und Beratungsqualität zur Herausforderung werden. Und neue Trends beim Material bis hin zur Oberfläche soll das Handwerk ebenfalls immer schneller umsetzen. Dass sich dies vor dem Hintergrund eines zunehmenden Fachkräftemangels abspielt, verschärft die Situation obendrein.
Die wilde Dreizehn
Um solchen Herausforderungen begegnen zu können, muss das Handwerk über neue Fertigungsstrategien nachdenken. Die Tischlerei Alfred Baumgartner hat dies getan und eine erhöhte Effizienz, Flexibilität und Qualität gleich an den Beginn ihrer Fertigung gestellt. Der Auslöser war insbesondere der Zeitdruck, dem der Betrieb zunehmend ausgesetzt ist. „Hinein spielt auch, dass die Arbeitsvorbereitung deutlich zeitintensiver als früher ist. Zeit, die in der Fertigung fehlt. Wir sind nun mal nur 13 Mann. Und keiner mehr. Auch dann, wenn große Projekte kommen“, betont Dominik Baumgartner. 2012 hatte er den Betrieb von seinem Vater übernommen, seither leitet er die 1925 gegründete Tischlerei in vierter Generation. Beide Schwestern arbeiten ebenso im Familienbetrieb: die eine verantwortlich für die Buchhaltung, die andere für die Planung. „Wir planen ja den Innenausbau auf Wunsch von A bis Z durch, wenn ein Hausbauer zu uns kommt“, ordnet der Jungunternehmer ein. Der Leistungsumfang erstrecke sich folglich bis zum Aufbau. „Manche Kunden wollen alles aus einer Hand, und diesem Wunsch kommen wir so weit wie möglich nach.“ Planung, Konstruktion, Fertigung und Aufbau also. „Natürlich setzen wir bei der Inneneinrichtung auch Sonderformen um.“ Damit ginge es so gut wie immer um Einzelfertigung. Viel werde für Privatpersonen gefertigt. „Hinzu kommen Hotellerie, Fremdenzimmer und Wirtshäuser: Etwa 70 Prozent unserer Aufträge sind damit Empfangsbereiche, Theken, Schränke, Zimmereinrichtungen, Wandverkleidungen oder Decken.“ Ein weiteres Segment ist der Objektbau, wo schwerpunktmäßig Trennwände für Büroräume hergestellt werden. Nicht zuletzt springt man immer wieder auch für Kollegen ein, die einen Auftrag gerade nicht schaffen. Was einmal mehr die Personalnöte verdeutlicht ... Und die Notwendigkeit zur Flexibilität: bei der Struktur und Organisation bis hin zu den Mitarbeitern – und eben auch den Maschinen.
Das Generelle gilt fürs Spezielle
Zumal vielfältige Materialien verarbeitet werden. Natürlich Spanplatte und MDF, aber auch Multiplex oder Purenit. „Darüber hinaus fordert die Gastronomie oft wasserbeständiges Material an. Ergänzt um Ein- oder Mehrschichtplatten und beschichtete Materialien, vor allem HPL.“ Vermehrt wird die Spannbreite durch die zahlreichen Teilegrößen sowie den Anspruch, auch sensible Oberflächen hochwertig zu bearbeiten. Was in Ruprechtshofen generell gilt – hohe Flexibilität, Qualität und Termintreue in der Auftragsabwicklung –, gilt im Speziellen auch für den Zuschnitt. Um diese Ansprüche zu erfüllen, wird heute mit einer Lager-Säge-Kombination von HOMAG aufgeteilt, die vor einem Jahr installiert worden war. In Betrieb sind die Robotersäge SAWTEQ B-300 flexTec und ein Flächenlager „TLF 211“ (STORETEQ S-200) seither in einer separaten Halle, die bis dahin als Kommissionierlager genutzt worden war. Dass damit eine strategische Entscheidung gefällt wurde – und das auch noch zum richtigen Zeitpunkt – zeigt das Investvolumen, das samt Gebäude bei rund einer Million Euro lag. Heute werden die Platten in der Halle nach Anlieferung erst vorsortiert, um am Folgetag dann aufgeteilt zu werden. Im Anschluss werden die Bauteile per Stapler an die jeweilige Bearbeitungsmaschine gesetzt, wobei die Tischlerei den klassischen Fluss aus Kantenanleimmaschine, BAZ, Lackieren, Schleifen und Montage realisiert hat. Schließlich wird im Ganzen ausgeliefert und beim Kunden aufgebaut.
Das Besondere, eingebettet im Standard
„Wenn bei großen Projekten ein Mitarbeiter ständig zwischen dem Zuschnitt und der Bekantung hin- und herspringen musste, war das einfach problematisch“, veranschaulicht Baumgartner den Auslöser für die Investition. Umso verlockender war die Aussicht, mit dem neuen Sägekonzept den Mann aus dem Zuschnitt abziehen und für andere Arbeiten einsetzen zu können. Dass dies für ihn von Anfang an abzusehen war, resultierte daher, dass er das anvisierte Konzept bereits kannte. „Die Vorstellung, mannlos zu fertigen, war der Ausgangspunkt“, so der Inhaber. „Und wenn man das will, bleibt nur das Roboterkonzept. Daher sind wir mit genauen Vorstellungen auf HOMAG zugegangen.“ Wie so oft, hingen dann die Sondervorstellungen mit der begrenzten Produktionsfläche zusammen. „Die Säge hätte zwar gut in unsere Halle gepasst, wir hätten aber viel Platz im Lager verloren“, schildert der engagierte Tischlermeister. „Daher wollten wir per Rollenbahn beschicken, was es so bei HOMAG bisher nicht gab.“ Heute laufen die Platten über die gewünschte Rollenbahn, die per Traverse aus dem TLF 211 beschickt wird, direkt an die Maschine. Damit hat HOMAG diesen Sonderwunsch ebenso umgesetzt wie einen bei den Abstapelplätzen. „Von den drei Plätzen haben wir einen aus dem Standard nehmen lassen. So können wir statt 1,2 m nun bis zu 1,35 m Breite abstapeln.“ Dies betrifft vor allem Platten, die als Trennwände Einsatz finden. Wie hier stapelt der Roboter auch die anderen Zuschnitte bearbeitungsspezifisch auf den Scherenhubtischen ab. Von da aus gehen sie entweder in Richtung CNC oder zur Kante; ist keine weitere Bearbeitung erforderlich, wird auch dies beim Abstapeln berücksichtigt. „So sparen wir beim Thema Abstapeln viel Zeit“, nennt der innovative Firmeninhaber ein erstes Ergebnis.
Klassik trifft Moderne
Die SAWTEQ B-300 flexTec selbst ist – wie auch das Flächenlager – im Grunde Standard. Der Schlüssel für die effektive Losgröße-1-Fertigung ist der Roboter: In Kombination mit einer Aufteilsäge, die in Konstruktion und Ausstattung wesentlich einer klassischen SAWTEQ B-300 entspricht, macht er die große Bearbeitungsvielfalt möglich. Erhöht wird diese Vielfalt nochmals dadurch, dass sich die SAWTEQ auch manuell bedienen lässt, zum Beispiel beim Paketzuschnitt. „Die Maschine deckt bis 6 cm ab“, berichtet Baumgartner. „Wir schneiden bis zu 5 cm und nutzen so immer wieder den Paketschnitt.“ Die zweite Schlüsselkomponente der SAWTEQ – diesmal für die mannlose Fertigung – ist das intelligente Abstapelkonzept auf die Hubtische. Die verantwortliche Software sorgt mit ausgefeilten Algorithmen dafür, dass für nachfolgende Bearbeitungen die jeweils passenden Stapel gebildet werden. Die SAWTEQ ist mit einem Laserscanner ausgestattet, der in Echtzeit die Höhe des Stapels misst und für die exakte Höhenpositionierung der Hubtische sorgt. Die Wiedererkennbarkeit der Teile in den Stapeln wird durch die Etikettierung jedes Teils beim Zuschnitt gewährleistet. Neben der Steuerungssoftware „CADmatic 5“ und der Abstapelsoftware arbeitet die zukunftsorientierte Tischlerei zudem mit dem Optimierungstool „Schnitt profi(t)“, das bereits mit der Vorgängersäge ins Haus gekommen war. Für die SAWTEQ musste daher nur auf die „Professionell“-Variante upgegradet werden. „Weil auch die Schnittstelle zu unserer CAD-Software RSO schon etabliert war, konnten wir alle Daten aus der Konstruktion sofort an die Säge übertragen.“
Haus ohne Hüter
Nach einem Jahr Arbeit mit der Robotersäge ist der junge Unternehmer „vollkommen zufrieden. Ich würde sie sofort wieder kaufen.“ Zu Beginn sei er bei der mannlosen Fertigung noch etwas skeptisch gewesen. „Immer wieder gingen wir an die Maschine, um zu sehen, ob sie ihren Job macht“, schmunzelt er. „Heute arbeitet die SAWTEQ vier, fünf Stunden, ohne dass jemand dabei ist. Wir holen nur die fertigen Stapel ab und sehen kurz nach, ob alles in Ordnung ist. Das ist schon alles.“ Gibt es viele Aufträge, wird auch am Wochenende aufgeteilt. Nicht mit dem Mitarbeiter allerdings, der früher an der Säge war. Der wird mittlerweile in anderen Bereichen eingesetzt. Dabei weiß der Inhaber zu schätzen, „dass es ein großer Unterschied ist, ob ein Roboter sägt oder ein Mensch, dem immer mal ein Fehler unterlaufen kann. Allein schon durch unser großes Materialspektrum. Jetzt haben wir wenig Ausschuss und die Qualität stimmt.“ Immerhin kontrolliert die Säge jede Platte, ob sie im Winkel liegt. Sollte die Fläche beschädigt sein, wird auch das gemessen und die Anlage stoppt. Baumgartner ist daher überzeugt: „Die SAWTEQ garantiert uns die Qualität und Flexibilität in der mannlosen Fertigung, die wir für die Einhaltung unserer Termine brauchen.“
Ein Artikel des Fachmagazins Holzkurier. Hier lesen Sie den Artikel auf HOLZKURIER.com
„Heute arbeitet die SAWTEQ vier, fünf Stunden, ohne dass jemand dabei ist. Wir holen nur die fertigen Stapel ab und sehen kurz nach, ob alles in Ordnung ist. Das ist schon alles.“Dominik Baumgartner, Geschäftsleitung