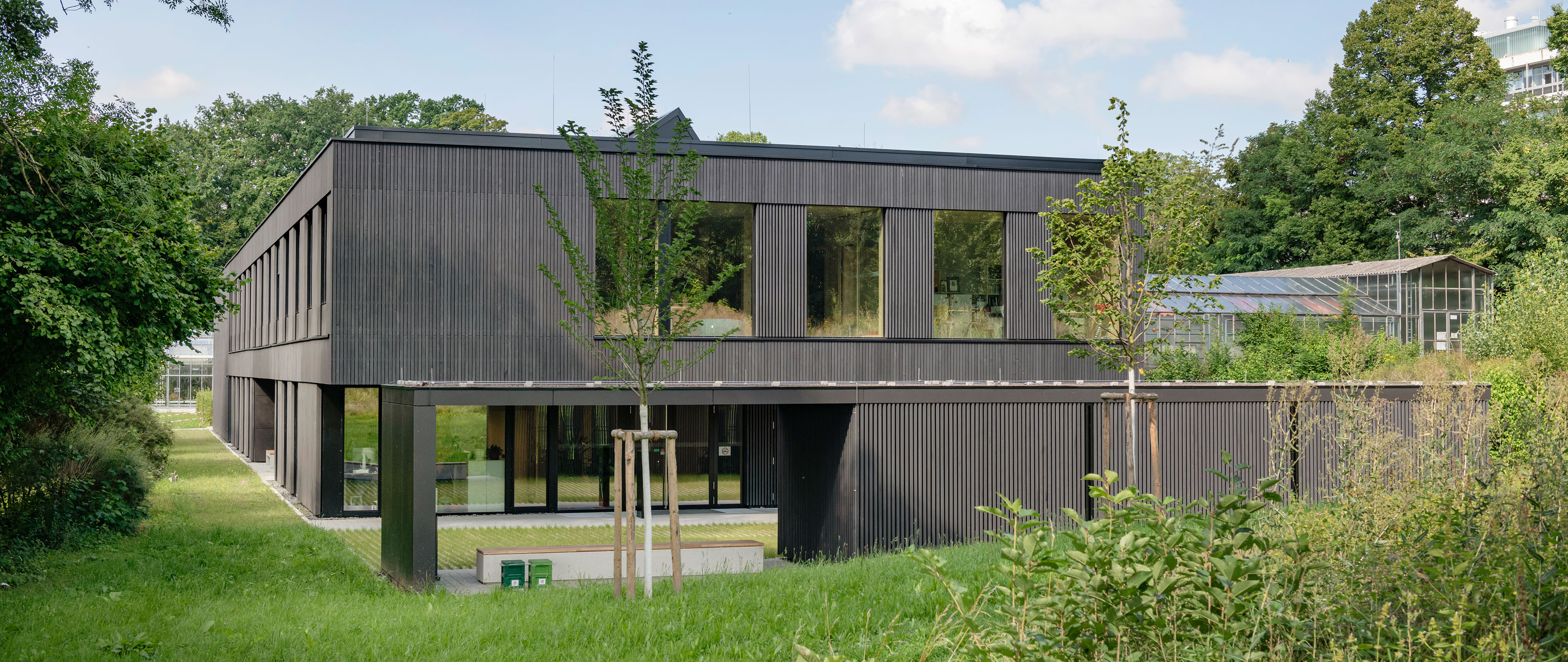
Timber construction is currently undergoing a radical change, in which some observers already see the beginning of a disruption. This includes shifts in the market, which suggest the opening up additional business areas and new providers, investors and startups with innovative ideas, technologies and approaches. On the other hand, in times of climate change, the signs for wood as a building material still indicate growth. Anyone who is well-positioned will also have a good chance of compensating for general declines in the construction sector by growing timber market shares in the future.
Focus on commercial construction
For SYNdikat Zimmerei AG in Reutlingen, Germany, being well-positioned means that the company diversified its business areas years ago, for one thing. Development moved away from the market segment of single-family homes, which the company does still serve today, but which now plays a subordinate role. This process was driven by a chronic lack of construction sites, which the Reutlingen/Tübingen region owes to a high density of population. Today, the focus of the carpentry business is on larger properties. Central business areas are multi-story residential construction, public projects such as schools, kindergartens and university buildings, and occasionally commercial properties, which are not actively solicited. The clients are architects, developers, housing associations and construction groups; many orders come via public tenders, which the carpentry business regularly participates in. Depending on the order constellation, in its projects, the company takes over individual services, the pure construction work or, as a general contractor, the complete, turnkey building. The highlights of the varied new building portfolio include a round school canteen, for which the company delivered and fitted the facade — panels in a sophisticated wood look. An eight-story student residence with 185 apartments for students, built in Reutlingen, is also worth seeing — a reinforced concrete-wood hybrid construction whose wood frame exterior walls come from SYNdikat. In Gönningen, the company recently created eight modern semi-detached houses in wood frame construction with a plaster facade for a developer, and in Ludwigsburg, two four-story buildings with 38 residential units for a housing association — also a wood frame building, here with a wooden strip facade. A very special project is the elongated new building that houses the Apicultural State Institute at the University of Hohenheim. Here, the focus was on sustainable construction, which is why wood was chosen as the construction material. Concrete components in the core areas and the top concrete layer on the ceiling are made of recycled concrete, and the heating requirement of the passive building is covered by the ventilation. Photovoltaic elements cover the residual energy requirement and the flat roofs are extensively covered with grass. The website of the carpentry business also features sophisticated single-family homes with a high energy standard. The list of flagship projects is long and of high architectural quality, as the company usually works together with renowned architects. However, the carpentry business often only comes into contact with the project team at a late stage in proceedings, with the disadvantage that at this point, it is no longer possible to influence the planning. Take, for example, the case of a three-story extension in Stuttgart, which shareholder Andres Lächele would have liked to design as a timber frame construction: "However, since fire protection had already been regulated at the time the contract was awarded, cross-laminated timber was already in the building application." Andres Lächele is one of three shareholders in the company, which was founded as a collective in 1993 — at that time with seven shareholders. It is currently producing a 1200 m2 timber frame commercial hall for a shop fitter that contacted the carpentry business independently. SYNdikat currently employs around half of its approximately 35 employees in the field of renovation. This is an area that contributes significantly less to the annual turnover of 6.5 million than new buildings. However, it does contribute to the broad positioning of the company. Thanks to the promotion of serial renovation, this area of business could also offer interesting prospects for the future — especially in conjunction with financially strong housing associations, with which Reutlingen is ideally interconnected.
Technically fit for the future
If the company does enter this line of business, in Reutlingen, they will be technically prepared for it — the second key aspect of a future-oriented company setup. In October 2021, the company supplemented the WEINMANN flat-pack table purchased in 2016 with a BUILDTEQ A-530 tilt table and a WALLTEQ M-120 multifunction bridge, thus creating the capacity with which the high element requirements for large-scale projects and serial renovations can be met. At the same time, SYNdikat has also created the conditions for a high level of prefabrication with short cycle times by increasing the number of employees in work preparation. "Which wasn't that easy. We have not found any new employees here for a long time." Thanks to these investments, production in Reutlingen is now much faster than before. "We are even significantly faster than I would ever have expected," says shareholder Andres Lächele. But for him, the speed of production is just one side of the coin: "When making the investment, our focus was actually on higher precision through automation." And actually, these goals were initially going to be achieved with a panel processing center. However, it quickly became apparent that the financial step from here to a multifunction bridge with a work table was rather small, but the additional benefit of the automation and precision of additional work steps was all the greater. The decision was therefore made to purchase the bridge, but on the advice of WEINMANN, the company invested in a small solution. This was to avoid overloading the employees at the table and in work preparation with overly complex process steps at the beginning. The result confirms both decisions retrospectively. The transition was marked by the standard rookie mistakes, but it was still smooth and seamless. And it brought new industrial precision across the board — for example, in the nail lines on the sheathing, "where, in manual production, individual nails were always lying next to the stud."
Automation reduces costs
Faster production cycles not only increase the company's production capacity, but also result in cost savings. This is especially the case if additional cost-cutting potential can be used in work preparation via serial effects, for example, in the semi-detached houses or in the two almost identical buildings in Ludwigsburg. "Here, we were able to simply duplicate many identical and similar components," remembers Andres Lächele. "In Ludwigsburg, even entire floors were practically the same. The effort involved in work preparation was therefore significantly reduced, and the synergy effects were also fully realized in production during such a project. We now have significant cost benefits." A welcome added benefit is that the production system can be used for more than just timber frame and roof elements. For example, in the project in Ludwigsburg, the three-layer panels for 24 balconies were processed on the trimming unit, and the CLT compartments between the fire zones were also trimmed on the system, sheathed with gypsum fiberboards and then nailed. The WALLTEQ M-120 also trimmed complex ribs for the roof of a bicycle station in Tübingen. This makes the system even more profitable, especially since it has been running without a break from its assembly in October 2021 to October 2022. Since then, Reutlingen has also been feeling the effects of a stagnant economy. There are gaps in the order book, the convenient order cushion has been used up and the new production system has also been at a standstill for two weeks. "Even property developers and the public sector struggle when construction prices escalate."
An optimistic view of the future
None of this is a threat to the company's existence, especially since the business is just picking up again, because the structure of the economy in the Stuttgart metropolitan area is extremely robust. Andres Lächele also assumes that more and more will be possible in the area of multi-story buildings in the future — not only for hybrid constructions, but also for wooden buildings with cross-laminated timber or beech supporting structures. Against this background, he is optimistic that the construction industry will continue to bounce back: "The demand for housing is huge and everything is pointing toward timber construction, which will secure growing market shares thanks to short construction times, sustainability and a small carbon footprint. We don't have to worry about the market too much, especially since the market share for renovations has risen continuously over the past 20 years and the promotion of serial renovation is further strengthening timber construction." In line with this, two big orders have just been received in Reutlingen — one for a school building in Tübingen and one for a kindergarten in Reutlingen. This means that the trio of shareholders at SYNdikat is slowly considering the next development steps for the company. The first step will be to convert part of a hall that is currently being used as a warehouse. A finishing station, including window installation, is going to be created here. The conversion requires the installation of an additional overhead crane and the construction of a new warehouse. All in all, this is a somewhat tricky task, since the possibilities of the company's plot have been largely made use of already. In a second step, the company is considering a turning table in Reutlingen. At the same time, the plan would be to invest in a new multifunction bridge, "which can do more because it will be equipped with a saw and more carriers. First of all, the structure of the hall must be clarified, and then we will continue step by step." In Reutlingen, there would be some storage capacity in a second hall. The beam processing is located there, and since it consists of a manual snipping saw with an electronic longitudinal stop and waste optimization, there is still space in this hall. There are no plans for a new carpentry machine: "As we only need studs cut at right angles for timber frame and flat roof elements, we are therefore ideally positioned. We get more complex geometries from the beam processing center, and I am often glad that we do not produce them ourselves. With the price structure for beam processing in our region, such orders are often not very profitable."
An article from the trade magazine "mikado," October 2023 issue. More information is available here.
“We are significantly faster than I would ever have expected.”Andres Lächele, CEO SYNdikat AG
SYNdikat AG
SYNdikat AG, based in Reutlingen, was founded in 1990 by just seven self-employed carpenters and has since developed into one of the leading timber construction companies in the region, with around 50 employees at present. SYNdikat AG is a full-service provider with a very comprehensive portfolio of products and services. This includes classic residential and commercial construction in wood frame construction, renovation and restoration, as well as the installation of solar and photovoltaic systems. The company attaches great importance to the issue of sustainability and therefore uses only materials from sustainable sources.
Find out more here.